- 2021-05-26 发布 |
- 37.5 KB |
- 39页
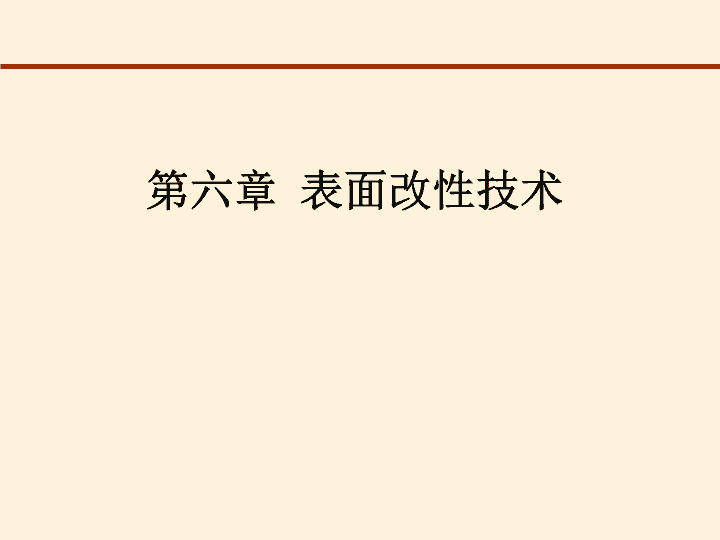
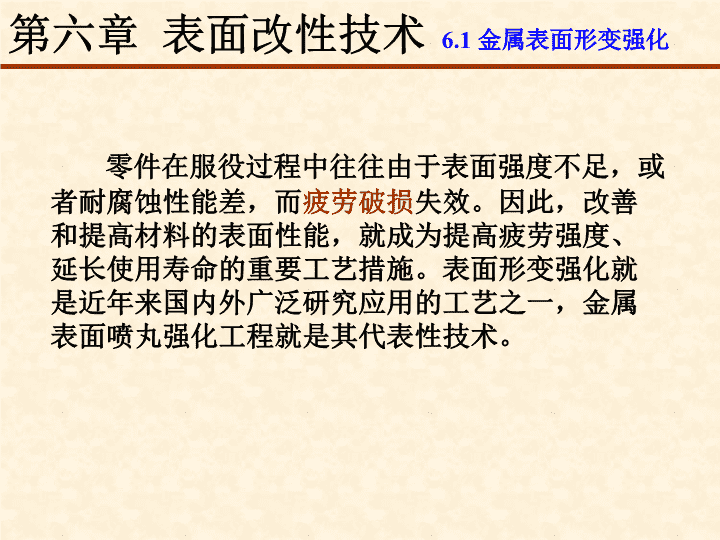

申明敬告: 本站不保证该用户上传的文档完整性,不预览、不比对内容而直接下载产生的反悔问题本站不予受理。
文档介绍
技能培训 材料表面工程学 表面改性技术
第六章 表面改性技术 6.1 金属表面形变强化第六章 表面改性技术 零件在服役过程中往往由于表面强度不足, 或者耐腐蚀性能差,而疲劳破损失效。因此,改 善和提高材料的表面性能,就成为提高疲劳强度、 延长使用寿命的重要工艺措施。表面形变强化就 是近年来国内外广泛研究应用的工艺之一,金属 表面喷丸强化工程就是其代表性技术。 6.1 金属表面形变强化第六章 表面改性技术 金属表面形变强化方法及其应用 常用的金属材料表面形变强化方法主要有喷九、滚 压和内孔挤压等强化工艺。 表面滚压强化示意图。对于圆角、沟槽等皆可通过 该方法获得表层形变强化,并引进残余压应力。 内孔挤压是使孔的内表面获得形变强化的工艺措施, 效果显著。 表面滚压 6.1 金属表面形变强化第六章 表面改性技术 喷丸强化是当前国内外广泛应用的一种表面强化 方法,即利用高速弹丸强烈冲击零件表面,使之产 生形变硬化层并引进残余压应力。已广泛用于弹簧、 齿轮、链条、铀、叶片、火车轮等零部件,可显著 提高金属的抗疲劳,抗应力腐蚀破裂、抗腐蚀疲劳、 抗微动磨损、耐点蚀等的能力。 6.1 金属表面形变强化第六章 表面改性技术 喷丸强化原理: 1)形成形变硬化层, 在此层内产生两种变化: 一是亚晶粒极大的细 化,位错密度增高,晶 格畸变增大; 二是形成了高的宏观 残余压应力。 2)表面粗糙度略有增 大,但却使切削加工的 尖锐刀痕圆滑。 6.1 金属表面形变强化第六章 表面改性技术 表面强化层的组织 变化: 6.1 金属表面形变强化第六章 表面改性技术 表面强化层的组织: 6.1 金属表面形变强化第六章 表面改性技术 强化后残余应力的分布规律 表面为残余压应力,心部为残余拉应力,最表 面层由于应力松驰,其残余应力稍有降低,故曲 线上有“抬头”现象。 6.1 金属表面形变强化第六章 表面改性技术 疲劳强度随表面残余压应力的增加而增加 6.1 金属表面形变强化第六章 表面改性技术 喷丸强化用的弹丸,常用的有三种: 1) 铸铁弹丸 碳质量分数物为2.75-3.60%,硬度 约为HRC58-65,退火后硬度为HRC30-57 。铸铁弹 丸的价格低廉。 2) 钢弹丸 当前使用的钢弹丸一般是将含碳量为 0.7%的弹簧钢丝(或不锈钢丝),切制成段,经磨圆 加工制成,直径为0.4-1.2mm。硬度HRC45-50为 最适宜。钢弹丸的组织最好为回火马氏体或贝氏体。 3) 玻璃弹丸 其应用是在近十几年发展起来的, 已在国防工业中获得应用。玻璃弹丸的直径为 0.05—0.40 mm范围,硬度HRC46-50。 