- 2021-05-11 发布 |
- 37.5 KB |
- 95页
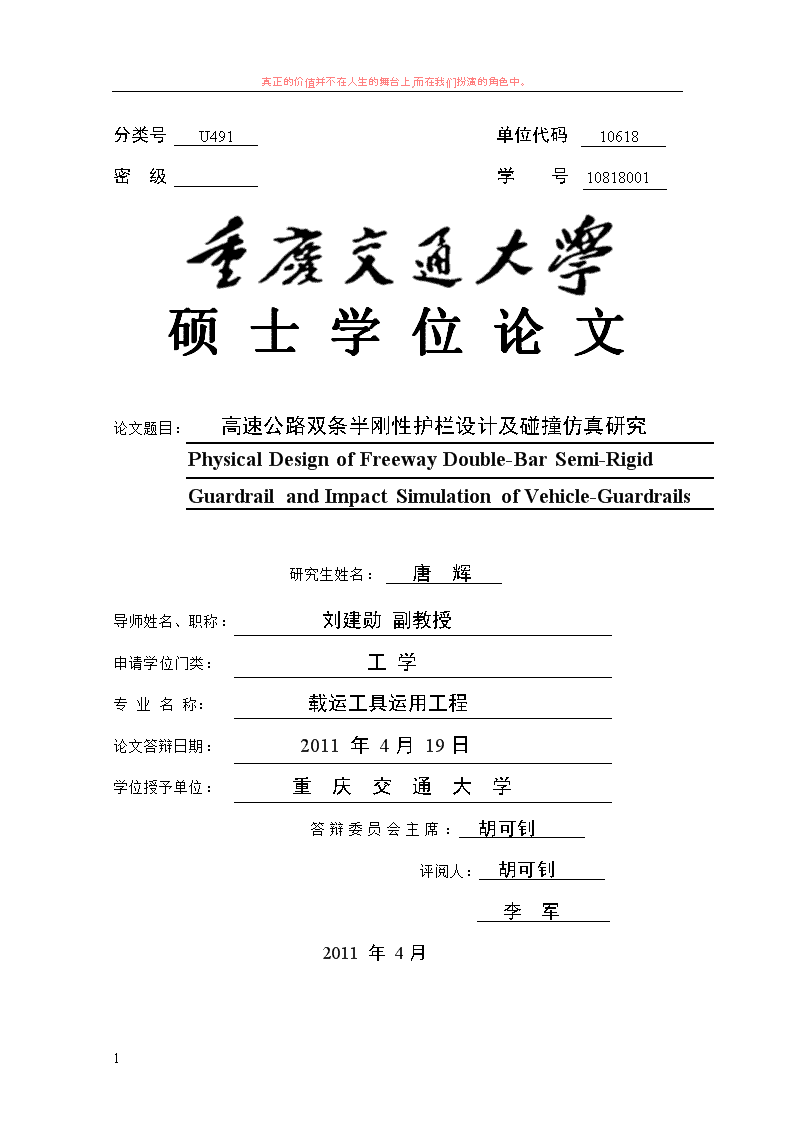
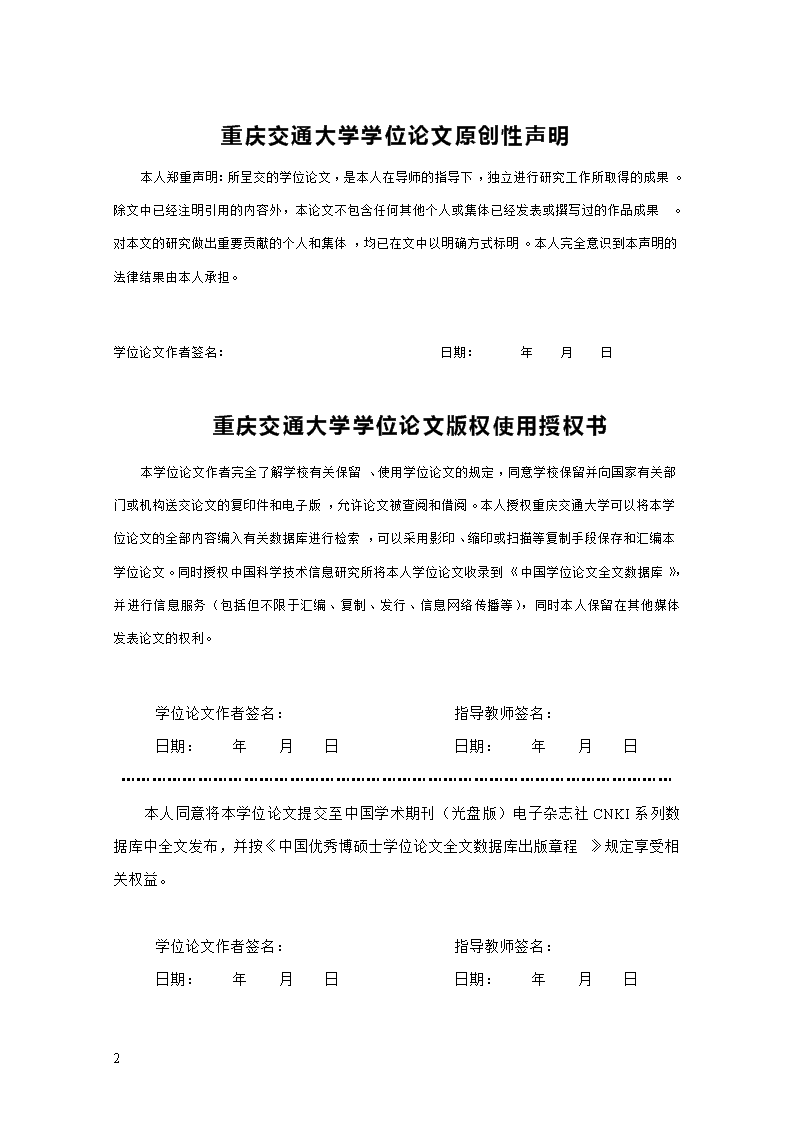
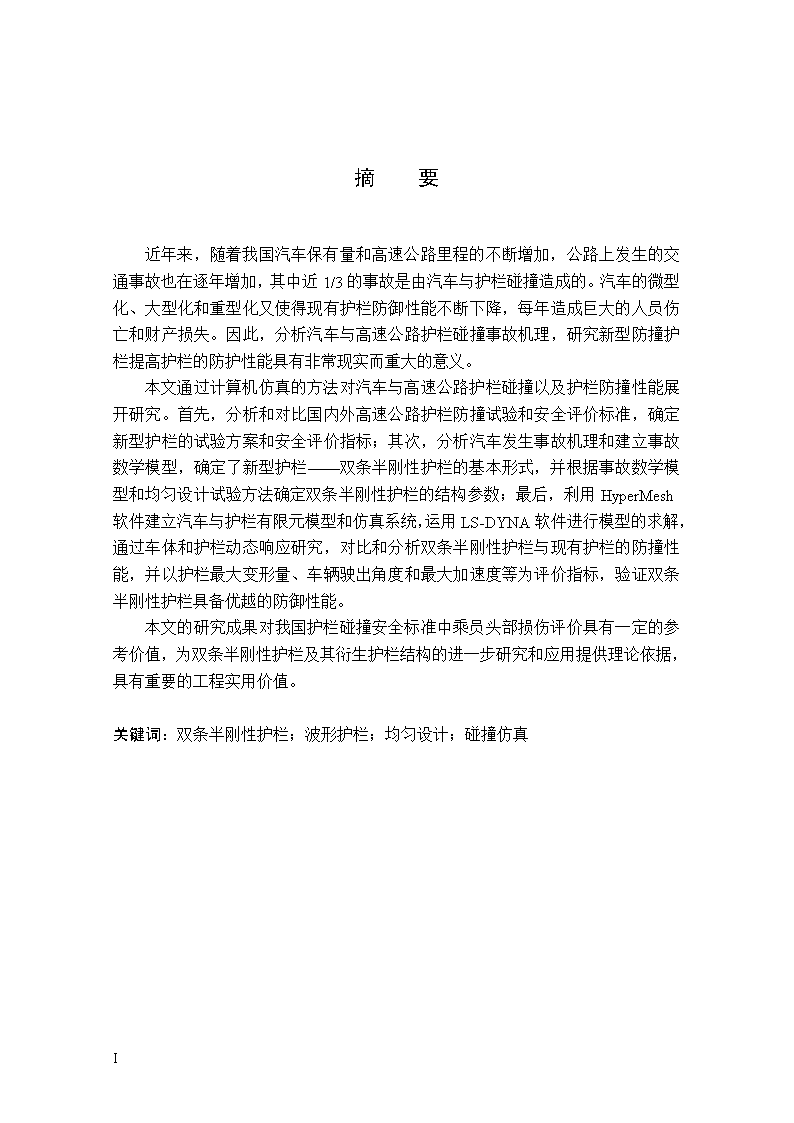
申明敬告: 本站不保证该用户上传的文档完整性,不预览、不比对内容而直接下载产生的反悔问题本站不予受理。
文档介绍
高速公路双条刚性护栏设计及碰撞仿真研究
真正的价值并不在人生的舞台上,而在我们扮演的角色中。 1 分类号 U491 单位代码 10618 密 级 学 号 10818001 硕 士 学 位 论 文 论文题目: 高速公路双条半刚性护栏设计及碰撞仿真研究 Physical Design of Freeway Double-Bar Semi-Rigid Guardrail and Impact Simulation of Vehicle-Guardrails 研究生姓名: 唐 辉 导师姓名、职称: 刘建勋 副教授 申请学位门类: 工 学 专 业 名 称: 载运工具运用工程 论文答辩日期: 2011 年 4 月 19 日 学位授予单位: 重 庆 交 通 大 学 答 辩 委 员 会 主 席 : 胡可钊 评阅人: 胡可钊 李 军 2011 年 4 月 2 重庆交通大学学位论文原创性声明 本人郑重声明:所呈交的学位论文,是本人在导师的指导下,独立进行研究工作所取得的成果。 除文中已经注明引用的内容外,本论文不包含任何其他个人或集体已经发表或撰写过的作品成果。 对本文的研究做出重要贡献的个人和集体,均已在文中以明确方式标明。本人完全意识到本声明的 法律结果由本人承担。 学位论文作者签名: 日期: 年 月 日 重庆交通大学学位论文版权使用授权书 本学位论文作者完全了解学校有关保留、使用学位论文的规定,同意学校保留并向国家有关部 门或机构送交论文的复印件和电子版,允许论文被查阅和借阅。本人授权重庆交通大学可以将本学 位论文的全部内容编入有关数据库进行检索,可以采用影印、缩印或扫描等复制手段保存和汇编本 学位论文。同时授权中国科学技术信息研究所将本人学位论文收录到《中国学位论文全文数据库》, 并进行信息服务(包括但不限于汇编、复制、发行、信息网络传播等),同时本人保留在其他媒体 发表论文的权利。 学位论文作者签名: 指导教师签名: 日期: 年 月 日 日期: 年 月 日 ……………………………………………………………………………………………… 本人同意将本学位论文提交至中国学术期刊(光盘版)电子杂志社 CNKI 系列数 据库中全文发布,并按《中国优秀博硕士学位论文全文数据库出版章程》规定享受相 关权益。 学位论文作者签名: 指导教师签名: 日期: 年 月 日 日期: 年 月 日 II 摘 要 近年来,随着我国汽车保有量和高速公路里程的不断增加,公路上发生的交 通事故也在逐年增加,其中近 1/3 的事故是由汽车与护栏碰撞造成的。汽车的微型 化、大型化和重型化又使得现有护栏防御性能不断下降,每年造成巨大的人员伤 亡和财产损失。因此,分析汽车与高速公路护栏碰撞事故机理,研究新型防撞护 栏提高护栏的防护性能具有非常现实而重大的意义。 本文通过计算机仿真的方法对汽车与高速公路护栏碰撞以及护栏防撞性能展 开研究。首先,分析和对比国内外高速公路护栏防撞试验和安全评价标准,确定 新型护栏的试验方案和安全评价指标;其次,分析汽车发生事故机理和建立事故 数学模型,确定了新型护栏——双条半刚性护栏的基本形式,并根据事故数学模 型和均匀设计试验方法确定双条半刚性护栏的结构参数;最后,利用 HyperMesh 软件建立汽车与护栏有限元模型和仿真系统,运用 LS-DYNA 软件进行模型的求 解,通过车体和护栏动态响应研究,对比和分析双条半刚性护栏与现有护栏的防 撞性能,并以护栏最大变形量、车辆驶出角度和最大加速度等为评价指标,验证 双条半刚性护栏具备优越的防御性能。 本文的研究成果对我国护栏碰撞安全标准中乘员头部损伤评价具有一定的参 考价值,为双条半刚性护栏及其衍生护栏结构的进一步研究和应用提供理论依据, 具有重要的工程实用价值。 关键词:双条半刚性护栏;波形护栏;均匀设计;碰撞仿真 III ABSTRACT As the vehicle capacity and the freeway mileage increase, the number of traffic accidents is also growing in recent years, and one third of the accidents are caused by vehicles crash the guardrail. Crashworthiness performance of the present guardrail is declining since the vehicle becomes miniaturization, large-scale or heavy. It causes huge casualties and heavy property damages every year. Therefore, it has a great significance to do researches on crash mechanism between vehicle and the guardrail, design new guardrail to improve the crashworthiness. In the paper, crash between vehicle and the guardrail, performance of the guardrail crashworthiness are studied through computer simulation method. First, guardrail crashworthiness tests and security evaluation criteriaion at home and abroad are analysed and compared, test scheme and evaluating indicators of a new guardrail is established. Then, crash mechanalism is analysed and the crash simulation model is created. According to the crash simulation model and test method of uniform design, a new guardrail which called double-bar semi-rigid guardrail and its structural parameters is identified. Finally, finite element models and vehicle-guardrail system is created through HyperMesh, and calculated by LS-DYNA. After studying the dynamic response of vehicle and the guardrail, crashworthiness of the two guardrails are analysed and compared, max displacement of the guardrail, vehicle max acceleration, driving out angle and such kinds of evaluating indicators verify that new guardrail has excellent crashworthiness performance. For the evaluation of passenger’s head injury, the research results of this paper possess a definite reference value for guardrail crash safety standards of our country, also provide theoretical basis of double semi-rigid guardrail and derivative structure of waveform guardrail for further research and application, has an important engineering practical value. KEY WORDS:Double-bar semi-rigid guardrail;W-beam guardrail;Uniform design; Impact simulation 4 目 录 摘 要...................................................................................................... II ABSTRACT....................................................................................................III 第一章 绪 论................................................................................................ 7 1.1 研究背景......................................................................................................................................... 7 1.2 国内外防撞护栏研究现状............................................................................................................. 4 1.2.1 国外防撞护栏研究现状.............................................................................4 1.2.2 国内防撞护栏研究现状[7]..........................................................................6 1.3 研究目的及意义............................................................................................................................. 6 1.4 主要研究内容.................................................................................................................................. 7 1.5 研究方法......................................................................................................................................... 7 1.6 本章小结......................................................................................................................................... 8 第二章 防撞护栏试验方法及安全评价标准分析.....................................9 2.1 各国护栏试验方法及评价标准概况............................................................................................. 9 2.1.1 美国 NCHRP Report 350 概况...................................................................9 2.1.2 欧盟 EN1317-2 概况................................................................................ 10 2.1.3 我国 JTG/T F83-01-2004 概况.................................................................10 2.2 各国护栏试验方法及评价标准对比分析................................................................................... 11 2.2.1 各国护栏等级划分及碰撞初始条件....................................................... 11 2.2.2 护栏安全性能评价指标...........................................................................15 2.2.3 评价指标对比分析...................................................................................15 2.3 我国护栏安全评价标准分析....................................................................................................... 