- 2021-05-11 发布 |
- 37.5 KB |
- 118页
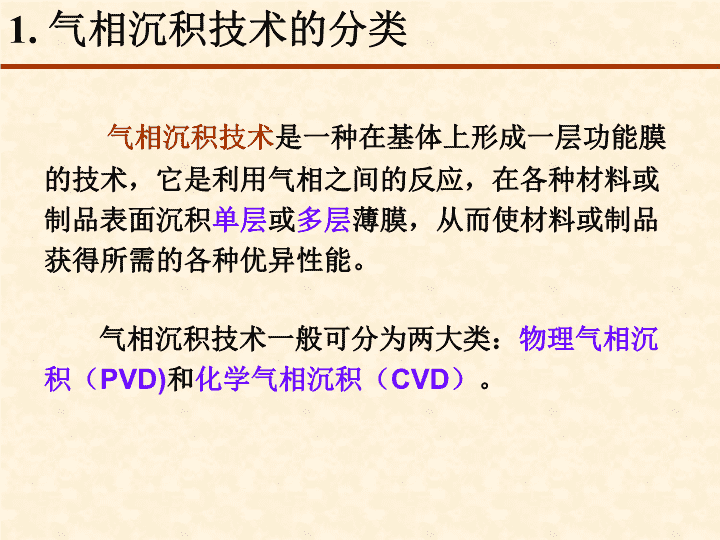
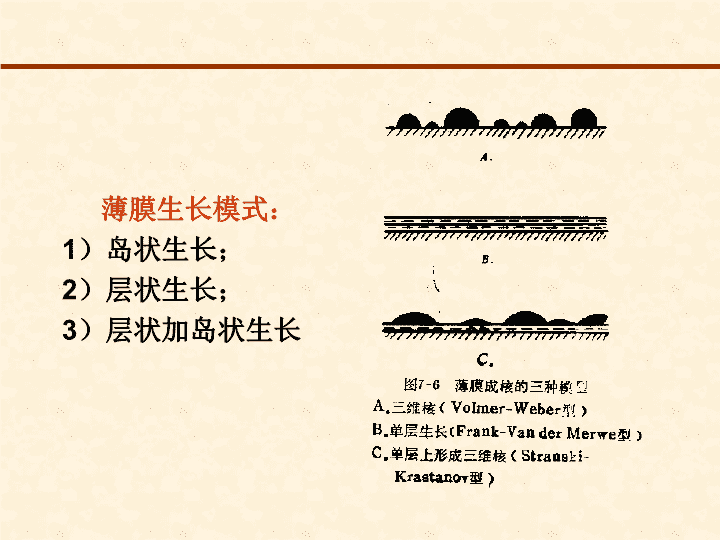

申明敬告: 本站不保证该用户上传的文档完整性,不预览、不比对内容而直接下载产生的反悔问题本站不予受理。
文档介绍
技能培训 材料表面工程学 气相沉积技术
1. 气相沉积技术的分类 气相沉积技术是一种在基体上形成一层功能膜 的技术,它是利用气相之间的反应,在各种材料或 制品表面沉积单层或多层薄膜,从而使材料或制品 获得所需的各种优异性能。 气相沉积技术一般可分为两大类:物理气相沉 积(PVD)和化学气相沉积(CVD)。 薄膜生长模式: 1)岛状生长; 2)层状生长; 3)层状加岛状生长 1.物理气相沉积(PVD): 在真空条件下,利用各种物理方法,将镀料气 化成原子、分子或使其离子化为离子,直接沉积到 基体表面上的方法。主要包括真空蒸镀、溅射镀膜、 离子镀膜等。 PVD法已广泛用于机械、航空、电子、轻工和 光学等工业部门中制备耐磨、耐蚀、耐热、导电、 磁性、光学、装饰、润滑、压电和超导等各种镀层。 随着PVD设备的不断完善、大型化和连续化,它的 应用范围和可镀工件尺寸不断扩大,已成为国内外 近20年来争相发展和采用的先进技术之一。 2.化学气相沉积(CVD) : 把含有构成薄膜元素的一种或几种化合物、单质 气体供给基体,借助气相作用或在基体表面上的化学 反应在基体上制得金属或化合物薄膜的方法。 主要包括常压化学气相沉积、低压化学气相沉积 和兼有CVD和PVD两者特点的等离子化学气相沉积等。 此外,还有有机金属化学气相沉积以及激光(电子束) 化学气相沉积。 2.化学气相沉积(CVD) : 目前,CVD法在电子、宇航、光学、能源等工业 中广泛用于制备化合物单晶,同质和异质外延单晶层, 制备耐磨、耐热、耐蚀和抗辐射的多晶保护层。此外, CVD是大规模集成电路制作的核心工艺,已广泛用于 制备半导体外延层、PN结、扩散源、介质隔离、扩 散掩蔽膜等。 7.2 真空技术基础 真空:“低于一个标准大气压里的气体状态”。 相对于大气状态,在真空状态下气体的新特点: 1:气体分子数目的减少,即气体单位体积中所 具有的分子数目的减少; 2:伴随着气体分子数目的减少,分子之间、分 子与器壁之间相互碰撞的次数逐渐减少; 3:气体分子热运动自由路程的增大。 7.2 真空技术基础第七章 气相沉积技术 一、真空度和真空区域的划分 真空高低的程度是用真空度这个物理量来 衡量的。所谓真空度,即是指低压空间中气态 物质的稀薄程度。气体的压力越低,其稀薄程 度越大,真空度越高。 7.2 真空技术基础第七章 气相沉积技术一、真空度和真空区域的划分 压强的单位主要采用Pa和 Torr,还有标准大气压、bar、 kgf/cm2。 几种常见单位之间的换算关系如下: 1 Torr = 133.3 Pa 1 Pa = 7.5×10-3 Torr 1 Torr = 1 mmHg 柱 1 Torr = 1/760 大气压 7.2 真空技术基础第七章 气相沉积技术 一、真空度和真空区域的划分 通常将真空区域划分为:低真空、 中真空、高真空和超高真空。 