此外,还有陶瓷弹丸、聚合塑料弹丸等。 6.1 金属表面形变强化第六章 表面改性技术 喷丸强化 强化用的弹丸与清理、成型、校形用的弹丸不 同,必须是因球形,切忌有棱角,以免损伤零件表 面。 一般来说,黑色金属制件可以用铸铁丸、钢丸 和玻璃丸。有色金属和不锈钢制件则需采用不锈钢 丸或玻璃丸。 6.1 金属表面形变强化第六章 表面改性技术 喷丸强化设备主要有两类: (1)机械离心式喷丸机,适用于要求喷丸强度高、 品种少、批量大、形状简单、尺寸较大的零件。 6.1 金属表面形变强化第六章 表面改性技术 喷丸强化设备主要有两类: (2)气动式喷丸机适用于要求喷丸强度较低、 品种多、批量小、形状复杂、尺寸较小的零件。 6.1 金属表面形变强化第六章 表面改性技术 (2)气动式喷丸机 压缩空气式 6.1 金属表面形变强化第六章 表面改性技术 重力式喷丸机结构 比吸入式复杂,适合 使用比重、直径较大 的金属弹丸。 6.1 金属表面形变强化第六章 表面改性技术 直接加压式喷丸 机 6.1 金属表面形变强化第六章 表面改性技术 表示喷丸强化质量的三个参数:喷丸强度、覆盖 率、表面粗糙度。 6.1 金属表面形变强化第六章 表面改性技术 1)影响喷丸强度的工艺参数主要有:弹丸直径、弹流速度、 弹丸流量、喷丸时间等。 弹丸直径越大,速度越快,弹丸与工件碰撞的动量越大, 喷丸的强度就越大。 喷丸形成的残余压应力可以达到零件材料抗拉强度的60 %,残余压应力层的深度通常可达0.25mm,最大极限值为 1mm左右。 喷丸强度需要一定的喷丸时间来保证,经过一定时间, 喷丸强度达到饱和后,再延长喷丸时间,强度不再明显增加。 在喷丸强度的阿尔门试验中,喷丸强度的表征为试片变 形的拱高。 6.1 金属表面形变强化第六章 表面改性技术 阿尔门试验 弧高度测试时采用标准化的弧高度试片,也称 Almen试 片。试片分N、A、C三种 ,其材料和硬度都有规定,长度和 宽度也固定,只是厚度不同。其中应用较多的为A试片(厚 1.27mm),适用于中等喷丸强度。 试片在专用的夹具中,接受在一组选定的工艺参数条件 下进行的喷射,然后测量其变形后凸弧的高度作为喷丸强度 的量度。弧高度单位用mm表示。例如,30A表示 A试片弧高 度为0.3mm。 图为不同弹丸速度和喷丸时间的弧高度值曲 线。当喷丸 时间延长时,弧高度先增大,之后逐渐平 稳,呈饱和趋势。 弹丸速度提高(喷丸机叶轮转速提 高),则弧高度全面增大。 生产实际中以弧高度的饱和 值作为喷丸强度。 6.1 金属表面形变强化第六章 表面改性技术 2)所谓覆盖率是指强化后表面弹坑占据的面积与总强化表 面的比值。喷丸覆盖率的影响因素:零件材料的硬度、弹丸 直径、喷射角度及距离、喷丸时间等。 在规定的喷丸强度条件下,零件的硬度低于或等于标准 试片硬度时,覆盖率能达到100%;反之,覆盖率会下降。 在相同的弹丸流量下,喷嘴与工件的距离越长、喷射的 角度越小、弹丸直径越小,达到覆盖率要求的时间就越短。 