21 2.4 本章小结....................................................................................................................................... 23 第三章 双条半刚性护栏结构设计........................................................... 23 3.1 汽车与护栏碰撞机理................................................................................................................... 23 3.2 车辆碰撞防撞护栏后引发骑跨、下钻事故的分析................................................................... 24 3.2.1 骑跨事故分析...........................................................................................24 3.2.2 下钻事故分析...........................................................................................30 3.3 设计思想....................................................................................................................................... 30 5 3.3.1 设计目的...................................................................................................30 3.3.2 结构形式...................................................................................................31 3.3.3 工作原理...................................................................................................31 3.3.4 变形分析...................................................................................................32 3.3.5 双条半刚性护栏特点...............................................................................32 3.4 待求参数分析............................................................................................................................... 33 3.5 参数设计流程............................................................................................................................... 34 3.6 参数范围的确定........................................................................................................................... 35 3.6.1 上护栏板安装高度 H 范围的确定.......................................................... 35 3.6.2 下护栏板安装高度 h 范围的确定...........................................................37 3.6.3 护栏板伸出量差值δ和立柱跨度 L 范围的确定.....................................38 3.7 参数的优化设计............................................................................................................................ 38 3.7.1 均匀设计原理[41][42][43].............................................................................. 39 3.7.2 均匀设计试验...........................................................................................39 3.7.3 数学建模...................................................................................................44 3.7.4 优化处理...................................................................................................45 3.8 本章小结....................................................................................................................................... 47 第四章 汽车-护栏碰撞系统仿真模型的建立......................................... 48 4.1 有限元建模平台........................................................................................................................... 48 4.1.1 仿真软件 LS-DYNA.................................................................................48 4.1.2 前处理软件 HyperMesh[49][50]...................................................................48 4.1.3 汽车与护栏碰撞仿真流程.......................................................................49 4.2 某轿车有限元模型....................................................................................................................... 50 4.3 某货车有限元模型....................................................................................................................... 55 4.4 护栏有限元模型........................................................................................................................... 56 4.4.1 波形护栏板模型.......................................................................................57 4.4.2 立柱模型...................................................................................................59 4.4.3 防阻块模型...............................................................................................59 4.4.4 护栏各组件的连接[56][57].......................................................................... 60 4.5 地面模型....................................................................................................................................... 60 4.6 “车辆-护栏-地面”碰撞体系的耦合..............................................................................................61 4.6.1 碰撞假设与简化处理...............................................................................61 4.6.2 参数确定及计算控制...............................................................................61 6 4.7 本章小结....................................................................................................................................... 64 第五章 汽车-护栏碰撞仿真结果分析..................................................... 65 5.1 试验方案的确定........................................................................................................................... 65 5.2 某轿车与双条半刚性护栏碰撞仿真结果分析........................................................................... 65 5.2.1 碰撞过程及能量变化...............................................................................65 5.2.2 乘员安全性能...........................................................................................66 5.2.3 车辆安全性能...........................................................................................67 5.2.4 护栏防撞性能...........................................................................................67 5.3 某轿车与现有波形护栏仿真结果分析....................................................................................... 68 5.3.1 碰撞过程...................................................................................................68 5.3.2 乘员安全性能...........................................................................................69 5.4 某货车与双条半刚性护栏碰撞仿真结果分析........................................................................... 