各真空区域所对应的真空值分别为: 低 真 空:105 ~102 Pa 中 真 空:102 ~10-1 Pa 高 真 空:10-1~10-5 Pa 超高真空: ≤10-5 Pa 7.2 真空技术基础第七章 气相沉积技术 二、真空的特点和应用 1.表面保护作用 在真空下,金属的氧化反应很少进行或完全不 能进行。因此,能够防止钢件表面的氧化和脱碳, 具有表面保护作用。 2.表面净化作用 在真空状态下,氧化物的分解所产生气体的压 力(称为分解压力)大于真空炉内氧的压力,反应 只能向氧化物分解的方向进行,因此当钢件表面有 氧化物时,就可使其中的氧排除掉,使表面得到净 化; 7.2 真空技术基础第七章 气相沉积技术 二、真空的特点和应用 2.表面净化作用 真空热处理时,钢件表面油污中的碳、氧、氢 的化合物易分解为氢、水蒸气和二氧化碳气体,随 后被抽走; 在真空下长时间加热时,零件在前几道工序 (熔炼、铸造、热处理等)中所吸收的氢、氧等气 体会慢慢地释放出来,从而降低钢件的脆性。 7.2 真空技术基础第七章 气相沉积技术 二、真空的特点和应用 3.减少气体分子之间的碰撞次数。 4.真空的绝热性好。 5.可降低物质的沸点或气化点。 7.2 真空技术基础第七章 气相沉积技术 四、真空的获得 通过真空泵实现。 真空泵从高/超真空到粗/低真空, 其产品大致可分14大类: 高/超真空——低温泵、分子泵、溅射离子泵、 钛升华泵、扩散泵。 中真空——干泵、双级旋片泵、罗茨泵、油增压 泵、水蒸气喷射泵。 粗/低真空——单级旋片泵、滑阀泵、液环泵、 往复式真空泵。 7.2 真空技术基础第七章 气相沉积技术 7.2 真空技术基础第七章 气相沉积技术 7.2 真空技术基础第七章 气相沉积技术 7.2 真空技术基础第七章 气相沉积技术 5.1.1 真空蒸发镀膜 真空蒸镀定义:真空蒸发是制备薄膜的一种常 用工艺,在工业上应用较多。具体过程是:通常在 真空度为10-4-10-5Torr的真空室内进行,采用电 阻式加热、 电子束加热、电弧加热及激光加热等加 热方法,使金属或者合金等材料蒸发和升华,由固 态变为气态(原子、分子或原子团);蒸发的气态 粒子通过基本上没有碰撞的直线方式从蒸发源传输 到基片上,并在基片上沉积成膜。导电材料、介质 材料、磁性材料和半导体材料等,都可以通过真空 蒸发工艺制备。 二、真空蒸镀方式和设备 (一)蒸发方式及蒸发源 真空蒸镀可采用的不同的加热方法,主要有:电 阻加热法、电子束加热、高频感应加热法、激光加热 法。 蒸发源:加热待蒸发材料并使之挥发的器具称 为蒸发源,也称加热器。 1.电阻加热法 用丝状或片状的高熔点金属做成适当形状的蒸发 源,将膜料放入其中,接通电源,电阻加热膜料使之 蒸发。 对蒸发源材料的基本要求是:高熔点,低蒸气压, 在蒸发温度下不会与膜料发生化学反应或互溶,具有 一定的机械强度,且高温冷却后脆性小等性质。常用 钨、钼、钽、石墨、氮化硼等高熔点材料。按照蒸发 材料的不同,可制成多股线螺旋形、U形、圆锥筐形、 薄板形、舟形等。 电 阻 加 热 蒸 发 源 2.电子束加热 用电子枪发射出的高能电子束直接轰击蒸发物 质的表面,使其蒸发。包括:发射电子的热阴极、电 子加速极、阳极(镀膜材料)。 由于是直接在蒸发物质中加热,避免了蒸发物 质与容器的反应和蒸发源材料的蒸发,故可制备高纯 度的膜层。