喷丸强化时,应选择大小合适的弹丸、喷射角度及距 离,使喷丸强度和覆盖率同时达到要求值。 通常覆盖率要求在100% - 200%,有些零件,如曲轴应用 可能要求覆盖率高于200%。 6.1 金属表面形变强化第六章 表面改性技术 3)表面粗糙度的影响因素:零件材料的强度和硬度、弹丸 直径、喷射角度及速度、零件的原始表面粗糙度。 在其他条件相同的情况下,零件材料的强度和表面硬度 值越高,塑性变形越困难,弹坑越浅,表面粗糙度值越小; 弹丸的直径越小,速度越慢,弹坑就越浅,表面粗糙度 值就变小; 喷射的角度大,弹丸速度的法向分量越小,冲击力越小, 弹坑越浅,弹丸的切向速度越大,弹丸对表面的研磨作用就 越大,表面粗糙度值就越小; 零件的原始表面粗糙度也是影响因素之一,原始表面越 粗糙,喷丸后表面粗糙度值降低越小;相反,表面越光滑, 喷丸后表面变得粗糙。 当对零件进行高强度的喷丸后,深的弹坑不但加大表面 粗糙度值,还会形成较大的应力集中,严重削弱喷丸强化的 效果。 6.1 金属表面形变强化第六章 表面改性技术 喷丸强化工艺适应性较广;工艺简单、操作方便;生产 成本低,经济效益好,强化效果明显。近年来,随着计算机 技术发展,带有信息反馈监控的喷丸技术已在实际生产中得 到应用,使强化的质量得到了进一步提高。 喷丸强化在汽车上的应用 凡是承受交变载荷的零件都用喷丸强化工艺。如螺旋 弹簧、板簧、扭杆、齿轮、传动元件、轴承、连杆、凸轮轴、 曲轴等。 汽车板簧的工艺路线:扁钢间断-加热压弯成型-淬火中 文回火-喷丸-装配 6.2 表面热处理第六章 表面改性技术 表面淬火是指采用快速加热,使钢件表层奥氏 体化并立即快冷获得马氏体,而心部仍保持原始组 织的一种淬火工艺。 表面淬火的加热方法有多种,如感应加热、火 焰加热、电接触加热、电解液加热等。其中最常用 的是火焰加热和感应加热两种。 6.2 表面热处理第六章 表面改性技术 一、感应加热表面淬火 目前应用最广、发展最快的一种表面热处理方法。 “集肤”效应 主要适用于大批量生 产的轴、齿轮等零件。 6.2 表面热处理第六章 表面改性技术 一、感应加热表面淬火 感应加热表面淬火是利用电磁感应的原理,使零件在交变 磁场中切割磁力线,在表面产生感应电流,又根据交流电集肤 效应,以涡流形式将零件表面快速加热,而后急冷的淬火方法。 集肤效应(skin effect)又叫趋肤效应,当交变电流通过导 体时,电流将集中在导体表面流过,这种现象叫集肤效应。电 流或电压以频率较高的电子在导体中传导时,会聚集于导体表 层,而非平均分布于整个导体的截面积中。频率越高,趋肤效 用越显著。 6.2 表面热处理第六章 表面改性技术 一、感应加热表面淬火 6.2 表面热处理第六章 表面改性技术 一、感应加热表面淬火 电流频率愈高,电流 透入深度就愈小,硬化层 深度越厚薄。因此应根据 零件所要求的淬火层深度 来选择频率,从而选定设 备。 