70 5.4.1 碰撞过程及能量变化...............................................................................70 5.4.2 乘员安全性能...........................................................................................70 5.4.3 车辆安全性能...........................................................................................72 5.4.4 护栏防撞性能...........................................................................................72 5.5 某货车与现有波形护栏仿真结果分析....................................................................................... 72 5.5.1 碰撞过程...................................................................................................72 5.5.2 乘员安全性能...........................................................................................72 5.6 双条半刚性护栏与现有护栏对比分析....................................................................................... 74 5.7 本章小结....................................................................................................................................... 74 第六章 结论与展望....................................................................................75 6.1 结论............................................................................................................................................... 75 6.2 展望............................................................................................................................................... 75 致 谢.......................................................................................................... 76 参考文献...................................................................................................... 77 在学期间发表的论著及取得的科研成果................................................. 81 一、在校期间发表的论文..........................................................................81 二、在校期间参与的科研项目..................................................................81 附录 汽车与护栏碰撞试验仿真图........................................................... 82 一、试验 1: 某轿车与双条半刚性护栏碰撞仿真试验........................82 7 二、试验 2: 某轿车与现有波形护栏碰撞仿真试验............................85 三、试验 3 某货车与双条半刚性护栏碰撞仿真试验............................86 四、试验 4 某货车与现有波形护栏碰撞仿真试验................................87 第一章 绪 论 1.1 研究背景 汽车从诞生之日起,就扮演着重要的角色,它作为当今不可或缺的现代交通 工具,极大地丰富了人们的生活。人们在享受汽车所带来的快捷方便的同时,交 通事故也给社会造成了巨大的损失,交通安全成为人们备受关注的焦点。随着高 速公路的快速发展,交通事故问题日益突出,成为世界各地持续关注的热点问题。 交通安全问题已是一个世界性的大难题[1][2]。 近年来,随着各国汽车安全性能研究的不断深入,道路交通事故呈现出下降 趋势。虽然我国在安全性能研究领域取得了一定的成果,然而道路交通问题仍然 十分严峻,比其他国家严重许多。2000 年,我国万车死亡率是美国的 8.08 倍、英 国的 11.47 倍、德国的 10.68 倍,2006 年我国万车死亡率是美国的 3.62 倍、英国 的 6.48 倍、德国的 6.62 倍,如表 1.1 所示。 表 1.1 2000-2006 年世界部分国家万车死亡率统计表[3] Tab.1.1 Statics of mortality per 10000 vehicles in some countries by the year: 2000-2006 国 别 2000 年 2001 年 2002 年 2003 年 2004 年 2005 年 2006 年 德国 1.46 1.33 1.28 1.23 1.08 0.98 0.93 西班牙 2.48 2.28 2.13 2.10 1.80 1.60 1.44 法国 2.36 2.35 2.16 1.68 1.59 1.43 1.25 意大利 1.61 1.63 1.60 1.43 1.30 1.35 1.31 荷兰 1.36 1.22 1.18 1.23 0.95 0.87 0.84 英国 1.21 1.18 1.15 1.10 1.02 0.99 0.95 美国 1.93 1.91 1.91 1.86 1.80 1.77 1.70 日本 1.20 1.14 1.08 0.99 0.84 0.87 0.80 韩国 7.40 5.50 4.60 4.40 3.90 3.40 3.20 中国 15.60 5.46 13.71 10.81 9.93 7.57 6.16 据统计,自 2000 年以来,道路交通事故四项指标(即事故次数、死亡人数、 2 受伤人数和直接财产损失)基本均以先升高再降低态势进行转化。在 2002 年,道 路交通事故发生次数,死亡人数和受伤人数均达到峰值。数据还表明,在 2000 至 2009 年间,交通事故发生次数下降幅度最大,而死亡人数变化幅度最小(如图 1.1 所示)。可见,道路交通事故发生次数的减少,并不能较为显著的降低人员的死亡 人数。 在高速公路上,其四项指标及占总数的比例关系走势如图 1.2 所示。不难发现, 在高速公路上发生交通事故造成的人员伤亡在数量上和所占比例均为强劲的上升 趋势,直接财产损失自 2003 年之后虽出现下降态势,但其占总数比例仍为上升态 势。 通过对我国高速公路交通事故数据统计做进一步分析可知,随着我国高速公 路管理水平的提高及人们安全意识的不断加强,我国高速公路事故增加率、每百 公里交通事故数总体呈下降趋势,但随着高速公路里程的不断增加,高速公路交 通事故绝对数和致死率(见表 1.2)仍在继续增加,而且事故中属于汽车与护栏碰 撞的绝对数呈强劲的上升势头[4]。 图 1.1 历年全国道路交通事故数据 Fig.1.1 Traffic accident data in the past few years 3 图 1.2 历年高速公路四项指标及占总数比例图 Fig.1.2 Four indicators and proportion of freeways over the past few years 表 1.2 2000-2007 年我国高速公路交通事故数据统计分析表[5] Tab.1.2 Statistical analysis of freeway traffic accidents in China by the year 2000-2007 年份 高速公路里 程(公里) 致死率 (%) 全国交通事故 致死率(%) 百公里 事故次数 百公里 死亡人数 2000 16314 25.1 18.3 119 13 2001 19437 24.0 16.2 129 17 2002 25130 24.3 16.3 119 16 2003 29745 26.3 17.4 122 18 2004 34288 29.1 18.2 71 18 2005 41005 29.0 17.4 44 16 2006 45339 28.0 17.2 32 15 2007 53913 29.2 17.7 23 11 统计结果进一步表明,在我国的道路交通事故中,发生在高速公路上的约有 30%是车辆越出路外造成的,且由此造成的特、重大恶性交通事故占该类事故总数 的比例达 62%以上,我国每年有 1/3 的死亡事故发生在车辆与路侧碰撞的单车事故 中,也就是说,每 3 人死亡事故中,就有 1 人死于车辆驶离道路的事故,且呈逐 年上升趋势 [1][6]。图 1.3 为汽车与护栏碰撞事故。 4 图 1.3 汽车与护栏碰撞事故 Fig.1.3 Accidents between Vehicle and guardrail 因此,在开展汽车自身安全技术研究的同时,在交通道路上尤其是高速公路 上设置合适的防撞护栏对降低交通事故严重程度显得格外重要,通过对现有护栏 安全性的改进和新型护栏安全性设计技术的研究,以提高汽车运行的安全性和保 证乘员人身安全是十分必要和具有现实意义的。 1.2 国内外防撞护栏研究现状 1.2.1 国外防撞护栏研究现状 在美国,众多部门和组织对高速公路防撞护栏的研究都十分重视,例如美国 高速公路交通安全管理局 NHTSA,美国交通运输安全署 AASHTO、美国交通运输 研究委员会 TRB、美国交通部 DOT,美国联邦公路局 FHWA 以及美国德克萨斯 A&M 大学运输研究所 TTI 等。早在 1920 年,美国就开始了对护栏进行了研究和 使用,在理论分析和模拟实验的基础上,通过大量实车足尺护栏碰撞试验,对多 种护栏形式、护栏端头、缓冲装置、防阻块等护栏安全系统进行了全面的、深入 的研究,积累了大量的资料和丰富的经验,制定出了一系列护栏形式选择、结构 设计、实验验证的标准化程序以及生产制造、运输安装和维护的规范和标准[7][8]。 在欧洲,如法国、意大利、德国等在上个世纪六七十年代相继开展了有关防 撞护栏方面的研究工作,从理论和实验上研究了不同结构形式的护栏,建立、健 全了相应的实验设施及实验规程。 日本从 50 年代开始这方面的研究,并在名神高速公路开始大规模使用护栏。 在随后十几年中,日本的众多研究机构对各种护栏进行了广泛深入的研究,于 1965 年制定了护栏设置纲要,对护栏的适用范围,结构设计,功能要求、施工安装等 方面做出了明确的规定[9]。 新型防撞护栏结构形式的研究、防撞护栏材料的选用及防撞护栏安全性能评 价仍然是当今交通界的研究热点,其中以下两点的研究尤为活跃: ①防撞护栏结构形式研究 5 按照在公路中的纵向设置位置,护栏可分为路基护栏和桥梁护栏;按其在公 路中的横向设置位置,可分为路侧护栏和中央分隔带护栏;根据碰撞后的变形程 度,护栏可分为刚性护栏、半刚性护栏和柔性护栏,其主要代表型式分别为混凝 土护栏、波形护栏和缆索护栏[10]。以双波为代表的半刚性护栏应用最为广泛,对 其结构形式的研究比较突出。如 L.C. Bank, T.R. Gentry[11]开发的拉挤复合材料型护 栏,利用护栏板自身材料组合结构进行受控撕裂从而吸收碰撞能量,而非采用弹 性材料的塑性变形吸能,提供了一种波形护栏设计思想。K.E., Engstrand[12]研究了 双波护栏板间的连接方式,以减少碰撞过程中的脱离现象。M Vesenjak 等人[13]分 别对双波护栏的 U 型、Z 型、六边形型及 D 型防阻块结构进行了碰撞性能探讨, 得出六边形结构形式的防阻块所受车辆碰撞角度影响较小以及在吸能方面有明显 优势。M. Borovinšk 等学者[14]讨论了三种波形护栏衍生结构的防撞性能,如图 1.4 所示。第一种是在防阻块后新设一根钢条,第二种是在立柱上新增一钢条,第三 种则结合半刚性护栏与柔性护栏结构形式,在半刚性护栏的双波后面加载两条钢 缆。运用有限元仿真试验对比分析,得出第二种结构形式在不过大地牺牲护栏最 大变形量指标和车辆加速度限制指标的前提下,可以更为有效地校正车辆运行轨 迹。 图 1.4 波形护栏衍生结构 Fig.1.4 Derivative structure of waveform guardrail ②护栏板高度研究 以双波半刚性护栏为例,护栏主要有护栏板、防阻块、立柱等基本构件组成。 护栏板高度对碰撞车辆运动状态有着重大影响。高度过低很容易引起车辆发生骑 跨、侧翻甚至冲出护栏的交通事故,造成严重损失;高度过高则易于引发车辆下 钻护栏事故,尤其是轿车更为明显,损失也十分惨重。Reid J.D.[15] 、Faller P.K.[16] 等学者研究了护栏高度对其防撞性能的影响。Sicking D.L.[17]等从碰撞车辆重心的 角度考虑相适应护栏板高度,并采用全尺实车碰撞试验和计算机仿真方法验证了 新护栏高度的适用性。Marzougui, D.[18]等则以碰撞车辆保险杠高度的角度出发考虑 6 相应的护栏板高度。 不难发现,为了适应汽车向微型化、大型化和重型化演变的需要,有效保证 车辆和乘员的安全,众多学者在对各种新型防撞护栏的结构和护栏板的高度方面 进行了大量的研究和探索,并提出了各种新颖的防撞护栏结构和护栏板高度,值 得我们借鉴和学习。 1.2.2 国内防撞护栏研究现状[7] 我国在“七五”期间开始针对高速公路护栏的设计、生产与施工等方面展开了研 究。交通部公路科学研究所从 1984 年开始对波形梁护栏进行了系统的研究,根据 我国的护栏设计条件,提出了适合我国国情的护栏结构形式。