一般用于电子元件和半导体用的铝和铝合 金,此外,用电子束加热也可以使高熔点金属(如W, Mo,Ta等)熔化、蒸发。 2.电子束加热 2.电子束加热 2.电子束加热 3.高频感应加热法 在高频感应线圈中放入氧化铝和石墨坩埚,蒸 镀的材料置于坩锅中,通过高频交流电使材料感应加 热而蒸发。 此法主要用于铝的大量蒸发,得到的膜层纯净 而且不受带电粒子的损害。 4.激光加热法 采用激光照射在膜料表面,使其加热蒸发。 由于不同材料吸收激光的波段范围不同,因而 需要选用相应的激光器。例如用二氧化碳连续激光加 热SiO、ZnS、MgF2、TiO2、Al2O3、Si3N4等膜料; 用红宝石脉冲激光加热Ge、GaAs等膜料。 由于激光功率很高,所以可蒸发任何能吸收激 光光能的高熔点材料,蒸发速率极高,制得的膜成分 几乎与膜料成分一样。 激 光 陶 瓷 蒸 镀 示 意 图 四、合金蒸镀 根据蒸发镀的原理可知:通过采用单金属镀料 或合金镀料我们就可在基体上得到单金属膜层或得 到合金膜层。但由于在同一温度下,不同的金属具 有不同的饱和蒸气压,其蒸发速度也不一样,蒸发 速度快的金属将比蒸发速度慢的金属先蒸发完,这 样所得的膜层成分就会与合金镀料的成分有明显的 不同。 四、合金蒸镀 为解决这个问题,可采用以下方法: ①多源同时蒸镀法:采用多蒸发源,使各种金 属分别蒸发,气相混合,同时沉积。利用该法还可 以得到用冶炼方法所得不到的合金材料薄膜。 ②瞬源同时蒸镀法(闪蒸法):采用单蒸发源, 使加热器间断的供给少量热量,产生瞬间蒸发。 真空蒸镀设备: 用于进行真空蒸镀的装置,一般由四部分组成: (1)真空室:用于放置镀件,进行镀膜的场所; (2)真空(排气)系统:一般由机械泵、扩散泵、 管道、阀门等组成; (3)蒸发系统:包括蒸发源,加热蒸发源的电气设 备; (4)电气设备:用于测量真空系统,膜厚测量系统, 控制台等。 蒸镀用途 蒸镀只用于镀制对结合强度要求不高的某些功 能膜,例如用作电极的导电膜,光学镜头的增透膜 等。 蒸镀用于镀制合金膜时,在保证合金成分这点 上,要比溅射困难得多,但在镀制纯金属时,蒸镀 可以表现出镀膜速度快的优势。 蒸镀用途 蒸镀纯金属膜中,90%是铝膜。铝膜有广泛的用 途。目前在制镜工业中已经广泛采用蒸镀,以铝代 银,节约贵重金属。集成电路是镀铝进行金属化, 然后再刻蚀出导线。在聚酯薄膜上镀铝具有多种用 途:制造小体积的电容器;制做防止紫外线照射的 食品软包装袋;经阳极氧化和着色后即得色彩鲜艳 的装饰膜。双面蒸镀铝的薄钢板可代替镀锡的马口 铁制造罐头盒。 5.1.2 溅射镀膜 1 溅射现象 用几十电子伏或更高动能的荷能粒子轰击材料表 面,使其原子获得足够的能量而溅出进入气相的过程 称为溅射。 溅射镀膜:在真空室中,利用荷能粒子轰击材料表 面,使其原子获得足够的能量而溅出进入气相,然后 在工件表面沉积的过程。 一、溅射镀膜原理 一、溅射镀膜原理 1 溅射现象 用几十电子伏或更高动能的荷能粒子轰击材料表 面,使其原子获得足够的能量而溅出进入气相的过程 称为溅射。 溅射镀膜:在真空室中,利用荷能粒子轰击材料表 面,使其原子获得足够的能量而溅出进入气相,然后 在工件表面沉积的过程。 一、溅射镀膜原理 1 溅射现象 一、溅射镀膜原理 入射粒子非弹性碰撞效应 反冲注入 注入 溅射粒子: M0、M+、M-、Mn 光子 基材M 通道注入 二次电子 X-射线 反射粒子 I0、I+、I-、 In 弹性碰撞效应 1 溅射现象 在溅射镀膜中,被轰击的材料称为靶。 