6.2 表面热处理第六章 表面改性技术 一、感应加热表面淬火 淬火后工件断面组织 6.2 表面热处理第六章 表面改性技术 一、感应加热表面淬火 感应淬火后零件的表面性能 ①高额感应淬火时,在零件 表层中产生较大的压应力, 抗疲劳性能增强; ②感应淬火时马氏体组织细 小,碳化物弥散细小,硬度 高。 ③感应淬火时零件经受激烈 的喷水冷却,使残余奥氏体 量较少,故硬度较高。 ④氧化、脱碳小,组织性 能稳定。 6.2 表面热处理第六章 表面改性技术 一、感应加热表面淬火 感应淬火类型: 根据频率不同,分为中频感应淬火,高频感应 淬火,此外还有超音频感应淬火、双频感应淬火。 表6-9. 6.2 表面热处理第六章 表面改性技术 根据交变电流的频率高低,可将感应加热热处理分为超高频、 高频、超音频、中频、工频 5类。 ①超高频感应加热热处理所用的电流频率高达27兆赫,加热层 极薄,仅约0.15毫米,可用于圆盘锯等形状复杂工件的薄层表面 淬火。 ②高频感应加热热处理所用的电流频率通常为200~300千赫,加 热层深度为0.5~2毫米,可用于齿轮、汽缸套、凸轮、轴等零件的 表面淬火。 ③超音频感应加热热处理所用的电流频率一般为20~30千赫, 用超音频感应电流对小模数齿轮加热,加热层大致沿齿廓分布。 ④中频感应加热热处理所用的电流频率一般为2.5~10千赫,加 热层深度为2~8毫米,多用于大模数齿轮、直径较大的轴类和冷 轧辊等工件的表面淬火。 ⑤工频感应加热热处理所用的电流频率为50~60赫,加热层深 度为10~15毫米,可用于大型工件的表面淬火。 6.2 表面热处理第六章 表面改性技术 600mm冷轧辊工频淬火 6.2 表面热处理第六章 表面改性技术 大型铸钢件工频淬火 6.2 表面热处理第六章 表面改性技术 各种感应加热器 6.2 表面热处理第六章 表面改性技术 二、火焰加热表面淬火 利用氧-乙炔火焰将钢件表层迅速加热到淬火温 度,然后立即喷水冷却以实现表面淬火的方法。其 淬硬层一般为2-6mm。 6.2 表面热处理第六章 表面改性技术 二、火焰加热表面淬火 火焰加热表面淬火设备简单,成本低,但易使钢 件表面过热,质量控制比较困难。因此,它主要适 用于单件、小批量生产以及大型零件如大型齿轮、 轴、轧辊等的表面淬火。 6.2 表面热处理第六章 表面改性技术 三、接触电阻加热表面淬火 利用触头(铜或石墨材质) 和工件的接触电阻,低 电压、大电流,使触点 温度迅速上升。将触点 以一定速度移过工件表 面,即可将表层加热至 淬火温度,并在工件自 身的冷却下淬硬。本法 简易可行,适于大件的 局部表面淬火,如机床 导轨、气缸套等。 6.2 表面热处理第六章 表面改性技术 四、电解液加热表面淬火 以工件作阴极,置于电解液中(常用5%~20%碳酸钠水溶 液),以电解槽为阳极,通入200~300V直流电。由于电 解作用使阴极(工件)表面形成一层氢气膜。氢气膜具有大 的电阻,温度迅速升高,并将工件表面加热到淬火温度。 停电后电解液将工件淬冷。本法适用于大批量生产工件的 局部表面淬火。 6.2 表面热处理第六章 表面改性技术 五、高密度能量加热表面淬火查看更多