该结构采用厚度 3mm 的深波纹横梁,Z 字形开口型钢立柱的形式,从 1989 年起在全国推广应用。但根 据随后几年的在高速公路、一级公路的工程实践得出,Z 形柱强度太弱,损坏严重, 不利于行车安全。故交通部公路管理司于 1994 年 5 月下令停止使用波形梁护栏“Z” 形柱。1992 年前后,中国公路工程咨询监理总公司组织有关人员对全国已通车的 高速公路护栏的使用情况作了调查。据此拟定了“波形梁护栏实车碰撞试验方案”。 经交通部工管司批准,公司联系了近十个单位组织了近百人的实验研究课题组, 进行了一年多的工作,完成了我国第一次实车足尺碰撞试验的研究任务,建立了 一整套实验方法和设施,紧接着公司又承担了“玻璃钢护栏的实验研究”工作并通过 分析、计算和实验圆满地完成了这项工作。1992 年底,交通部公路科学研究所在 总结全国护栏实际应用的基础上,推出了新型的变截面波形梁护栏结构形式。该 结构由于横梁采用变截面形式,横梁在搭接处结合紧密,使高强螺栓的性能得以 充分发挥,横梁在搭接处产生断裂的可能性大为减小,从而保证了横梁的连续作 用,并使线形更加顺适美观,造价降低。该结构形式已应用于首都机场和成渝高 速公路,并将作为我国公路护栏的基本结构形式列入交通行业标准,在全国推广 应用。到 1994 年初我国制定了行业标准(JTJ074—94)《高速公路交通安全设施设 计及施工技术规范》;到 1997 年,交通部公路科学研究所就开发了可用于高速公 路设施碰撞研究的试验手段,为防撞护栏的试验研究创造了更好的条件。近年来 随着经济建设和高速公路投入运营,重型车和大型车的比例突增,由于其吨位大、 车速高使得目前高速公路上使用的波形梁护栏已经不能满足其安全要求,从而引 发的事故严重度很高。2000 年,交通部编写发布了《公路三波形梁钢护栏》行业 标准并推广应用,主要用于重型车、大型车比例高的路段和山区高速公路等地形 不利之处。 1.3 研究目的及意义 虽然我国的防撞护栏在研究和实践上取得了一定的进步,但整体上与国外相 7 比还是存在一定的差距。当前,我国半刚性防撞护栏已无法满足交通安全要求, 主要表现在: ①护栏设计基本参照国外的相关标准和规范,而国内道路状况、汽车类型、 行驶车速以及道路限速等诸多因素并不与国外相一致,防撞护栏的安全性能尚未 完全得到发挥。 ②车型格局的变化,高速公路上的车型向微型化和重型化两个方向发展。车 型微型化因车身变得更小更低而必将增加碰撞现有半刚性护栏时发生绊阻、钻入 护栏的可能性;车型巨型化因质量更大、重心更高而提高碰撞现有半刚性护栏车 辆骑跨或翻车甚至冲出护栏的风险性。 ③某些高速公路因路面修复在原路面增铺一层沥青路面,相应降低了护栏的 高度,尤其对大型车的安全防护极为不利。 因此,为了同时有效地防止汽车微型化引发的车辆下钻护栏事故和汽车重型 化造成的车辆骑跨甚至冲出护栏的事故发生,缩小我国与国外防撞护栏水平,保 证乘员基本安全和减小碰撞事故损失,有必要对现有半刚性护栏进行深入研究。 1.4 主要研究内容 本文从汽车与护栏碰撞力学模型研究出发,设置双条半刚性护栏基本结构尺 寸,采用 HyperMesh 和 LS-DYNA 软件,利用动态显示非线性有限元方法建立和 求解“汽车-双条半刚性护栏”耦合模型,从碰撞后车内乘员安全性、车体加速度、 车辆运行状态、车辆运行轨迹和护栏最大变形量等角度研究其碰撞安全性能,以 及与“汽车-半刚性护栏”模型碰撞结果进行对比分析,修正双条半刚性护栏结构参 数,并验证双条半刚性护栏安全性能优越于其他形式护栏。具体研究内容如下: ①对欧盟《高速公路护栏安全性能评价标准》(BSEN1317-1998)、美国《高速 公路安全设施安全性能评价推荐程序》(NCHRP Report 350)和我国的《高速公路 护栏安全性能评价标准》(JTG/TF83-01-2004)进行对比分析,结合我国《实车正 面碰撞乘员保护设计规则》(CMVDR,294)探讨适合我国护栏碰撞中乘员安全评 价方法。 ②双条半刚性护栏结构形式研究及参数确定。 ③双条半刚性护栏碰撞性能仿真研究。 1.5 研究方法 首先,在双条半刚性护栏结构参数设计过程中,采用均匀设计试验方法。均 匀设计(Uniform Design)是基于试验点在整个试验范围内均匀散布的从均匀性角度 出发的一种试验设计方法,它着重在试验范围内考虑试验点均匀散布以求通过最 8 少的试验来获得最多的信息,适合于多因素多水平的试验和系统模型完全未知的 情况。通过均匀设计试验方法,在 DPS 数据处理平台上构建护栏安全评价指标与 护栏结构参数的数学模型,借助各个护栏安全评价指标来确定双条半刚性护栏的 结构参数。 其次,采用 MATLAB 软件中 fmincon 函数进行双条半刚性护栏结构参数的优 化。fmincon 函数可以很好的解决非线性多变量约束最优化问题,因此,采用此优 化函数。 最后,在 HyperMesh 软件中建立汽车与护栏碰撞模型,提交至 LS-DYNA 软 件进行计算机仿真试验。目前,汽车与护栏碰撞的研究方法主要有三种:实车足 尺碰撞试验法、缩尺模型试验法和计算机仿真法。由于实验条件和成本的限制, 本文采用计算机仿真方法进行研究。 计算机仿真法是根据力学原理,通过理论分析建立相应的数学模型,借助计 算机进行数值模拟计算,仿真汽车与护栏实际碰撞过程以获取碰撞数据的方法。 由于这种方法具有成本低廉、方便快捷、可重复性好等优点,现已成为实车碰撞 的有力补充和重要参考。随着计算机技术和计算算法的快速发展,计算机模拟在 研究汽车碰撞安全领域得到广泛应用,尤其在乘员保护措施、汽车和护栏结构的 优化等方面发挥着巨大作用。目前,较为常用的力学模型主要以有限元模型和多 刚体模型为主[19][20][21][22],其仿真软件包括 ANSYS、LS-DYNA、MADYMO、 PAM-CRASH、PC-CRASH、ADAMS、VGP 等。在对汽车与护栏碰撞仿真分析时, 大多数还是以动态显示非线性有限元为理论依据,软件 LS-DYNA 最具代表性。 1.6 本章小结 本章根据事故统计数据发现汽车与护栏碰撞事故具有普遍性和严重性;随后 介绍了国内外防撞护栏的研究现状;在此基础上提出本文研究的目的及意义、主 要研究内容,最后归纳了常用研究方法,以及本文所采用的方法。 9 第二章 防撞护栏试验方法及安全评价标准分析 随着世界各国高速公路的不断发展,防撞护栏对交通安全起到了至关重要的作 用。防撞护栏的安全评价是检查护栏能否起到保护车辆作用的重要指标,也是考 察护栏在事故中是否减少人员伤亡和财产损失的重要体现,防撞护栏的安全性能 评价也一直备受各国研究人员的关注。 目前,世界各国的高速公路护栏安全性能评价已逐渐发展并形成两大主要评价 体系,即以美国公路合作研究组织 NCHPR(National Cooperative Highway Research Program)为代表编著的《高速公路安全设施安全性能评价推荐程序》(NCHRP Report 350)和欧盟标准化委员会 CEN(Committee European Normalization)为代 表编写的《高速公路护栏安全性能评价标准》(EN1317-2)。我国的高速公路护栏 安全性能评价标准(JTG/T F83-01-2004)则以欧盟的 EN1317 和美国的 NCHRP350 为蓝本,并结合我国实际情况编写而成。 2.1 各国护栏试验方法及评价标准概况 2.1.1 美国 NCHRP Report 350 概况 美国是最早进行高速公路安全护栏试验和评价标准研究工作的,早在 1962 年, 由几家安全护栏研究机构在“Highway Research Correlation Services Circular 482”发 表了仅一页的安全护栏实车碰撞试验程序。它只是简单地规定了试验车质量、碰 撞速度及碰撞角度参数,但没有详细的评判标准。1973 年,在政府的资助下由 Southwest Research Institute 主持了 NCHRP Project 22-2 研究计划,其后发表了 NCHRP Report 153。包括对护栏防撞性能的评价、护栏各部件脱离评价、车辆碰 撞最大加速度限制等内容[23]。这个只有 16 页的研究报告结合了美国 70 多家研究 机构及个人的研究成果。其安全护栏的试验及性能评价标准得到了广泛的应用。 10 NCHRP Report 153 在经过不断的试验及修订后,于 1980 年颁布了新的安全护 栏试验及评价标准 NCHRP Report 230。该标准对 NCHRP Report 153 进行了大量的 修改,其适用范围也进一步扩大。该报告还引入了基于“连枷空间模型”的乘员风险 评价标准,对乘员损伤的评价更为接近实际碰撞情况[24]。 从 1989 年后以首席调查员 Dr. Hayes Ross 和其助手 Jarvis Mishie 为首的研究 小组对 NCHRP Report 230 进行了大量的试验及研究,起草了修改草案,于 1993 年发表了新的安全护栏试验及评价标准 NCHRP Report 350,提出了 6 种护栏等级 与评价标准及其测试程序,并规定各种道路上使用的新型护栏都须安装 350 报告 规定的等级和程序进行实车碰撞[25]。新标准和 NCHRP Report 230 相比,有更加详 细的安全护栏试验及评价标准。至此,NCHRP Report 350 基本成为世界各国采用 的通用的安全护栏试验及性能评价准则[26]。 2.1.2 欧盟 EN1317-2 概况 英国安全护栏碰撞试验及评价标准 BS 6779 是 1987 年 8 月第一次颁布的,后 来分别在 1990 年、1992 年及 1998 年进行了修订。先普遍采用的标准是 1998 年 3 月颁布的第四次修订的版本。同年英国的 BSI 同时发布了以 BS 6779 为蓝本的英 文版标准 BS EN1317:1998。该标准同时也被欧洲委员会 CEN(Committee European Normalization)订为欧共体国家的通用标准。该标准原定于 2001 年 1 月 1 日将完 全取代现行的英国安全护栏的标准 BS 6779。现在欧洲安全护栏的试验方法及评价 标准 BS EN1317:1998 与英国标准 BS 6779 仍并存。BS EN1317:1998 对 BS 6779 进行了大量的修改,增加了安全护栏的评定等级及试验的种类等很多细节,正逐 步向美国的 NCHRP Report 350 靠拢[26]。 BS EN1317:1998 主要由六大部分组成,包括常规标准测试方法及术语(EN 1317-1);护栏安全性能等级、试验方法及评价标准(EN 1317-2);防撞垫性能等 级、试验方法及评价标准(EN 1317-3);护栏端头、过渡护栏性能等级、试验方法 及评价标准(EN 1317-4);耐久性评价标准(EN 1317-5)以及行人护栏(EN 1317-6)。 2.1.3 我国 JTG/T F83-01-2004 概况 我国有关高速公路护栏安全评估始于《高速公路交通安全设施设计及施工技 术规范》(JTJ074-94),该规范对高速公路其他交通安全设施也进行了研究。而单 独以护栏作为评估对象的标准,是 2004 年 12 月颁布的《高速公路护栏安全性能 评价标准》(JTG/T F83-01-2004)(以下简称 F83)。F83 以欧盟的 EN1317 和美国 的 NCHRP350 为蓝本,并结合我国实际情况编写而成,标准第一次详细地提出了 详细的试验方法和评价标准,为高速公路护栏安全评价提供了理论依据。 11 2.2 各国护栏试验方法及评价标准对比分析 2.2.1 各国护栏等级划分及碰撞初始条件 ①美国护栏等级划分及碰撞初始条件[27] 护栏的测试分为六个等级,每个等级对长护栏和过渡段均有严格的测试,包 括不同车型、碰撞速度和碰撞角度,具体的安全护栏试验评定等级及试验方法见 表 2.1。 表 2.1 NCHRP Report 350 护栏试验评定等级及试验方法 Tab.2.1 Rating guardrail test and test methods in NCHRP Report 350 试验等级 护栏类型 测试种类 碰撞条件 车辆类型 碰撞速度 (km/h) 碰撞角度 ( °) 1 长护栏 1-10 820C(轿车) 50 20 S1-10a 700C(轿车) 50 20 1-11 2000P(皮卡) 50 25 过渡段 1-20d 820C(轿车) 50 20 S1-20a 700C(轿车) 50 20 1-21 2000P(皮卡) 50 25 2 长护栏 2-10 820C(轿车) 70 20 S2-10a 700C(轿车) 70 20 2-11 2000P(皮卡) 70 25 过渡段 2-20d 820C(轿车) 70 20 S2-20a 700C(轿车) 70 20 2-21 2000P(皮卡) 70 25 3 长护栏 3-10 820C(轿车) 100 20 S3-10a 700C(轿车) 100 20 3-11 2000P(皮卡) 100 25 过渡段 3-20d 820C(轿车) 100 20 S3-20a 700C(轿车) 100 20 3-21 2000P(皮卡) 100 25 4 长护栏 4-10 820C(轿车) 100 20 S4-10a 700C(轿车) 100 20 4-11d 2000P(皮卡) 100 25 4-12 8000S(厢式货车) 80 15 过渡段 4-20d 820C(轿车) 100 20 S4-20a 700C(轿车) 100 20 4-21d 2000P(皮卡) 100 25 12 4-22 8000S(厢式货车) 80 15 5 长护栏 5-10 820C(轿车) 100 20 S5-10a 700C(轿车) 100 20 5-11d 2000P(皮卡) 100 25 5-12 36000V(厢式拖车) 80 15 过渡段 5-20d 820C(轿车) 100 20 S5-20a 700C(轿车) 100 20 5-21d 2000P(皮卡) 100 25 5-22 36000V(厢式拖车) 80 15 6 长护栏 6-10 820C(轿车) 100 20 S6-10a 700C(轿车) 100 20 6-11d 2000P(皮卡) 100 25 6-12 36000T(油罐拖车) 80 15 过渡段 6-20d 820C(轿车) 100 20 S6-20a 700C(轿车) 100 20 6-21d 2000P(皮卡) 100 25 6-22 36000T(油罐拖车) 80 15 ②欧洲护栏等级划分及碰撞初始条件 1)护栏等级的划分[28] 按照欧盟《高速公路护栏安全性能评价标准》(BS EN1317-1998)的划分标准, 根据护栏的测试种类和测试标准,可将护栏划分为低约束、正常约束、高约束和 超高约束护栏。