由于离子易于在电磁场中加速或偏转,所以荷能 粒子一般为离子,称为离子溅射。用离子束轰击靶而 发生的溅射,则称为离子束溅射。 一、溅射镀膜原理 溅射产额 一个入射离子溅射出的原子或分子个数称为溅 射产额或溅射率,单位为原子个数/离子。显然,溅 射率越大,生成膜的速度就越大。 一、溅射镀膜原理 每入射一个粒子 溅射出来的原子数Y 影响溅射产额的因素主要有: ①入射离子:包括入射离子的能量、入射角、入 射离子种类等; ②与靶有关:包括靶原子的原子序数、靶表面原 子的结合状态、结晶取向以及靶材是纯金属、合金 或化合物等; ③与温度有关:一般认为溅射率在和升华能密切 相关的某一温度内,溅射率几乎不随温度变化而变 化,当温度超过这一范围时,溅射率有迅速增加的 趋向。 最大值 阈值 入射离子的能量 入射离子能量对溅射产额的影响 入射离子能量对溅射产额的影响 只有当入射离子能量超 过一定的溅射阀值以后、 才会出现被溅射物表面 溅射。对大多数金属, 溅射阀值范围在20-40ev。 随着入射离子能量的增 加、溅射产额先是提高 而后下降并发生注入. 是入射方向与样 品法向的夹角。 当 = 60o- 70o时, 溅射产额最大, 但对不同的材料, 增大情况不同。 离子入射度对溅射产额的影响 入射离子原子系数对溅射产额的影响 图为Ar+在400eV时对一些元素的溅射产额 靶原子系数对溅射产额的影响 元素周期表 溅射产额与元素的升华热倒数的对比 升华能对溅射产额的影响 在100-1000 eV下,用Hg+垂直入射Mo和Fe的溅 射粒子的角分布 溅射粒子能量分布曲线 溅射原子的动能一般为1~10ev,高于热蒸发原子(约 0.1-1ev动能)。 2 辉光放电 辉光放电是溅射的基础,溅射镀膜主要是利用 辉光放电将气体电离产生正离子撞击靶材表面,靶 材的原子被溅射出而堆积在基底表面形成薄膜。 辉光放电属于低气压放电,其构造是在封闭的 容器內放置两个平行的电极板,利用电子将中性原 子和分子激发,当粒子由激发态降回至基态时会以 光的形式释放出能量。 2 辉光放电 2 辉光放电 气体放电伏安特性 八个区域: 1)阿斯顿暗区 2)阴极辉光区 3)阴极暗区 4)负辉区 5)法拉第暗区 6)正柱区 7)阳极暗区 8)阳极辉光区 1)、2)、3)合起来为阴极位降区, 是维持放 电必不可少的区域。 八个区域: 1)阿斯顿暗区:由于电子从阴极逸出时的速度很小, 不足以使气体激发,所以不发光。 2)阴极辉光区:电子获得了足够的能量而使气体原 于受激发光。 3)阴极暗区: 4)负辉区:已加速的电子与气体原子、正离子发生 碰撞、电离、复合的区域。 八个区域: 5)法拉第暗区: 这是由负辉区扩展而来的过渡区。 在负辉区中损失了能量的电子,难以引起原子激 发,故不发光。 6)正柱区:电子和离子的浓度很大,而在任一点附 近两者浓度均相等,宏观上呈现为电中性,所以 又称为等离子区.该区导电能力很强,象导体一 样在放电中起着传导电流的作用。在辉光放电中, 正拄区是可长可短、可有可无的区域。 7)阳极暗区 8)阳极辉光区 阴极位降区, 是维持放电必不可少的区域。极间 电压主要降落在该区。若其他条件不变,只改变 两极间距离,阴极位降区宽度不会改变,而其他 各区则相应缩短。