- 2021-04-16 发布 |
- 37.5 KB |
- 1页
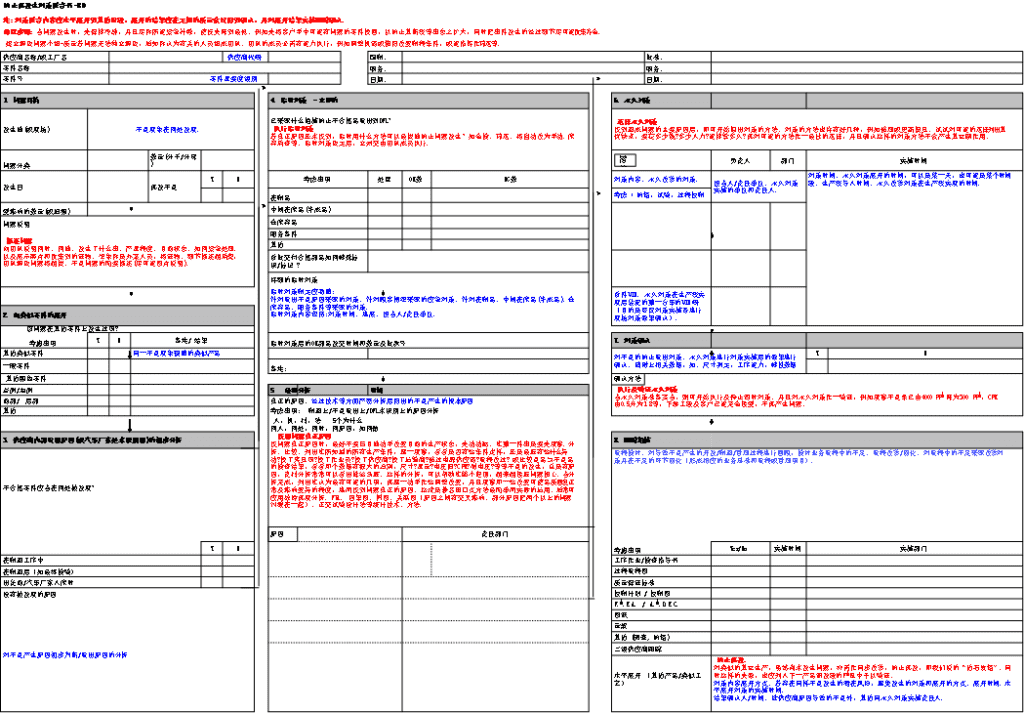
申明敬告: 本站不保证该用户上传的文档完整性,不预览、不比对内容而直接下载产生的反悔问题本站不予受理。
文档介绍
8D报告模板
防止再发生对策报告书 -8D 注: 对策报告内容应水平展开到其他阶段,展开的结果应在定期的质量会议得到确认,并对展开结果实施跟踪确认. 前置步骤: 当问题发生时,先保持冷静,并且尽你所能紧急补救,使损失降到最低。例如先将客户手中可能有问题的零件换回,以防止其断线等事态之扩大,同时把事件发生的经过细节尽可能收集齐全。 建立解决问题小组-质量若问题无法独立解决,通知你认为有关的人员组成团队。团队的成员必需有能力执行,例如调整机器或懂得改变制程条件,或能指挥作筛选等。 供应商名称/或工厂名 供应商代码 编制: 批准: 零件名称 职务: 职务: 零件号 零件重要度级别 日期: 日期: 1 问题详情 4. 临时对策 –立即的 6. 永久対策 发生地(或现场) 不良现象在何处发现。 已采取什么措施防止不合格品流出到DFL? 执行临时对策 若真正原因还未找到,临时用什么方法可以最快地防止问题发生?如全检、筛选、将自动改为手动、库存清 查等。临时对策决定后,立刻交由团队成员执行。 选择永久对策 找到造成问题的主要原因后,即可开始拟出对策的方法。对策的方法也许有好几种,例如修理或更新模具。试试对可能的选择列出其优缺 点,要花多少钱?多少人力?能持续多久? 再对可能的方法作一最佳的选择,并且确认这样的对策方法不会产生其它副作用。 问题分类 数量(分子/分母 ) 负责人 部门 实施时间 发生日 再发不良 Y N 考虑事项 处置 OK数 NG数 对策内容:永久改善的对策。 担当人/责任单位:永久对策实 施的单位和责任人。 对策时间:永久对策展开的时间,可以是某一天,也可能是某个时间段 。生产线导入时间:永久改善对策在生产线实现的时间。 在制品 考虑 * 防错,试验,过程控制 受影响的数量(或追溯) 中间在库品(半成品) 问题说明 仓库存品 描述问题 向团队说明何时、何地、发生了什么事、严重程度、目前状态、如何紧急处理、以及 展示照片和收集到的证物。想象你是办案人员,将证物、细节描述越清楚,团队解决 问题将越快。不良问题的简要描述(尽可能图片说明)。 服务备件 其他 首批交付合格部品如何特殊标识 /标记 ? 详细的临时对策 临时对策制定应涵盖: 针对流出不良原因采取的对策;针对顾客抱怨采取的应急对策;针对在制品、中间在库品(半成品)、仓库存 品、服务备件等采取的对策。 临时对策内容包括:对策时间、进展、担当人/责任单位。 首件VIN:永久对策在生产线实 现后装配的第一台车的VIN码( 目的是督促对策实施者进行现场 对策效果确认)。2. 向类似零件的展开 该问题在其他零件上发生过吗? 考慮事項 Y N 备注/ 結果 临时对策后的OK部品发交时间和数量及批次号 7. 