如表 2.2 所示。 2)护栏碰撞初始条件 一般地,汽车碰撞护栏的初始条件包括:a.碰撞速度,即实际碰撞点前 6m 以 内所测定的试验车辆实际行驶速度;b.碰撞角度,实际碰撞点位置车辆中心线与护 栏导向方向的夹角;c.车辆质量;d.碰撞车型。由于不同的车型、不同的护栏约束 等级等,汽车碰撞护栏的初始条件也有所差别,具体如表 2.3 所示,所用测试车辆 如图 2.1 所示。 13 图 2.1 各种测试车型 Fig.2.1 The vehicle models in crash tests 表 2.2 欧盟护栏等级划分 Tab.2.2 Levels of guardrail in EU 测试等级 测试种类 低约束 T1 TB21 T2 TB22 T3 TB41+TB21 正常约束 N1 TB31 N2 TB32+TB11 高约束 HI TB42+TB11 H2 TB51+TB11 H3 TB61+TB11 特高约束 H4a TB71+TB11 H4b TB81+TB11 表 2.3 汽车碰撞测试标准 Tab.2.3 Vehicle crash test criterion 测试种类 碰撞速度 (km/h) 碰撞角度 ( °) 车辆质量 (kg) 试车类型 TB11 100 20 900 轿车 TB21 80 8 1300 轿车 14 TB22 80 15 1300 轿车 TB31 80 20 1500 轿车 TB32 110 20 1500 轿车 TB41 70 8 10000 载重汽车 TB42 70 15 10000 载重汽车 TB51 70 20 13000 大型客车 TB61 80 20 16000 载重汽车 TB71 65 20 30000 载重汽车 TB81 65 20 38000 载重汽车 ③我国护栏等级划分及碰撞初始条件 1)护栏等级的划分 公路护栏按照防撞等级可分为:路侧 B、A、SB、SA、SS 五级;中央分隔带 Am、SBm、Sam 三级,各等级护栏的碰撞条件和性能应满足表 2.4 的规定[29]。在 我国高速公路上以双波为代表的半刚性护栏应用最为广泛,与其碰撞的研究也较 多。护栏的防撞等级划分如表 2.4 所示。本文以 Am 为试验方法。 2)护栏碰撞初始条件 根据交通部公路科学研究所的课题组对“十一五”前期全国大部分高速的调研 情况,确定了符合我国当时基本国情的护栏碰撞初始条件,如表 2.5 所示。本文的 研究采用第一、三种碰撞初始条件,即碰撞速度分别为 100km/h、60km/h,碰撞角 度均为 20°,车辆质量分别为 1500kg、10000kg。 表 2.4 我国护栏防撞等级 Tab.2.4 The level of guardrail crashworthiness in China 防撞等级 碰撞试验条件 路侧 中央分隔带 碰撞速度 (km/s) 碰撞角度 (°) 碰撞质量 (t) B — 100 20 1.5 40 20 10 A Am 100 20 1.5 60 20 10 SB SBm 100 20 1.5 80 20 10 SA SAm 100 20 1.5 80 20 14 SS — 100 20 1.5 80 20 18 表 2.5 我国汽车与护栏碰撞初始条件 15 Tab.2.5 The initial conditions of the vehicle crash with guardrail in China 车型 碰撞速度 (km/h) 碰撞角度 ( °) 车辆质量 (kg) 小轿车 100 20 1500 大客车 80 20 10000,14000,18000大货车 60 20 2.2.2 护栏安全性能评价指标 高速公路护栏安全性能指标主要包括以下几个方面: ①乘员安全评价指标 高速公路护栏安全性能评价最终将归结于对乘员安全性的评价,只是采用了 不同的评价方法: 1)安装假人情况时,在危及生命安全的假人身体关键部位添加相应传感器, 获取并计算得出如假人头部性能指标 HPC、假人胸部性能指标 THPC 和假人腿部 性能指标 FPC 等相关数据,数据未超过法规规定极限值即视为护栏安全性能良好。 2)不具备安装假人时,用测量车体加速度的间接方法,以作为车内乘员安全 性能的替代指标。当车体加速度未超过法规规定极限值时,护栏安全性能视为良 好。 ②车辆安全性能评价指标 车辆碰撞护栏后的运行状态和运行轨迹对乘员损伤严重程度有着很大的影响, 主要体现在下面两个方面: 1)运行状态:在车辆碰撞护栏过程中,车辆常见危险行驶姿态有:穿越护栏、 骑跨护栏、翻越护栏、下钻护栏、与护栏发生阻绊、横转、掉头等,发生这些情 况均会导致严重后果,在碰撞过程中是不允许发生的。 2)运行轨迹:车辆碰撞护栏时,由于车辆自身的惯性、护栏的导向和反弹作 用,可能出现车辆碰后驶出角度过大,易侵入其他车道并与该车道正常行驶的车 辆发生二次事故,造成更为严重的交通事故。 ③护栏防撞性能评价指标 1)护栏最大动态变形量:为了避免车辆翻出路外,结合道路周边环境,护栏 的最大动态变形量不能超过法规规定值。 2)脱离物件:在碰撞过程中,脱离组件、碰撞碎片(如护栏的固定螺栓、防 阻块等)以及其他护栏上的碰撞物体不能侵入驾驶室内及阻挡驾驶员的视线。 2.2.3 评价指标对比分析 ①乘员安全评价指标 1)美国护栏安全评价标准中乘员安全评价指标[26] [27] 16 在美国护栏安全评价标准中,关于乘员安全评价主要包括两个指标,即乘员 碰撞速度 OIV(Occupant Impact Velocities)和乘员撞击加速度 ORA(Occupant Ride down Accelerations)。 a.乘员碰撞速度 OIV , ,0 t X Y x yV a dt 式(2.1) 其中, ,X YV ——乘员与汽车内部碰撞时在 X,Y 方向上的速度; ,x ya ——试验车辆在 X,Y 方向上的加速度; *t ——车内乘员因碰撞纵向位移 0.6m 或横向位移 0.3m 所经历的时间中较 小的一个,确定方法如下: 2 ,0 0 , t t x yX Y a dt 式(2.2) 其中,X=0.6m,为乘员纵向位移量; Y=0.3m,为乘员横向位移量。 由上面两个积分式可分别求出对应于 X=0.6m 的积分时间 * Xt 及对应于 Y=0.3m 的积分时间 * Yt , *t 为 * Xt 和 * Yt 中较小者。 b.乘员撞击加速度 ORA 乘员撞击加速度采用车体在 X 和 Y 方向上碰撞加速度的处理值,即为车体加 速度 10ms 间隔平均值的最大值。 2)欧洲护栏安全评价标准中乘员安全评价指标[28][30][31] 欧盟的护栏碰撞实验评价标准中,采用三个乘员安全评价指标,即:乘员加 速 度 伤 害 指 标 ASI ( Acceleration Severity Index )、 碰 撞 后 头 部 减 速 度 PHD (Post-impact Head Deceleration)和理论头部碰撞速度 THIV(Theoretical Head Impact Velocity)。 a.乘员加速度伤害指标 ASI 乘员的加速度伤害指标 ASI 是通过车辆重心处 P 点的加速度传感器获取的三 个方向的加速度,经过计算推导出来的乘员安全评价指标。其计算公式为: 1/222 2 x x y y z zˆ ˆ ˆASI(t)= a / a a / a a / a 式(2.3) 式中:âx、ây、âz 分别为车辆重心处加速度 ax、ay、az 三个分量的极限值,标 准规定佩有安全带的乘员所取的极限值分别为:20g、9g、10g( g 为重力加速度, 取 9.81m/s2);而āx、āy、āz 分别为车辆重心处加速度 ax、ay、az 三个分量任意 50ms 时段的平均值,即: x 1a t xt a dt ; y 1a t yt a dt ; z 1a t zt a dt 式(2.4) 17 b.理论头部碰撞速度 THIV 碰撞后头部减速度 PHD 和理论头部碰撞速度 THIV 的计算是基于“Flail Space Model(连枷空间模型)”的假设,它的基本原理如图 2.2 所示。 图 2.2 连枷空间模型(左碰情况) Fig.2.2 Impact of the theoretical head on the left side 假定碰撞过程中,乘员被看成可自由移动的质点(头部),只考虑车辆在水平 面的纵向运动、横向运动和横摆,车辆的俯仰、翻转和竖向运动均忽略不计,车 辆与护栏的碰撞过程中有以下几个主要阶段: 在车辆与护栏碰撞的初始瞬间,乘员(头部)与车体速度相同,假定此时乘 员(头部)和车辆重心 C 间距为 x0(车体坐标系),乘员舱内表面与乘员(头部) 的纵向和横向间距分别为 Dx 和 Dy,即为乘员(头部)从初始位置至撞击乘员舱内 部所经历的位移(车体坐标系),取值为:Dx=0.6m,Dy=0.3m。 在车辆与护栏碰撞而改变速度的过程中,乘员(头部)的运动位移分别为 xb 和 yb(相对于车体坐标系),乘员(头部)连续运动直到 T 时刻撞击乘员舱内表面, 例如图 2.2,yb=Dy,则乘员(头部)撞击乘员舱左侧面;若 xb=Dx+x0,则乘员(头 部)撞击乘员舱前侧面。在碰撞瞬间(T 时刻),若乘员(头部)相对于车体坐标 系的速度分别为 Vx(T)和 Vy(T),则: 1/22 2 x yTHIV= V (T)+V (T) 式(2.5) 即 THIV(头部碰撞速度)为 Vx(T)和 Vy(T)的合成值,该指标用于衡量乘员(头 部)撞击乘员舱内表面的剧烈程度。 c.碰撞后头部减速度 PHD 18 乘员(头部)和乘员舱内部碰撞后,保持与乘员舱内表面接触的状态经历后 续的车辆-护栏碰撞过程,因此,在后续的碰撞过程中,乘员(头部)和车体的 加速度相同,若车体纵向和横向加速度 10ms 平均值的时程分别为 cx (t) 和 cy (t) , 则碰撞后头部减速度: 2 2 1/2 c cPHD=MAX[(x (t)+y (t)) ] (t>T) 式(2.6) 3)我国护栏安全评价标准中乘员安全评价指标[31][32] 在我国现行护栏相关规范中,《高速公路交通工程及沿线设施设计通用规范》 (JTG D80-2006)(以下简称 D80)、《公路交通安全设施设计规范》(JTG D81-2006) (以下简称 D81)均以车体 10ms 间隔平均加速度作为乘员安全评价指标,而 F83 中规定有两种途径:其一是车体 10ms 间隔平均加速度。虽然各标准的评价指标均 有车体 10ms 间隔平均加速度,但作为评价基准的指标取值方向(纵向、横向、竖 直方向的单向值还是合成值)都各不相同;其二是采用我国《实车正面碰撞乘员 保护设计规则》(CMVD294)中的假人伤害指标。尽管在 2003 年时,对 M1 类乘 用 车 强 制 实 施 的 汽 车 碰 撞 安 全 法 规 《 实 车 正 面 碰 撞 乘 员 保 护 设 计 规 则 》 (CMVDR294)已经升级为《乘用车正面碰撞的乘员保护》(GB11551-2003)[33], 但对假人伤害指标的基本评价方法并未改变,即头部综合性能指标 HPC、胸部性 能指标 THPC 和腿部性能指标 FPC。 a.头部综合性能指标 HPC 2 1 2.5 2 1 2 1 1 t t HPC t t adtt t ≤1000 式(2.7) 式中, a ——假人头部中心的合成加速度; 1 2,t t —— 碰 撞 中 从 初 始 接 触 到 最 后 接 触 过 程 中 的 任 意 两 个 时 刻 , 2 1 36t t ms 。 b.胸部性能指标 THPC 为胸部压缩量,即胸部变形的绝对值。 c.大腿性能指标 FPC 大腿轴向压力,即轴向传递至假人每条大腿的压力。 4)各国护栏安全评价标准中乘员安全评价指标对比 表 2.6 为我国和欧盟、美国护栏安全评价标准中乘员安全(或损伤)评价标准 比较表,通过比较分析,我们可以得到如下结论: 表 2.6 各国高速公路护栏碰撞乘员损伤评价比较表 Tab.2.6 Assessment comparison of the person's damage degree 19 指标 国别 评价指标 限值范围 美国 乘员碰撞速度 OIV 纵向:推荐值 3m/s,最大值 5m/s 纵向和横向:推荐值 9m/s,最大值 12m/s 乘员撞击加速度 ORA△t=10ms 纵向和横向:推荐值 15g,最大值 20g 欧盟 加速度伤害指标 ASI△t=50ms 等级 A ASI≤1.0 等级 B 1.0<ASI≤1.4 等级 C 1.4<ASI≤1.9 碰撞后头部减速度 PHD△t=10ms 纵向和轴向合成值≤20g 理论头部碰撞速度 THIV ≤33km/h 中国 F83 假人 伤害 指标 头部性能指标 HPC△t=36ms ≤1000 胸部性能指标 THPC ≤75mm 腿部性能指标 FPC ≤10kN 车体 10ms 间隔平均加速度 纵向、横向、竖直方向≤20g D80 车体 10ms 间隔平均加速度 ≤20g D81 车体 10ms 间隔平均加速度 三个方向合成值≤200m/s2(≈20.4g) a.各评价标准中部分指标所取时间间隔不同。如我国 F83 中的 HPC 采用的 是 36ms,欧洲标准中 ASI 取 50ms、PHD 取 10ms,美国标准中 ORA 取 10ms 等。 b.各评价标准中采用车体加速度作为乘员损伤评价指标的,加速度取值方向 存在不同。 c.欧盟标准中的理论头部碰撞速度 THIV 和美国标准中的乘员碰撞速度 OIV 尽管计算方法略有不同,但二者的指标极限值基本一致,欧盟 THIV 的限值为 33km/h(≈9.17m/s),美国 OIV 的限值为:理想值 9m/s、最大值 12m/s; d.欧盟的 PHD 和美国的 ORA 均表征乘员(头部)与驾驶舱内部碰撞之后乘 员所经历的车辆加速度,欧盟 PHD 的限值为 20g,美国 ORA 的限值为:推荐值 15g、最大值 20g。 ②车辆安全性能评价指标 本指标目的是当车辆与护栏发生碰撞后,防止因护栏的弹性变形和车辆自身 的惯性等因素,使得车辆驶离本车道与相邻车道来往的车辆发生二次碰撞事故。 