阴极与阳极间距离至少应比阴 极位降区宽。 二、溅射镀膜的特点和方式 (一) 溅射镀膜的特点(与真空蒸镀相比) 1)溅射出的原子能量高,形成的薄膜结合好; 2)可用于任何材料的镀膜; 3)膜层厚度均匀; 4)除磁控溅射外,沉积速率低. (二)溅射镀膜的方式 具体的溅射工艺很多,如二极(直流)溅射、射频 溅射、磁控溅射、反应溅射、对向靶溅射、离子束溅 射、吸气溅射等等。下面简单介绍几种。 1.二极溅射 在真空室内 (10-3-10-4Pa)充 以1-10Pa的惰性 气体(例如氩气), 被溅射的材料作为 阴极,将基片作为 阳极并接地。阴阳 极电压为几千伏。 1.二极溅射 最简单的直流二极溅射装置如图所示。 在真空 室内(10-3-10-4Pa)充以1-10Pa的惰性气体(例如氩 气),被溅射的材料作为阴极,将基片作为阳极并接地。 整个系统在阴阳极之间加上几千伏的直流电后产生辉 光放电,由放电形成的正离子在电场作用下朝着阴极 靶方向加速,并轰击阴极。在离子的轰击下,材料从 阴极上打出来(主要是以中性原子的形式,部分是以离 子的形式),被溅射出来的粒子冷凝在放置于阳极的基 片上就形成薄膜。 1.二极溅射 直流二极溅射法可以镀金属、合金以及一些低导 电性的材料,但是不能直接镀绝缘材料。另外,直流 二极溅射法方法简单,但是有不少缺点。直流二极溅 射的工作气压较高(1Pa左右),因而在真空室中残留的 气氛(O2,H2O,N2,CO2等等)对于膜层的质量影响 就较大。二极直流溅射法的溅射速率也较低。 溅射镀膜的速率取决于溅射电压和电流,并与靶 与基片间距离以及真空室的气体压强有关。 2.三极溅射 三级溅射是在二极溅射的基础上增加一个能加 热到2500C的钨丝做成的热电子发射极来产生热电子。 这些电子在工作电场中被加速,产生电离作用。在三 极溅射中,靶电流可以在电压和气压都不变的条件下, 独立地调整。三极溅射可以在较低的靶电压和气压下 工作,数百伏的靶电压和0. 01-0. 1Pa的气压下就能维 持辉光放电效应。 3.磁控溅射 磁控溅射特点是在阴极靶面上建立一个环状 磁靶(电场与磁场正交),溅射产生的二次电子在阴 极位降区被加速后,不是直接飞向阳极,而是在正交 电磁场作用下来回振荡,沿着环状磁场作摆线运动。 并不断与气体分子碰撞,把能量传递给气体分子,使 之电离,而电子则失去能量,变为低能电子,最终漂 移到阴极附近的辅助阳极被吸收。 由于二次电子在靠近靶的封闭等离子体中作循 环运动,路程足够长,每个电子使气体原子电离的机 会增加,因此气体离化率大大增加。因此,磁控溅射 薄膜生长速率比其他溅射高。 3.磁控溅射 目前,磁控溅射是应用最广泛的一种溅射沉积方 法,其主要原因是在磁场中电子的电离效率提高,这 种方法的沉积速率可以比其他溅射方法高出一个数量 级。 此外,由于磁场有效地提高了电子与气体分子 的碰撞几率、因而工作气压可以显著降低,即可由 1Pa降低至10-1 Pa。这一方面降低了薄膜污染的倾向, 另一方面也将提高入射到衬底表面原子的能量,因而 将可以在很大程度上改善薄膜的质量。 3.磁控溅射设备 4.射频溅射 为了镀绝缘材料需要采用射频溅射法。射频 电源是采用高频振荡器产生的。常用的射频电源 频率为13. 56MHz。由于有射频电场存在,电子 能在阴阳极间来回振荡,电子和气体粒子的碰撞 几率大大增加。