- 2021-04-16 发布 |
- 37.5 KB |
- 8页
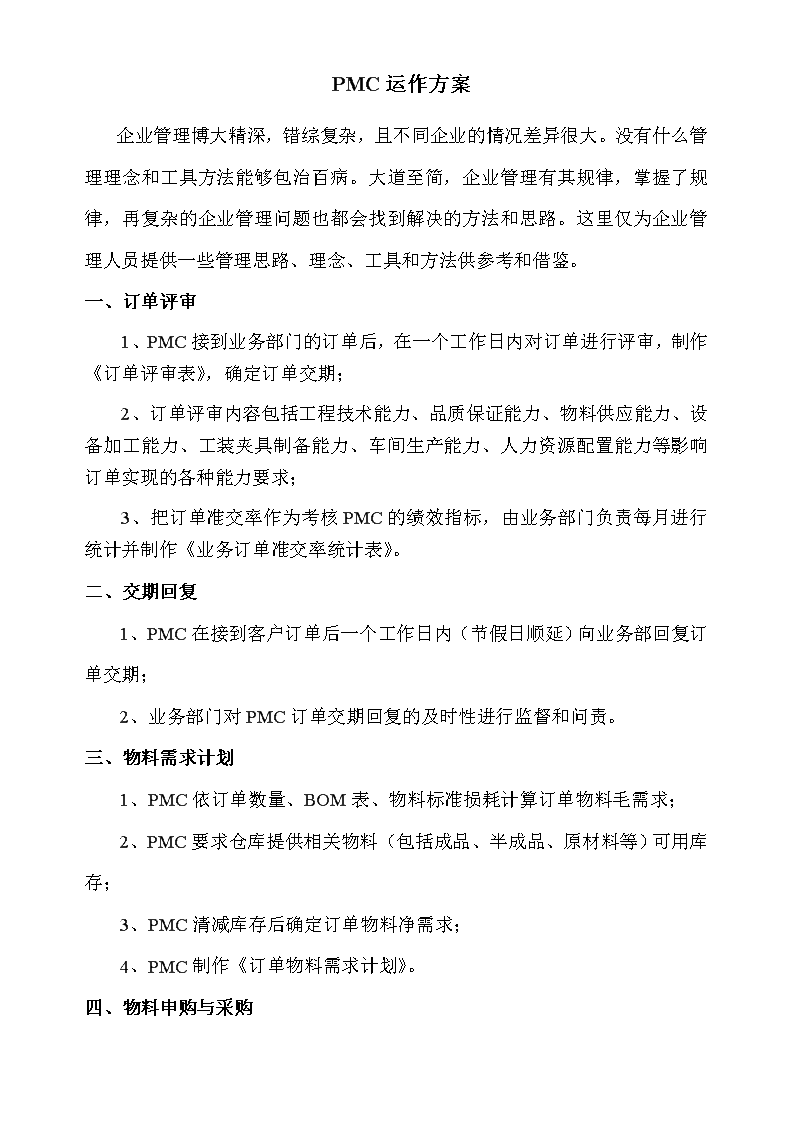


申明敬告: 本站不保证该用户上传的文档完整性,不预览、不比对内容而直接下载产生的反悔问题本站不予受理。
文档介绍
PMC运作方案
PMC运作方案 企业管理博大精深,错综复杂,且不同企业的情况差异很大。没有什么管理理念和工具方法能够包治百病。大道至简,企业管理有其规律,掌握了规律,再复杂的企业管理问题也都会找到解决的方法和思路。这里仅为企业管理人员提供一些管理思路、理念、工具和方法供参考和借鉴。 一、订单评审 1、PMC接到业务部门的订单后,在一个工作日内对订单进行评审,制作《订单评审表》,确定订单交期; 2、订单评审内容包括工程技术能力、品质保证能力、物料供应能力、设备加工能力、工装夹具制备能力、车间生产能力、人力资源配置能力等影响订单实现的各种能力要求; 3、把订单准交率作为考核PMC的绩效指标,由业务部门负责每月进行统计并制作《业务订单准交率统计表》。 二、交期回复 1、PMC在接到客户订单后一个工作日内(节假日顺延)向业务部回复订单交期; 2、业务部门对PMC订单交期回复的及时性进行监督和问责。 三、物料需求计划 1、PMC依订单数量、BOM表、物料标准损耗计算订单物料毛需求; 2、PMC要求仓库提供相关物料(包括成品、半成品、原材料等)可用库存; 3、PMC清减库存后确定订单物料净需求; 4、PMC制作《订单物料需求计划》。 四、物料申购与采购 1、PMC依据物料需求计划制作《物料申购单》发采购部门进行物料采购; 2、PMC制作《采购进度跟进表》,跟进物料采购进度,并对采购准交率进行统计; 3、PMC要求采购部门及时反馈采购异常(包括进度异常、来料品质异常等),并对异常影响的生产计划进行调整; 4、把采购准交率作为考核采购部门的绩效指标,由PMC负责每月进行统计并制作《采购准交率统计表》。 五、外协计划 1、需发外加工的部件,由PMC制作《发外加工计划》,由采购部门进行外发; 2、PMC制作《外协进度跟进表》,每天跟进外协进度,并对外协准交率进行统计; 3、PMC要求外协部门及时反馈外协异常(包括进度异常、外协品质异常等),并及时对生产计划进行调整。 4、把外协准交率作为考核采购部门的绩效指标,由PMC负责每月进行统计并制作《外协准交率统计表》。 六、备料计划 1、PMC于每周六前下达下下周《周备料计划》给仓库进行备料(帐面备料); 2、PMC要求车间提前三天制作备料计划下达给仓库进行备料(实物备料); 3、PMC和车间跟进仓库备料进度; 4、PMC要求相关部门(车间和仓库)及时反馈备料异常事项并进行协调解决; 5、PMC统计各部门备料计划达成率并进行公布(具体数据由仓库提供); 6、PMC对影响备料计划达成的责任部门和人员进行责任认定并问责。 七、物料领用与发放 1、PMC根据订单数量、BOM表、标准损耗制定《订单套料表》; 2、PMC监督车间依《订单套料表》到仓库领取物料,车间不得超套料单领料; 3、PMC监督仓库依《订单套料表》备料和发放,仓库不得超套料单备料和发料; 4、PMC监督生产依《订单套料表》及标准损耗使用物料,生产不得超计划使用物料; 5、物料丢失、损坏、报废、不良需补料的,由车间填写《补料申请单》经相关部门和PMC签字后方可到仓库补料,仓库凭有效《补料申请单》进行发料。 