各国评价指标见表 2.7 所示。 表 2.7 各国车辆安全性能评价指标比较表 Tab.2.7 Assessment comparison of the vehicle safety performance 指标 国别 评价标准 美国 车辆的驶出角度不大于驶入角度的 60% 欧洲 车辆在碰撞后从碰撞点开始以后距离 B 以内,车辆的任何部位均不能越过与 20 护栏距离为 ( 16% )A W L 的平行线。 其中, W——车宽; L——车长; A、B——距离限制,取值如下所示。 车型 A(m) B(m) 轿车 2.2 10.0 其他车型 4.4 20.0 中国 车辆的驶出角度不大于驶入角度的 60% ③护栏防撞性能评价指标 由于护栏的外侧情况各不相同,有大江大河、悬崖峭壁等危险程度很高的路 段,车辆如果掉下去车内的乘员可能会无一生还。而有些路段问题并没有这样严 重,路侧情况与中央分隔带的情况存在不同。因此根据不同路段、不同形式、不 同材料的护栏,规定不同的护栏最大动态变形量是很有必要的,可以在保证安全 的前提下有效地降低成本。 表 2.8 各国护栏防撞性能评价指标比较表 Tab.2.8 Assessment comparison of the guardrail crashworthiness 指标 国别 评价标准 美国 被测护栏必须始终阻挡试验车辆并改变其行驶方向;试验车辆不得穿透、骑跨或 越过护栏,但忽略在规定范围内的横向变形弯曲是允许的。 欧洲 包含两个评价指标: ①护栏最大变形 D 和②响应宽度 W,如下图所示。其中 W 是车体或护栏在 碰撞过程中最外缘到护栏变形时最内缘的最大动态距离,如下表所示。 护栏最大变形 D 和响应宽度 W 响应宽度 W 各级限值 21 碰撞宽度等级 横向最大位移(m) W1 W≤0.6 W2 W≤0.8 W3 W≤1.0 W4 W≤1.3 W5 W≤1.7 W6 W≤2.1 W7 W≤2.5 W8 W≤3.5 中国 刚性护栏最大动态变形量≤10cm; 半刚性三波护栏最大动态变形量≤75cm; 半刚性双波护栏最大动态变形量≤100cm; 柔性护栏可根据其安装位置参照半刚性护栏最大动态变形量的指标。 2.3 我国护栏安全评价标准分析 我国第一个关于高速公路护栏评价的标准——《高速公路护栏安全性能评价 标准》(JTG/TF83-01-2004)中乘员损伤评价(带假人情况)采用我国正面碰撞 CMVDR294 法规中的评判标准,尽管两个标准均属于汽车碰撞范畴,但车辆与护 栏的碰撞和车辆的正面碰撞有着极大的区别: ①碰撞角度的不同。车辆与护栏碰撞具有一定的夹角,如我国高速公路护栏 安全性能评价中采用的碰撞角度(车辆行驶方向与护栏的夹角)为 20°;而正面碰 撞的形式多样,较为接近的是车辆左、右侧与 30 楔形块的斜碰撞,按照护栏碰撞 情况折算的碰撞角度是 60°,二者的碰撞角度相差较大。 ②碰撞速度不同。正面碰撞法规中车辆的碰撞速度为 50km/h 左右,而在汽车 与护栏碰撞规范中,以小轿车为例,碰撞速度高达 100km/h。 ③碰撞对象不同。车辆与护栏碰撞试验中,车辆碰撞的为护栏;在正面碰撞 试验中,碰撞的物体是障碍壁、B 柱等。前者结构细而长,变形区域宽,而后者结 构较为方正,变形范围窄。 ④车辆运动状态不同。车辆与护栏碰撞试验中,车辆在与护栏发生碰撞后, 车体并不立即停下,而是在护栏的导向作用下,顺着护栏方向继续前行,逐步恢 复到正常行驶方向上直至停止;在正面碰撞试验中,车体直接因障碍壁等物体的 阻挡而立即停止。 ⑤乘员运动形态不同。车辆与护栏碰撞试验中,在发生碰撞时,车体的运动 在横、纵方向均有较大的变化,车内乘员的运动方式也会随着车体运动的改变而 变化,除了具备正面碰撞乘员在纵向运动特征外,还具有横向运动特征。若车辆 的碰撞速度高,则与护栏碰撞较为剧烈,乘员头部还有可能与侧面窗户等物件发 22 生碰撞,增加了乘员的损伤风险性。在正面碰撞试验中,乘员与侧窗发生碰撞的 可能性极小。 由此可见,车辆与护栏碰撞形式与正面碰撞形式是不同的,前者能否采用后 者的乘员损伤评价方法,有待商榷。 欧盟的 ASI 与我国的 HPC 没有直接的联系,但由于它们均能表示乘员伤害情 况,所以两者还是存在一定的相关性。国内外学者也对它们的相关性进行了研究。 我国《高速公路护栏安全性能评价标准》主要起草人于树平和乔希永等研究人员 曾通过实车试验探讨了护栏碰撞试验乘员加速度伤害指标 ASI 和头部损伤指标 HPC(其计算方式与 HIC 一致)的关系,实验表明:当 ASI 为 1.0 时,假人头部 与侧门发生了碰撞,其 HIC 值已超过 200,并得出结论:对于护栏的侧面碰撞, HPC 值为 1000 的评判标准不适合用于护栏的评价[30]。Shojaati,Bmst 等人[34]通过 九次实车碰撞试验,研究了 ASI 和 HIC 的关系。笔者对上述文献的实车试验数据 运用 MATLAB 软件 cftool 工具进行拟合计算,得到 HPC 与 ASI 的回归模型如(式 2.8),其关系曲线如图 2.3 所示。 1.235 13 16.4752.43 2.468 10ASI ASIHPC e e 式(2.8) 式中,ASI——乘员加速度伤害指标; HPC——乘员头部性能指标。 图 2.3 ASI 和 HPC 关系图 Fig.2.3 Relationship between ASI and HPC 决定系数 R2 是判断回归模型拟合程度优劣最常用的数量指标。该值越大,模 型拟合程度越高。经计算本回归模型的决定系数 R2=0.9636,笔者认为本模型拟合 优度较好。 23 表 2.9 ASI 与 HPC 转换表 Tab.2.9 Transition from ASI to HPC 等级 ASI HPC ASI-A ≤1.0 ≤180.27 ASI-B 1.0<ASI≤1.4 180.27<HPC≤295.45 ASI-C 1.4<ASI≤1.9 295.45<HPC≤557.45 根据式(2.8),按照欧盟 EN1317 乘员安全评价标准的划分,计算得出相应的 HIC 值如上表 2.9 所示,ASI-C 级已经属于高危险情况。因实车试验经费昂贵,获 取的数据量相对较少,无法十分精确地提取二者关系,但从少量的数据中,我们 仍可以看出《实车正面碰撞乘员保护设计规则》(CMVDR294)中,用乘员头部性 能指标 HPC 限值来评价车辆与护栏碰撞中乘员的损伤有点过于宽松,因此,在护 栏碰撞安全评价中,假人头部性能指标 HPC 由原来的 1000 降至 557.45 更为合适。 2.4 本章小结 本章简要地介绍了各国防撞护栏试验方法及安全评价标准;概括和分析了国内 外护栏安全性能主要评价指;最后认为将我国《高速公路护栏安全性能评价标准》 中乘员安全评价指标之乘员头部性能指标值由 1000 降至 557.45 更为合适。 第三章 双条半刚性护栏结构设计 3.1 汽车与护栏碰撞机理 汽车与护栏的碰撞是一个十分复杂的过程。护栏的结构形式、材料、护栏板 与立柱的连接、车辆与护栏板之间的摩擦等诸多因素对事故车辆的碰撞行为均有 显著的影响。在车辆与护栏碰撞过程中,车辆在水平面上所受到的作用力包括: 与护栏的摩擦力、与地面的摩擦力,二者可分解为横向作用力和纵向作用力,如 图 3.1 所示;护栏水平面所受作用力为:土壤的约束力、与车辆的摩擦力和车辆惯 性引起的压力,如图 3.2 所示[35]。 24 图 3.1 汽车受力分解图 图 3.2 护栏受力分解图 Fig.3.1 Thrust decomposition of vehicle Fig.3.2 Thrust decomposition of guardrail 对于车辆,横向作用力垂直于护栏板纵平面,使碰撞车辆沿顺时针旋转;纵 向作用力平行于护栏板纵平面,使车辆沿逆时针旋转。横向作用力和纵向作用力 共同决定了车辆碰撞时的减速行为和转向行为。如果横向力引起的力矩大于纵向 力产生的力矩,那么事故车辆将顺时针转向靠近护栏,车辆的运动轨迹得到校正; 反之事故车辆将会出现横向打转或者翻滚等不良后果[9]。良好的护栏结构应具备 吸收碰撞能量和校正车辆运动轨迹的功能,以确保车辆和乘员的安全,降低事故 的损伤程度。 对于护栏,波形护栏板、防阻块、立柱各部件一起承受来自车辆的碰撞力和土 壤的约束力,以吸收绝大部分的碰撞能量。其中波形护栏板主要承受拉力,横向 方向发生弯曲变形,以较高强度抵抗车辆的冲撞,防止车辆冲出道路,纵向方向 发生拉伸变形,以较好的连续性校正车辆的运动方向,竖直方向发生扩张变形, 波纹的逐步展开较好的吸收碰撞能量;防阻块在传递护栏板压力的同时,自身发 生变形吸收部分碰撞能量;而立柱则主要承受弯矩,起着支撑系统完整性的作用。 护栏结构中最为重要的组成部分是波形护栏板,它的波纹越深,断面的可变形量 越大,吸收能量越多。与此同时,波形护栏板的波纹越深,车辆与护栏的接触面 积便越小,两者之间的摩擦力也会越小,即车辆受到的纵向作用力减小了,有利 于车辆运行轨迹的校正[36][37]。 3.2 车辆碰撞防撞护栏后引发骑跨、下钻事故的分析 车辆与护栏发生碰撞后,若车辆发生下钻、骑跨、翻车等现象时,车内乘员 的安全无法保障。因此诸如此类现象是不允许发生的[33]。本文着重考虑车辆下钻 和骑跨事故类型。 3.2.1 骑跨事故分析 车辆碰撞护栏时产生的骑跨运动主要受汽车保险杠下边缘和护栏横梁中心线 高度差的影响,并和汽车运动情况有直接关系。由文献[2]得知,车辆的保险杠高度 是确定护栏设置高度的一个关键控制因素,充分考虑这一因素后,就不大可能发 生越出护栏的事故。为此,我们提出了骑跨事故的数学模型,以重点讨论汽车保 险杠下边缘和护栏横梁中心线高度差对临界骑跨时速度的影响。 ①基本假设 1)碰撞过程中,车辆不发生变形,车辆质心相对于原车几何尺寸保持不变; 2)从车辆碰撞护栏起到碰撞终止,车辆运动方向忽略不计; 25 3)护栏板在横向方向允许发生变形,而竖直方向变形忽略不计; 4)车辆碰撞点在地面上投影点的上升高度与车辆保险杠下边缘上升高度一致; 5)车辆质心处于车辆纵轴线上,并在车辆后轮与碰撞点在车顶上的投影点的 对角线上; 6)车辆与护栏、车轮与道路之间的摩擦力忽略不计算。 ②数学模型的建立 车辆以一定的初速度与护栏发生碰撞后,整个系统的碰撞能量一部分被护栏、 车辆自身变形吸收了,另一部分则克服车辆骑跨于护栏过程中质心上升引起的重 力做功。碰撞系统总能量减去护栏和车辆自身变形吸收的能量之后,如果剩下的 能量大于克服车辆质心上升重力所做的功,车辆则会因拥有多余的动能驱使车辆 继续前行而发生骑跨事故;小于时则不会发生,而当它们相等时,将出现骑跨现 象的一个临界情况。根据此基本原理,可建立车辆碰撞护栏时车辆的骑跨数学模 型。 车辆碰撞护栏发生骑跨现象的原理图如图 3.3 所示,其中图 3.3(a)表示车辆 与护栏发生碰撞之前的位置关系图,图 3.3(b)表示的是车辆碰撞护栏后骑跨在 护栏上的位置关系图。假定车辆碰撞前后保险杠上升高度为△H,保险杠下边缘与 护栏横梁中心线高度差为△h,则根据碰撞前后能量守恒定理,有: (a)碰撞前 (b)发生骑跨临界 图 3.3 事故原理图 Fig.3.3 The principle of accident 2 0 1 sin sin2 g B V Om v mg h E E E 式(3.1) 式中, m ——车辆质量( kg ); 0v ——车辆初始速度( /m s ); ——碰撞角度(°); g ——重力加速度( 2/m s ); 26 gh ——车辆质心上升高度( m ); BE ——护栏变形吸收能量( J ); VE ——车辆变形吸收能量( J ); OE ——其他损失能量( J )。 由于车辆碰撞过程中,保险杠上升的高度△H 并不是整车质心上升的高度 gh ,因此需要通过几何关系的计算,得出车辆质心上升高度 gh ,以寻求保险杠 上升高度△H 与碰撞初速度 0v 的关系,进而得到保险杠下边缘与护栏横梁中心线 高度差△h 与车辆碰撞初速度 0v 的关系。 车辆的基本几何尺寸如图 3.4 所示,简化模型如图 3.5 所示。当车辆与护栏碰 撞时,保险杠上升过程可简化为 PN 段绕着点 O(代表车辆后右轮中心)旋转角度 β,点 M、N、P、Q 旋转至点 M’、N’、P’、Q’,且 N 点上升高度为△H,进而引 起质点 Q 高度由原来的 hg 增加到 hg’。 图 3.4 车辆几何尺寸 Fig.3.4 Dimension of Vehicle 图 3.5 车辆简化模型 27 Fig.3.5 Simplified model of vehicle 图 3.6 车辆上升前后位置关系图 Fig.3.6 Vehicl Position change after being lifted 图中,TW——轮距; B——车宽; L——车长; H——车高; b——车辆质心至后轴的距离; c——车辆质心至距前保险杠的距离; hg——质心高度。 根据图 3.5 和图 3.6 中的几何关系,有: 2 21' ( ) [ ( )]2 WON ON b c T B 式(3.2) 2 2 'arctan( ) arctan( )' 1( ) [ ( )]2 W PN H ON b c T B 式(3.3) 2 2 ' ''arcsin( ) arcsin( )' 1( ) [ ( )]2 W N N H ON b c T B 式(3.4) ' sin ghOQ 式(3.5) 则,车辆碰撞护栏后的质心高度为: ' ' sin( )gh OQ 式(3.6) 28 所以,车辆碰撞护栏后其质心上升高度为: 'g g gh h h 式(3.7) 将式(3.2)至式(3.6)带入式(3.7)得,上式得: 2 2 2 2 2 2 sin arctan( ) arcsin( ) 1 1( ) [ ( )] ( ) [ ( )]2 2 1 sin arctan( ) 1( ) [ ( )]2 W W g g W H H b c T B b c T B h h H b c T B 式(3.8) 将式(3.8)带入式(3.1),经过整理,得前保险杠上升高度△H 为: 2 0 1 sin sin2sin arcsin 1 sin(arctan ) arctan B V O g m v E E E H HH K mg h K K 式(3.9) 因此,对于车辆碰撞护栏发生骑跨事故,我们可以通过车辆前保险杠上升的高 度△H,得到保险杠下边缘与护栏横梁中心线高度差△h 与临界骑跨速度 0v 的关系 式: 2 0 1 sin sin2sin arcsin 1 sin(arctan ) arctan2 B V O b g m v E E EB H Hh K mg h K K 式(3.10) 式中: bB ——波形护栏板宽度,A 级高速公路双波半刚性防撞护栏取 310mm; K ——车辆结构系数,即: 2 21( ) [ ( )]2 WK b c T B 式(3.11) 为了便于计算,车辆结构系数可取近似值 2 2( ) ( )K L B 根据高速公路交通工程及沿线设施设计通用规范(JTG D80-2006),A 级波形半 刚性护栏吸收能量 BE 为 160kJ,碰撞角度取 20°,取 : : 100:100:1B V OE E E ,以某 车型为例,主要参数如下表 3.1 所示。 