因此,在射频溅射中,并不需要 从阴极发射大量的电子来维持放电过程。因此, 工件可以不接电。射频溅射放电能在较高的真空 度(即较低的气压)下进行。例如,二极直流溅射 常在1Pa左右的气压下进行,而射频溅射却可在 0.1Pa的气压下进行。 4.射频溅射 4.射频溅射 利用射频溅射可以溅射绝缘材料,这是由 于在电子的质量小,放电时电子的迁移率高于离 子,当靶电极通过电容耦合加上射频电压时,到 达靶上的电子数目远大于离子数,于是电子就积 存在由绝缘体制成的靶面上,等于自动地加上了 负偏压。正离子在靶面上负电位的强烈吸引下, 运动到靶面对靶产生溅射作用。这样在基底上就 形成了绝缘体的薄膜。 5.偏压溅射 偏压溅射的原理是在基片上加上负偏压(约 -100V),使来自放电空间的离子连续地清洗基片,获 得纯洁的膜。 5.偏压溅射 6.非对称交流溅射 非对称的交流溅射法采用非对称的交变电压, 电阻R的作用是产生不对称的交流电,以振幅大 的半周溅射靶材,并使薄膜沉积在基底上;以振 幅小的半周通过离子轰击基底,除去吸附气体而 得到高纯膜。 6.非对称交流溅射 7.反应溅射 在阴极溅射中,真空槽中需要充入气体作为媒 介,使辉光放电得以启动和维持。最常用的气体是氩 气。如果在通入的气体中掺入易与靶材发生反应的气 体(如O2,N2等),因而能沉积制得靶材的化合物 膜(如靶材氧化物,氮化物等化合物薄膜)。如采用 Ti靶进行溅射时,在工作气体中加入一定量反应气N2、 CH4和O2就可分别得到TiN、TiC、TiO2化合物薄膜, 而且控制反应气分压可以控制化合物的成分、晶体结 构和生长方式。 5.1.3 离子镀 一、离子镀的概念 离子镀是结合蒸发与溅射两种薄膜沉积技术而发 展的一种物理气相沉积方法。 这种方法使用蒸发方法提供沉积用的物质源,同 时在沉积前和沉积中采用高能量的离子束对薄膜进行 溅射处理。 离子镀(ionplating,IP)是在真空蒸发镀的基 础上发展起来的新技术,它将各种气体放电方式引入 气相沉积领域,使得整个气相沉积过程都在等离子体 中进行。 二、几种常用的离子镀 1 气体放电等离子体离子镀 (直流离子镀) 设备与真空蒸镀设备类似, 在蒸发源与基材之间加直流 电压,基材为负极,蒸发源 为正极(接地)。充以氩气, 调整电压使蒸发源与基材之 间产生辉光放电,氩气离子 和镀料离子加速飞向基材, 在离子轰击的同时形成质量 较高的膜。 2 射频离子镀 三区: 1)蒸发区; 2)离化区(射频线圈 为中心); 3)离子加速区 射频频率:13.56MHz 真空度:10-1-10-3Pa 基体偏压:0-1500V 3.空心阴极放电离子镀 利用空心热阴极放电 产生等离子体。空心钽管 作为阴极(HCD枪),辅 助阳极距阴极较近,二者 作为引燃弧光放电的两极。 阳极是镀料。弧光放电时, 电子轰击阳极镀料,使其 熔化而实现蒸镀。蒸镀时 基片加上负偏压即可从等 离子体中吸引氩离子向基 片轰击,实现离子镀。 4 多弧离子镀(阴极电弧离子镀) 基本原理是:在真空室中利用电弧靶(弧光放 电的大能量)将镀料(钛等金属或合金)熔化并蒸 发离化生成等离子体,通过电场进行加速,最后沉 积在工件表面。 多弧离子镀属于冷场致弧光放电范畴,是一种 没有固定熔池的固态蒸发源,多采用圆形阴极电弧 源作为蒸发源。 