八、生产主计划 生产主计划是工厂所有订单的生产排程,PMC通过主计划对工厂的生产能力、负荷能力、新订单交期进行掌控,并依据生产主计划确定冷冻滚动生产计划。 1、订单完成评审确定交期后,PMC根据客户订单数量、订单交期、产能标准、标准工时、产品工艺路线、生产能力、负荷能力、采购周期、外协周期等制作《生产主计划》; 2、《生产主计划》制作完成或更新后,当天内传送一份给业务部门。 3、业务部门对PMC《生产主计划》传递的及时性进行监督和问责。 九、冷冻滚动生产计划 1、PMC根据《生产主计划》制作《冷冻滚动生产计划》; 2、PMC在每周六15:00前制作下一周的《冷冻滚动生产计划》,并签发到各生产车间; 3、各生产车间对《冷冻滚动生产计划》进行审查,有异议需在半个工作小时知会PMC进行沟通解决。 4、车间监督PMC是否准时下达《冷冻滚动生产计划》,并进行横向问责; 5、PMC监督检查各车间是否按《冷冻滚动生产计划》安排生产,并进行横向问责; 十、出货计划 1、PMC根据《主生产计划》和《冷冻滚动生产计划》制定《出货计划》; 2、PMC每周六前制定下周的《出货计划》,并将《出货计划》分发给业务、车间、品管、仓库等相关部门,各部门提前做好出货准备。 十一、插单与补单 1、由PMC负责对业务插单和补单进行监督和考核; 2、PMC每周、每月统计业务部门插单和补单次数,制作《订单插单和补单统计表》并进行公布; 3、原则上PMC可以拒收插单和补单,特殊情况下插单和补单必须经总经理签字后PMC方可接收; 4、PMC接收插单和补单后,应立即对主生产计划进行调整,并同步调整冷冻滚动生产计划。 十二、产前准备 不打无准备之仗,生产前PMC应对各项生产准备工作进行检查落实,原则上没有做好产前准备工作的订单不安排生产。 1、PMC在安排生产前,应对生产前各项准备工作进行检查和跟进; 2、PMC检查各部门产前准备情况,对影响产前准备的责任部门和责任人进行问责; 3、PMC应及时排查产前工作的异常情况,并及时进行协调解决(如物料配套情况、工装夹具制备情况、设备运行情况等); 4、对因产前准备不充分而对生产计划的达成造成影响的,由PMC进行责任认定和问责; 5、产前准备的内容包括:工程技术资料、品质保证、物料配套、工模夹具制备、设备运行、人员配置等。 十三、生产统计和进度跟进 1、PMC每天统计车间生产数量,跟进车间生产进度; 2、PMC每天不定时到各车间检查生产情况,发现异常及时进行调整; 3、PMC要求车间每天9点前提供前一天的生产日报表,对未提交生产日报表的车间进行问责; 4、PMC统计各车间生产计划达成情况,对未达成的生产计划要求查明原因,追究相关责任人的责任,并根据实际情况对生产计划重新作出调整。 5、把生产计划达成率作为考核车间的绩效指标,由PMC负责每周、每月进行统计,制作《各车间生产计划达成率统计表》并公布。 