对策确认 其他类似零件 同一不良现象覆盖的类似产品 对不良的防止流出对策、永久对策进行对策实施后的效果进行确 认。请附上相关数据,如:尺寸测定,工序能力,特性数据 Y N 一般零件 备注: 其他颜色零件 确认方法 左侧/右侧 5 最终分析 时间 执行及验证永久对策 当永久对策准备妥当,则可开始执行及停止暂时对策。并且对永久对策作一验证,例如观察不良率已由4000 PPM降为300 PPM,CPK由0.5升 为1.8等,下游工段及客户己能完全接受,不再产生问题。 前部/ 后部 真正的原因:经过技术等方面严密分析后得出的不良产生的根本原因 其他 考虑事项: 制造上/不良流出上/DFL未识别上的原因分析 人,机,料,法 5个为什么 何人,何处,何时,何原因,如何做 工序变换,返工,维护,文件规定。3. 供应商内部流出原因(或汽车厂家处未识别出)的初步分析 找出问题真正原因 找问题真正原因时,最好不要盲目地动手改变目前的生产状态,先动动脑。您第一件事是要先观察、分析、 比较。列出您所知道的所有生产条件,逐一观察,看看是否有些条件走样,还是最近有些什么异动?换了夹 具吗?换了作业员?换了供应商?换了运输商?修过电源供应器?流程改过? 或比较良品与不良品的检查结果, 看看那个数据有很大的差別,尺寸?重量?电压值?CPK?耐电压?等等不良的发生,总是有原因,资料分析常常 可以看出蛛丝马迹。这样的分析,可以帮助您缩小范围,越来越接近问题核心。当分析完成,列出您认为最 有可能的几项,再逐一动手作些调整改变,并且观察那一些改变可使品质回复正常及影响变异的程度,进而 找到问题真正的原因。这就是著名田口式方法最简单而实际的运用。通常可应用故障再现分析、FTA、因果 图、树图、关联图(原因之间有交叉影响、部分原因把两个以上的问题纠缠在一起)、正交试验设计法等统 计技术、方法。 8. 跟踪措施 不合格零件应当在何处被发现? 流程检讨:对导致不良产生的开发/制造/管理过程进行回顾,检讨业务流程中的不足。流程改善/固化:对流程中的不足采取改善对策并在 不足的环节固化(形成相应的业务基准和流程或管理项目)。 原因 责任部门 Y N 考慮事项 Yes/No 实施时间 实施部门 在制造工序中 工序作业/检查指导书 在制造后(如最终检验) 过程流程图 出货前/汽车厂家入库时 质量保证标准 没有被发现的原因 控制计划 / 控制图 对不良产生原因初步判断/流出原因的分析 F.M.E.A. / A.M.D.E.C. 图纸 量规 其他 (調査, 防错) 二级供应商跟踪 水平展开 (其他产品/类似工艺 ) 防止再发。 对类似的其它生产,虽然尚未发生问题,亦需作同步改善,防止再发,即我们说的“他石攻错”。同时 这样的失效,也应列入下一产品研发段的FMEA中予以验证。 对策内容展开方式:若存在同样不良发生的潜在风险,避免发生的对策和展开的方式。展开时间:水平 展开对策的实施时间。 结果确认人/时间:除供应商原因导致的不良外,其他同永久对策实施责任人。 措施查看更多