4 多弧离子镀 多个弧源的 多弧离子镀: 可制多层膜, 合金膜,化 合物膜. 4 多弧离子镀 多弧离子镀的特点: (1) 蒸发源多,蒸发源可以任意方式放置,膜厚分 布均匀。 (2)电弧镀膜具有离化率高,高达60%~80%; 可镀多种膜层,膜层质量好,镀膜效率高。 (3) 等离子体密度高,表面可被离子轰击洁净, 而且可增大偏压,所以结合力好。 三、离子镀的特点: 离子镀兼具蒸镀的沉积速率高和溅射镀膜的沉积 粒子能量高(比溅射粒子能量高得多)的优点,从 而具有膜/基结合力强、绕涂性好和可镀材料广的 特点。 三、离子镀的特点: (1)附着力强,薄膜结构致密。在蒸发沉积之前 以及沉积同时采用离子轰击衬底和薄膜薄膜的方法, 一方面可以在薄膜与衬底之间形成粗糙洁净的表面, 提高薄膜的附着力;另一方面可抑制柱状晶的生长, 从而形成均匀致密的薄膜结构。 (2)绕射性好,可提高薄膜对于复杂外形表面的 覆盖能力。与纯粹的蒸发沉积相比,在离子镀的过 程中,蒸发材料的原子被电离为正离子,可以在带 负电的工件表面各个部位沉积(包括背面)。 (3)沉积速度快。和蒸发镀膜一样,沉积速度快。 四、物理气相沉积的三种基本方法的比较 真空蒸镀 溅射镀 离子镀 附着力: 弱 强 强 绕射性: 差 好 好 薄膜致密度: 小 大 大 沉积速度 快 慢(磁控溅射除外) 快 PVD技术的应用: 可获得金属涂层和化合物涂层。 如在黄铜表面涂敷金膜,用于装饰; 在塑料带上涂敷铁钴镍膜,制作磁带; 在高速钢表面涂敷TiN、TiC薄膜, 提高刃具的耐 磨性等。 多层膜(TiN/CrN20层) 塑料基体上制备AI膜与着色 磁控溅射镀膜在工具钢基体上制备TiN膜 多弧离子镀膜机 5.2 化学气相沉积 5.2 化学气相沉积 一、化学气相沉积原理 利用气态化合物或化合物的混合物在基体 材料表面(通常为热表面)上发生气相化学反应, 从而在基材表面上形成镀膜的技术称为化学气相 沉积(CVD)。 CVD法制备薄膜的过程,可以分为下面几个 主要的阶段: ①反应气体扩散至工件表面; ②反应气体分子被基材表面吸附; ③在基材表面发生化学反应; ④反应生成的气相副产物由基片表面脱离,被真 空泵抽掉; ⑤在基片表面留下的固体反应产物在基片表面扩 散、形核,形成薄膜。 CVD设备示意图 CVD设备: 1.送气装置; 2.反应室; 3.加热装置; 4.排气装置 CVD技术中常采用的化学反应有: (1)热分解反应: 热分解法是在真空或惰性气氛下加热基片至所需 的温度之后,导人反应气体使之发生热分解反应,最 后在基片上沉积出固体的薄膜材料。采用热解法可以 制备金属、半导体、绝缘材料等各种材料。 (1)热分解反应: 热分解法制备硅单晶的示意图:基底为硅片,反应气 体为硅烷SiH4。 在800-1000C发生热分解反应 SiH4 ---> Si + 2H2 (2)还原反应(氢还原、金属还原,基材还原) 用氢气来还原卤化物产生各种金属和半导体薄膜。 