十四、生产异常反馈与协调 1、PMC要求各相关部门及时反馈影响生产计划达成的异常事项,对未及时反馈生产异常而对生产计划造成影响的,追究相关人员责任; 2、PMC组织相关部门对异常事项进行协调解决,跟进异常解决进度; 3、PMC对生产异常事项进行统计,要求相关部门限期进行整改; 4、PMC制作《生产异常统计表》,并于每周、每月进行公布; 5、PMC对影响生产计划达成的异常事项进行责任认定并进行问责。 十五、产能分析与瓶颈工序分析 1、PMC对各车间各工序的生产能力进行评估,制作《工序产能分析表》,作为制作生产计划的依据; 2、PMC对各工序的产能负荷进行评估,查找出瓶颈工序并及时进行调整; 3、PMC对生产过程进行控制,保持上下工序之间物流平衡,确保各工序按流水线节拍进行生产,实现在制品在各工序间快速流转,减少中间库存; 4、车间按PMC要求进行瓶颈工序的调整,包括人员调整和工作时间调整等; 5、因缺乏产能分析或瓶颈工序调整而导致产品工艺路线上的相关工序节点不平衡,造成产线停工待料或加工件积压,对相关部门和人员进行问责; 6、根据生产负荷,PMC对业务部门的营销策略提出建议,包括订单优化、客户分级等。 十六、库存控制 1、PMC严格按订单数量和标准损耗安排生产,不得超计划生产,特殊情况下必须经总经理审批; 2、PMC严格按订单物料需求和物料标准损耗制定物料申购计划,不得超计划申购,特殊情况下必须经总经理审批; 3、PMC严格按订单物料需求和标准损耗制定外协计划,不得超计划外协,特殊情况下必须经总经理审批; 4、PMC主导制定《常用物料安全库存》,仓库依据安全库存进行申购; 5、车间生产物料的申购原则上由PMC和仓库进行申购,车间主任直接进行申购的,必须经PMC签字确认后,采购部门方可接单采购。 6、对造成库存积压的责任部门和责任人,视具体情况进行问责。 十七、统筹协调 1、以PMC为中心,围绕生产计划对各部门工作进行统筹协调; 2、各部门必须配合和执行PMC制定的各项工作计划,并保质保量按时完成计划; 3、PMC监督检查各相关部门工作计划的完成情况,并进行横向问责; 4、PMC在必要时召集相关部门会议,协调解决与生产计划相关事宜; 十八、生产协调会 1、PMC每天15:30组织相关部门召开生产协调会,跟进生产、采购、外协进度,解决生产异常,协调各部门工作,使各部门的工作能够协调一致; 2、PMC对未达成的计划项进行责任认定和问责; 3、生产协调会必须形成相关《会议记录》,制定相关会议决议,并及时分发给与会人员; 4、PMC跟进相关会议决议执行情况,对未完成会议决议的责任部门和人员进行问责。 十九、生产周例会 1、PMC每周组织相关部门召开一次生产周例会; 2、生产周例会应对前一周的生产情况进行总结,对下一周的生产计划进行安排,并对相关部门的工作绩效进行评价; 3、生产周例会必须形成相关《会议记录》,制定相关会议决议,并及时分发给与会人员; 4、PMC跟进相关会议决议执行情况,对未完成会议决议的责任部门和人员进行问责。 二十、专项会议 1、PMC根据实际情况不定时组织相关部门召开专项会议,解决与生产有关的专项问题; 2、专项会议也必须形成相关《会议记录》,制定相关会议决议,并及时分发给与会人员; 3、PMC跟进相关会议决议执行情况,对未完成会议决议的责任部门和人员进行问责。 查看更多