如用H2还原四氯化硅制备单晶硅的反应: SiCl4 + 2H2 ---> Si + 4HCl (3)化学输送(歧化反应):2SiI2 ---> Si + SiI4 (4)氧化反应:SiH4 + O2 ---> SiO2 + 2H2 (5)水解反应: 2AlCl3+3H2O--->Al2O3 +6HCl (6)氮化反应或氨解反应: 3SiH4 + 4NH3 ---> Si3N4 + 12H2 TiCl4+N2+ H2 → TiN+HCl (7)碳化反应:TiCl4 + CH4 ---> TiC + 4HCl (8)化学合成反应 两种或两种以上的气态反应物在一个热的基 底上相互反应,产生固相的反应产物沉积在基底 上,这种薄膜的沉积方法称为化学合成法。 如: SiCl4 +CCl4 ---> SiC+2Cl2 (9)等离子体激发反应:用等离子体放电使反应气 体活化,可以在较低温度下成膜。 (10)光激发反应:例如在SiH-O2反应系中使用水 银蒸气为感光物质,用253.7纳米紫外线照射,并被 水银蒸气吸收,在这一激发反应中可在100℃左右制 备硅氧化物。 (11)激光激发反应:例如金属有机化合物在激光激 发下W(CO)6 ---> W + 6CO 。 二、化学气相沉积技术的分类 按化学反应的激活方式,可分为: 1) 热化学气相沉积技术(TCVD) 2) 等离子体化学气相沉积技术(PACVD) 3) 激光诱导化学气相沉积技术(LCVD) 二、化学气相沉积技术的分类 按化学反应室的压力,可分为: 1)常压CVD; 2)低压CVD 二、化学气相沉积技术的分类 按化学反应温度高低,可分为: 1)低温沉积(<200℃,如等离子气相沉积 PCVD); 2)中温CVD( 500~800℃,金属有机化合物 气相沉积MOCVD ); 3)高温CVD(900~1200℃,如 热化学气相 沉 积TCVD ); 4)超高温CVD(>1200℃)。 1 混气室 2转子流量计 3步进电机控制仪 4真空压力表 5不锈钢管喷杆6喷头 7基板 8石墨基座 9 石英管反应室 10机械泵 11WZK温控仪 12电阻丝加 热源 13保温层陶瓷管 14密封铜套 1.热化学气相沉积技术(TCVD) 电阻丝加热,石英管反应室 1.热化学气相沉积技术(TCVD) 电阻丝加热, 石英钟罩 热化学气相沉积技术的特 点: 沉积温度高:800-1200C 1.热化学气相沉积技术(TCVD) 2. 等离子体增强化学气相沉积(PCVD) 利用直流放电、射频放电或微波产生的等离子体 内的高能电子激活反应气体分子使之离解或电离,生 成活泼的激发分子、离子、原子或活性原子团等,并 在基体表面上沉积镀膜。 PCVD法借助于等离子体作用,促进气相化学反 应进行,可降低基体温度,提高反应速度。 2. 等离子体增强化学气相沉积(PCVD) 射 频 等 离 子 CV D 射频电源通 常采用电容耦 合或电感耦合 方式,其中又 可分为电极式 和无电极式结 构,电极式一 般采用平板式 或热管式结构 2. 等离子体增强化学气相沉积(PCVD) 微 波 等 离 子 CVD 3. 激光诱导化学气相沉积(LCVD) 利用激光激活反应气体分子使之离解或电离,生成 活泼的激发分子、离子、原子或活性原子团等,并在 基体表面上沉积镀膜。 特点:沉积温度低。 3. 金属有机化合物化学气相沉积(MOCVD) 三、CVD技术在工模具上的应用: CVD镀层已成功地应用在刀具、模具取得明显的效 果。 用CVD法在不锈钢表壳上获得金黄色TiN涂层, 不 但美观, 而且耐磨。在刀具及模具表面沉积TiN、TiC、 Ti(C,N)、Cr7C3、Al2O3, 以提高工模具的耐磨性。 CVD金刚石薄膜查看更多