表 3.1 某车型的主要参数 Tab.3.1 Main parameters of a vehicle 质量 m/(kg) 车长 L/(m) 车宽 B/(m) 质心至后轴的距离 b/(m) 1500 5.025 1.84 1.82 29 车高 H/(m) 轮距 TW/(m) 质心高度 hg/(m) 质心至距前保险杠的距离 c/(m) 1.47 1.566 0.568 3.82 利用 MATLAB 软件绘制出保险杠下边缘与护栏横梁中心线高度差△h 与临界 骑跨速度 v0 关系的趋势图(如图 3.7)。从图可知,保险杠下边缘与护栏横梁中心 高度差随着临界骑跨速度的增加而逐渐降低。图中蓝色实线取的是 K 值,红色虚 线取 K 的近似值,两曲线趋势十分接近,因此,用 K 的近似值代替 K 值是较为可 靠的。从图 3.8 中可以得到,当车辆初始速度为 22.2m/s 时,车辆前保险杠下边缘 不得高于护栏横梁中心线 83.78mm,否则会发生骑跨事故。由于现在各种车型结 构悬殊较大,而且各地高速公路各种车型所占比例也不尽相同,因此,通过车辆 的结构来确定护栏的类型和基本结构参数需要根据高速公路车型所占比例和大多 数车型的实际情况而定。 0 5 10 15 20 25-10 0 10 20 30 40 50 车辆初速度 保 险 杠 下 边 缘 与 护 栏 横 梁 中 心 线 高 度 差 K K 图 3.7 高度差△h 与临界骑跨速度 v0 关系 Fig.3.7 Relationship between △h and v0 22.19 22.195 22.2 22.205 22.21 22.215 22.22 22.225 0 0.02 0.04 0.06 0.08 0.1 0.12 0.14 0.16 (m/s) h ( m ) 图 3.8 放大后的高度差△h 与临界骑跨速度 v0 关系 Fig.3.8 Relationship between △h and v0 after magnify 30 3.2.2 下钻事故分析 随着现代小轿车逐步的微型化发展,发动机盖为了满足流线型设计而变得更 低,此类车型在和护栏发生碰撞时,很容易钻入护栏横梁之下,造成严重的人员 伤亡和财产损失。发生车辆下钻护栏事故的主要原因在于汽车的发动机盖高度与 护栏横梁下边缘的高度过于接近( 2 1h h ),甚至汽车的发动机盖高度低于护栏横 梁下边缘高度( 2 1h h ),如图 3.9 所示。车辆的前车盖高度是确定护栏设置高度 的关键控制因素,充分考虑这一因素后,就不大可能发生钻撞护栏的事故[2]。为了 防止此类事故的发生,规范中提出护栏的接触点在垂直方向不应少于 3 英寸 (76.4mm),即护栏横梁安装高度 h0 不得高于汽车发动机盖高度 h2 的 78.6mm。 图 3.9 车辆下钻护栏模型图 Fig.3.9 Vehicle running into guardrail 3.3 设计思想 3.3.1 设计目的 目前世界上生产的汽车从大吨位的重型汽车到很小的微型汽车,其质量相差 非常悬殊,车辆外形变化很大。现代的小轿车有向微型化发展的趋势,其质量变 得越来越轻,为了减少空气阻力,前车盖更符合流线型而变低,这种车辆在与护 栏相碰时,很容易转入护栏的横梁下面而造成严重的后果。另一种情况是车辆的 吨位越来越大,也就是车辆日趋大型化和重型化。这种大型车在与护栏碰撞时, 可能产生跳跃问题[2] [38]。 在与 W 型波形护栏相碰时,由于车辆的保险杠碰撞波形梁护栏的横梁顶部而 可能使其拧扭成斜面。这种情况尤其在碰撞角度很大、速度很高时危险性更大。 一旦出现这种情况,就有可能使保险杠向下往后倾斜,汽车在冲撞力的作用下很 容易滑上护栏的斜面,从而发生跃出护栏的事故[2]。 31 上述两种情况对护栏的功能设计带来了矛盾,也增加了确定护栏结构形式的 难度,这是世界各国研究人员至今仍在不断探索护栏的原因之一。可见,研发一 种可以防御多种车型的新型护栏结构势在必行[9]。 因此,为了适应当今汽车微型化、大型化和重型化所带来的巨大变化,扩大 护栏的防撞车型范围,本文研制了双条半刚性波形护栏,以解决汽车微型化造成 的车辆下钻护栏问题和汽车大型化、重型化造成的车辆骑跨护栏的问题。 3.3.2 结构形式 护栏板在整个碰撞过程中,起到了吸收碰撞能量和导向的作用,是最为重要的 组成部分。本文研究的双条半刚性护栏是基于原有波形护栏的基本结构,改进了 原护栏板的安装高度,并在其下方增设了一条半刚性护栏,通过下防阻块与立柱 连接,与上护栏板和上防阻块等部件构成一体,共同抵抗车辆的碰撞。新型护栏 的结构形式如图 3.10 所示。在安装过程中,上护栏板伸出量比下护栏板伸出量略 大,以预防车辆与下护栏板过早的接触而引起翻车;合理设置上、下护栏板的安 装高度是双条半刚性护栏安全与否的关键所在。本文将在后面章节中详细讨论安 装高度问题。 (a)主视图 (b)立体图 图 3.10 双条半刚性护栏结构图 Fig.3.10 Structure of double semi-rigid guardrail 3.3.3 工作原理 本护栏主要由上、下护栏板基本结构形式组成,在碰撞过程中起到吸收能量 和校正车辆行驶方向的作用。护栏中的上、下护栏板部件先后与车辆发生接触碰 撞,上护栏板首先变形吸收碰撞能量,吸收到一定程度时,下护栏板开始与车辆 产生接触,继上护栏板变形并吸收碰撞能量。两者在与不同车体类型冲撞时,侧 重点是有所不同的。 32 上护栏板离地面的间距高于原有护栏板的离地距离,在抵抗大型车和重型车 冲撞时,相对缩短了车辆质心与上护栏板碰撞点的高度差,车辆发生穿越和骑跨 护栏较为困难,从而降低了此类事故发生的风险性; 下护栏板距地面高度低于原有护栏板的离地高度,在受到微型轿车碰撞时,虽 然增加了车辆质心与下护栏碰撞点的高度差,但有上护栏板的防御,发生穿越和 骑跨事故概率十分微小。与此同时,随着轿车的微型发展,保险杠和发动机盖高 度均变得更低,由此设计成了相对高度较低的下护栏板,以缩小下护栏板与发动 机盖之间的高度差,有效预防车辆下钻护栏事故的发生,提高护栏的防撞性能。 3.3.4 变形分析 本文研究的双条半刚性护栏变形包含原有半刚性护栏的基本特性之外,还具备 自身变形特点和变形过程。它的变形主要经历了以下三个过程: 过程一:在车辆即将与护栏发生碰撞时,车辆的保险杠至发动机盖之间的某 部分(视不同车型而定,微型轿车为发动机盖偏下部分、大型和重型车为保险杠 及其偏上部分)先与上半刚性护栏板发生接触,上护栏板发生横向的弯曲变形、 上防阻块发生轻微的挤压变形,此过程为初次吸收碰撞能量。 过程二:随着碰撞的进一步推进,车辆的轮胎上半部分开始与下半刚性护栏 板接触,下护栏板发生横向的弯曲变形、下防阻块发生挤压变形,与此同时,上 护栏板继续发生扩展变形,上防阻块进一步发生挤压变形,此过程为第二次吸收 碰撞能量。 过程三:在上、下护栏板和防阻块吸收大部分碰撞能量之后,立柱开始承受 弯矩,发生弯曲变形吸收车辆剩下的碰撞能量,此过程为第三次吸收碰撞能量。 通过护栏的三次吸能过程,碰撞车辆的绝大部分能量均被吸收,较好的防止了车 辆翻越、骑跨和下钻等严重事故的发生,提高了乘员和车辆的安全性能。 3.3.5 双条半刚性护栏特点 双条半刚性护栏与传统半刚性护栏很大的区别,不但在吸收能量方面、防止意 外事故方面,还是在乘员保护方面均有着很大的优势。本护栏的特点可归纳为以 下几点: ①防撞车型范围的扩大。目前车辆的微型化、大型化和重型化,原有防撞护栏 很难同时满足这些车型的碰撞要求,而该护栏则兼顾了车辆“两极”发展的特点,既 可以保护微型车,又可在一定程度上保障大型车和重型车的行车安全。 ②吸能区域的变得更宽。该护栏通过上、下双条半刚性护栏基本结构形式,将 原有护栏一分为二,通过上、下两个部分先后吸收碰撞能量,重组了吸能区域, 扩大了碰撞过程中护栏吸能区域和吸收能量的能力,发挥出独特的防撞作用。 ③更为有效的防止多种事故形式的发生,尤其是防止微型轿车的下钻护栏事 33 故、大型车和重型车的穿越、翻越和骑跨事故。 1)针对微型轿车,根据车体流线型设计降低了车辆的碰撞区域,该护栏也随 之满足此类车型的碰撞需要,着重体现下半刚性护栏板的防撞功能,增设的下半 刚性护栏板,可防止微型轿车下钻护栏事故的发生; 2)针对大型和重型车,与护栏发生碰撞时碰撞部位较高,若护栏的高度不够, 车辆很容易就冲出护栏,与护栏外的实体发生二次碰撞,造成严重的交通事故。 为此,本护栏为了兼顾这部分车型的碰撞情况,着重体现在上半刚性护栏板的防 撞功能,提高上半刚性护栏的安装高度,有效遏止穿越、翻越和骑跨事故的发生。 ④防止车辆发生阻绊效应。本设计护栏中的下护栏板结构,从空间上阻隔了车 轮与护栏立柱的接触,即使在护栏变形较为严重的情况下,车轮也很难与立柱发 生接触碰撞,从根源上,避免了车辆与护栏发生阻绊效应。 3.4 待求参数分析 护栏板是护栏系统中的核心部件,它性能的好坏直接关系到整个护栏的安全 性能。由此,本文着重对护栏板进行分析研究,初步确定上、下护栏板的基本参 数,从而为后面章节的仿真分析奠定基础。 首先,根据第二节的事故分析可知,防止车辆发生穿越、骑跨、下钻等事故最 为关键的因素就是护栏板的安装高度,而本文研究的护栏板采用的是双条护栏板, 安装高度与原有护栏的情况大不相同。上护栏板因防止大型车和重型车发生骑跨 护栏事件而提高其安装高度,但与此同时,也相应地增加了微型轿车下钻护栏的 风险性;下护栏板因防止微型车发生下钻护栏事故而降低其安装高度,但也相对 地增加了大型车和重型车的车轮碾压下护栏板,抬高前车头,发生骑跨甚至冲出 上护栏板的可能性。可见,双条半刚性护栏板各自的安装高度(或其间距)是待 求尺寸中最为重要的参数之一。 其二,上、下护栏板在碰撞过程中先后与车辆的接触顺序对碰撞形态也有较大 影响。由力学平衡原理,车辆若与下护栏板先发生接触碰撞,平衡点会变低而更 容易引发车辆侧翻事故。因此,设计为车辆先与上护栏板发生碰撞,然后再和下 护栏板发生接触,二者的接触间隔需要加以合理的控制,否则也将无法达到预期 的碰撞效果。可见,上、下护栏板的伸出量差值亦是待求参数之一。 其三,立柱是整个护栏系统的支撑部件,立柱跨度(即每两个立柱的间距)的 大小对护栏板的支撑强弱也有很大关系,防撞效果也受其影响,因此,立柱跨度 仍是待求的重要参数之一。 上述分析得知,主要的待求参数包括:上护栏板安装高度 H,下护栏板安装高 度 h,上、下护栏板伸出量差值δ以及立柱跨度 L,如图 3.11 所示。 34 图 3.11 双条半刚性护栏待求参数图 Fig.3.11 The unknown parameters of double semi-rigid guardrail 3.5 参数设计流程 为了确保车辆与护栏发生碰撞事故过程中的乘员安全和行车安全,护栏板基本 结构参数的确定显得尤为重要。 35 图 3.12 参数设计流程图 Fig.3.12 Process of parameters design 首先,对车辆与护栏碰撞事故加以分析和归类,对于不同碰撞事故,采取不同 的设计方案。本文主要研究车辆骑跨护栏事故模型和分析下钻事故发生机理,分 别得到两种主要碰撞事故对应的护栏板安装高度,以确定上、下护栏板安装高度 取值范围;其次,设定上、下护栏板伸出量差值δ和立柱跨度的取值范围;最后, 通过均匀设计对上述四个参数进行优化,确定能满足护栏评价安全指标的优化值。 其参数设计流程如图 3.12 所示。 3.6 参数范围的确定 3.6.1 上护栏板安装高度 H 范围的确定 该护栏板主要目的在于有效防止大型车辆与护栏发生碰撞时产生骑跨等严重 的交通事故,并保证微型轿车不发生下钻事故。微型轿车发生下钻事故的最低临 界高度为上护栏板安装高度的上限值;大型车辆发生骑跨事故的最高临界高度为 上护栏板安装高度的下限值,满足前述条件,才能达到护栏的最初设计要求。 ①上护栏板安装高度上限值的确定 36 在所有车型当中,流线型较好的轿车因前车盖较低,在与护栏发生碰撞时更易 发生比较严重的下钻护栏事故。为此,上护栏板安装高度上限值必须满足此类车 型不发生下钻事故的设计条件。其设计方法基于车辆下钻事故发生机理,收集并 统计高速公路部分轿车的前车盖高度,根据文献[2]中提到护栏接触点在垂直方向不 应少于 3 英寸(76.4mm),即护栏横梁安装高度不得高于汽车发动机盖高度的 78.6mm 的设计方法来确定。各种轿车对应的上护栏安装高度如表 3.2 所示。 表 3.2 轿车对应的上护栏安装高度上限值 Tab.3.2 Upper guardrail’ max height corresponding to different cars 序号 车 型 上护栏板上限值 Hmax 1 北京现代-悦动 888.2708 2 进口雪佛兰-Spark 斯帕可 800.0762 3 一汽丰田-锐志 904.0766 4 一汽大众-速腾 923.6714 5 华晨宝马-宝马 3 系 770.7895 6 一汽奥迪-奥迪 A4L 874.0774 7 长安福特-嘉年华 805.0191 8 neon-0.7 697.52 9 东风本田-思域 2009 款 1.8 LXi 847.9283 10 一汽大众-大众 CC 792.0955 11 长安轿车-志翔 862.7704 12 进口雷克萨斯-雷克萨斯 GS 843.589 13 广汽本田-雅阁 903.0594 14 长安福特-福特 S-MAX 834.5547 15 长安沃尔沃-沃尔沃 S40 877.4109 按照 95%的车辆不发生下钻事故的要求,对上表数据进行计算和整化,上护栏 板安装最高临界高度 Hmax 取为 770mm。 ②上护栏板安装高度下限值的确定 上护栏板安装高度下限值的设计基于前面建立的骑跨事故数学模型(详见第三 章第二节),分析当车辆接近临界骑跨速度时的车辆保险杠下边缘与护栏横梁中心 线高度差△h,再根据车辆自身保险杠的高度,确定上护栏板的安装高度。 在采用骑跨事故数学模型之前,针对我国高速公路上的大型车辆的车身参数进 行统计,车型主要以大型车和重型车为主,根据高速公路护栏安全性能评价标准 (JTG/T F83-01-2004)的试验条件:小轿车碰撞速度为 100 km/h 和碰撞角度 20°、 大客车碰撞速度为 80 km/h 和碰撞角度 20°、大货车碰撞速度为 60 km/h 和碰撞角 度 20°。统一起见,碰撞速度均为 80 km/h、碰撞角度 20°。经过计算,得到各车型 37 对应护栏的安装高度,如表 3.3 所示。 表 3.3 大型/重型车对应的上护栏安装高度下限值 Tab.3.3 Upper guardrail’ max height corresponding to different large-scale/heavy vehicles 序号 车 型 上护栏板下限值 Hmin 1 CA1429P4K2L11T6 558.0392 2 CA5175CLXYP1K2L10T3A706X2 604.986 3 CA1258P4K2L5T1 654.6921 4 解放牌 CA1127L5A 506.434 5 解放牌 CA1359P4K2L11T610X4 657.339 6 解放牌 CA1250P4K2L11T36X2 688.644 7 春兰牌 NCL1209DP 柴油载货汽车 703.3069 8 解放牌 CA1160P1K2LA70 平头 4X2 载货汽车 649.6149 9 解放牌 CA1320P4K2L11T6A70 平头浮轮载货汽车 723.0726 10 解放牌 CA1241P2K14T 平头 6X6 载货汽车 637.3188 11 大通牌 SH1250 平头驾驶室载货汽车 707.6563 12 解放牌 CA1255P2K2E3L3T1A92 平头载货汽车 717.7735 13 解放牌 CA1255P11K2L7T1A91 平头长轴距载货汽车 682.4149 14 东风本田-本田 CR-V 579.1031 15 悍马 H3x 704.26 按照 95%的车辆不发生骑跨事故的要求,对上表数据进行计算和整化,上护栏 板安装最低临界高度值 Hmin 取为 720mm。 因此,上护栏板的安装高度 H 取值范围为 720mm~770mm。 3.6.2 下护栏板安装高度 h 范围的确定 该护栏板主要目的是防止微型轿车与护栏发生碰撞时产生骑跨事故。微型轿 车发生骑跨事故的最高临界高度作为下护栏板安装高度的下限值,而下护栏板安 装高度的上限值需根据上护栏板的安装高度而定,满足低于上护栏板的安装高度 即可。 ①下护栏板安装高度上限值的确定 根据上护栏板安装的最低临界高度 720mm,上护栏板宽度 310mm 和下护栏板 半个单波宽度 96mm,下护栏板安装的最高临界高度计算如下: max 720 310/ 2 96( ) 469( ) 470( )h mm mm mm 对计算结果整化,下护栏板安装的最高临界高度 hmax 取为 470mm。 ②下护栏板安装高度下限值的确定 下护栏板安装高度下限值的确定与上护栏板安装高度下限值的确定基本类似, 设计对象由前面的大型/重型车换为微型轿车,仍按照碰撞速度 80km/h 和碰撞角度 38 20°的碰撞条件,经过计算,得到各车型对应护栏的安装高度,如表 3.4 所示。 表 3.4 轿车对应的下护栏板安装高度下限值 Tab.3.4 Lower guardrail’ min height corresponding to different cars 序号 车 型 下护栏板下限值 1 北京现代-悦动 354.8577 2 进口雪佛兰-Spark 斯帕可 313.5252 3 一汽丰田-锐志 398.14 4 一汽大众-速腾 412.4161 5 华晨宝马-宝马 3 系 317.0887 5 一汽奥迪-奥迪 A4L 442.2141 7 长安福特-嘉年华 385.0081 8 neon-0.7 318.468 9 东风本田-思域 2009 款 1.8 LXi 424.9022 10 一汽大众-大众 CC 306.2396 11 长安轿车-志翔 356.8433 12 进口雷克萨斯-雷克萨斯 GS 342.3074 13 广汽本田-雅阁 433.254 14 长安福特-福特 S-MAX 240.666 15 长安沃尔沃-沃尔沃 S40 422.3141 按照 95%的车辆不发生骑跨事故的要求,对上表数据进行计算和整化,下护栏 板安装的最低临界高度值 hmin 取为 440mm。 因此,下护栏板的安装高度 h 取值范围为 440mm~470mm。 3.6.3 护栏板伸出量差值δ和立柱跨度 L 范围的确定 ①护栏板伸出量差值δ范围的确定 由于车辆碰撞护栏后将导致立柱发生变形和后倾,而立柱的变形和后倾将会 引起下护栏板相对于上护栏板伸出,导致车辆和护栏板接触点由上护栏板移动到 下护栏板,接触点的下降有可能造成车辆的侧翻运动。为考察上、下护栏板伸出 量差值对车辆运动状态的影响,设定护栏板伸出量差值最大值约为防阻块宽度的 一半(约为 90mm)。因此,护栏板伸出量差值δ范围为 0≤δ≤90mm。 ②立柱跨度 L 范围的确定 一般地,波形护栏的立柱跨度为 2000mm、护栏板长度为 4000mm。因此,本 文的立柱跨度 L 范围假定为 2000mm~4000mm。 3.7 参数的优化设计 优化设计是用数学规划理论来求解最优设计方案,非线性约束优化方法有罚函 39 数法、复合形法、网络法、可行方向法等[39][40]。在使用这些优化方法之前均要明 确列出目标函数和计算较为复杂,然而车辆与护栏碰撞属于大变形并且非线性, 目标函数的建立尚较困难。综合考虑,本论文采用均匀设计的试验设计方法来获 取目标函数,并运用 MATLAB 的 fmincon 函数进行非线性多变量约束最优化求解, 较为方便的得到护栏参数的最优解。 3.7.1 均匀设计原理[41][42][43] 均匀设计(Uniform Design)是基于试验点在整个试验范围内均匀散布的从均匀 性角度出发的一种试验设计方法, 是数论方法中的“伪蒙特卡罗方法”的一个应用, 由方开泰和王元两位数学家于 1978 年创立。 均匀设计原理是数论中的一致分布理论。它只考虑试验点在试验范围内均匀散 布,挑选试验代表点的出发点是“均匀分散”,可以保证试验点具有均匀分布的统计 特性,还可使每个因素的每个水平做一次且仅做一次试验,任两个因素的试验点 点在平面的格子点上,每行每列有且仅有一个试验点。它着重在试验范围内考虑 试验点均匀散布以求通过最少的试验来获得最多的信息,因而其试验次数比正交 设计明显的减少,使均匀设计特别适合于多因素多水平的试验和系统模型完全未 知的情况。均匀设计已成为一种主要的试验设计方法,包括四个优点:a.充满空间, 均匀设计在试验区域内产生具有很强代表性的试验点;b.稳健性,均匀设计是 沿用回归设计思想,对模型没有要求很强的假定,对模型的变化有一定的稳健 性;c.多水平,均匀设计是所有试验中一个因素能安排水平最多的试验设计;d. 试验次数大大减少等。 一般地,均匀设计的操作过程: ①明确试验目的,确定试验指标。 ②选择试验因素。根据专业知识和实际经验进行试验因素的选择,一般选择 对试验指标影响较大的因素进行试验; ③确定因素水平。根据试验条件和以往的实践经验,首先确定各因素的取值 范围,然后在此范围内设置适当的水平; ④选择均匀设计表, 排布因素水平。根据因素数、水平数来选择合适的均匀 设计表进行因素水平数据排布; ⑤明确试验方案,进行试验操作; ⑥试验结果分析。 3.7.2 均匀设计试验 ①试验目的 基于上述均匀设计理论,选取护栏安全评价指标中的车辆碰撞最小加速度和护 栏最小变形量做为综合优化指标,建立二次多项式模型,研究上护栏板安装高度 H、 40 下护栏板安装高度 h、上下护栏板伸出量差值δ和立柱跨度 L 的最佳匹配值。 ②选取试验因素 在众多影响车辆碰撞加速度和护栏变形量因素中,新型护栏中的上护栏板安装 高度 H 和下护栏板安装高度 h 对车辆碰撞加速度有着较大的影响, 选取 H 和 h 为试验因素 1,2;与此同时,上、下护栏板伸出量差值δ和立柱跨度 L 对护栏的变 形量有重要影响,选取δ和 L 作为试验因素 3,4。 表 3.5 试验因素及其水平表 Tab.3.5 Test factor and factor level 试验因素 因素水平 因子 1 (H) 因子 2 (h) 因子 3 (δ) 因子 4 (L) N1 720 440 0 2.0E+03 N2 723.57 442.14 6.4286 2.14E+03 N3 727.14 444.29 12.857 2.29E+03 N4 730.71 446.43 19.286 2.43E+03 N5 734.29 448.57 25.714 2.57E+03 N6 737.86 450.71 32.143 2.71E+03 N7 741.43 452.86 38.571 2.86E+03 N8 745 455 45 3.00E+03 N9 748.57 457.14 51.429 3.14E+03 N10 752.14 459.29 57.857 3.29E+03 N11 755.71 461.43 64.286 3.43E+03 N12 759.29 463.57 70.714 3.57E+03 N13 762.86 465.71 77.143 3.71E+03 N14 766.43 467.86 83.571 3.86E+03 N15 770 470 90 4.00E+03 ③确定因素水平 前面一节分析了各试验因素的取值范围,综合考虑实际情况,各因素水平选取 15 个,其具体值如表 3.5。 ④选择均匀设计表 本文运用 DPS(Data Processing System)数据处理系统计算生成均匀设计表。 DPS 数据处理系统是由浙江大学唐启义等人开发的通用多功能数理统计和数学模 型处理平台,它将数值计算、试验设计、统计分析、模型模拟和画线制表等功能 为一体,功能十分强大。基于该平台,选取实验因素为 4,因素水平为 15,生成 的均匀设计表如 3.6 所示。 表 3.6 均匀设计方案 Tab.3.6 Uniform design scheme 41 试验因素 因素水平 x1 x2 x3 x4 N1 9 8 10 15 N2 5 13 7 14 N3 14 10 12 10 N4 12 2 6 13 N5 3 12 9 1 N6 8 3 3 2 N7 1 9 5 6 N8 13 14 4 4 N9 4 6 1 9 N10 6 1 11 5 N11 15 5 8 7 N12 2 4 13 12 N13 10 11 2 11 N14 7 15 14 8 N15 11 7 15 3 表 3.7 试验方案 Tab.3.7 Test scheme 试验因素 因素水平 x1 x2 x3 x4 N1 748.5714 455 57.8571 4.00E+03 N2 734.2857 465.7143 38.5714 3.86E+03 N3 766.4286 459.2857 70.7143 3.29E+03 N4 759.2857 442.1429 32.1429 3.71E+03 N5 727.1429 463.5714 51.4286 2000 N6 745 444.2857 12.8571 2.14E+03 N7 720 457.1429 25.7143 2.71E+03 N8 762.8571 467.8571 19.2857 2.43E+03 N9 730.7143 450.7143 0 3.14E+03 N10 737.8571 440 64.2857 2.57E+03 N11 770 448.5714 45 2.86E+03 N12 723.5714 446.4286 77.1429 3.57E+03 N13 752.1429 461.4286 6.4286 3.43E+03 N14 741.4286 470 83.5714 3.00E+03 N15 755.7143 452.8571 90 2.29E+03 ⑤试验方案 根据前面的试验因素及水平表 3.5 和均匀设计方案(表 3.6)确定本试验方案, 如表 3.7 所示。 根据试验方案,采用 CATIA、HyperMesh 软件先后建立几何模型和有限元模 42 型,其仿真模型如下:圆管立柱、防阻块和上、下波形护栏的组合结构。圆管立 柱的下端在地下 1100mm 处受到六自由度约束,以模拟实际土壤对立柱的约束效 果。在上、下护栏板中心高度处受到速度为 7600mm/s(垂直于护栏板方向)的钢 块正面碰撞。其中钢块尺寸为 580mm×580mm×580mm,质量约为 1.5t;护栏的密 度 Pho=7.860e-09t/mm3 、弹性模量 E=200GPa、泊松比 NU=0.27、屈服应力为 310MPa[19] , 单 元 类 型 为 Belytschko-Tsay 类 型 , 接 触 类 型 采 用 AUTOMATIC_SINGLE_SURFACE。按照试验方案 1 构建的碰撞模型如图 3.13 所 示,得到该因素水平下护栏的应力云图(见图 3.14),调出车辆的加速度曲线(见 图 3.15)和护栏变形曲线(见图 3.16),并从曲线图中得到车辆的最大加速度值为 106410mm/s2,约为 10.86g(g 为重力加速度),护栏最大变形量 929.81mm。 图 3.13 试验方案 1 碰撞模型 Fig.3.13 Crash model (scheme 1st) 图 3.14 试验方案 1 护栏应力云图 Fig.3.14 Von mise stress of guardrail(scheme 1st) 43 图 3.15 车辆最大加速度曲线 图 3.16 护栏最大变形曲线 Fig.3.15 Max acceleration curve of vehicle Fig.3.16 Max deformation curve of guardrail 同理,按照剩下 14 组试验方案,调整试验因素数值,获得各因素水平下车辆 的最大加速度值和护栏最大变形量,如表 3.8 所示。 表 3.8 试验结果 Tab.3.8 Test result 试验因素 因素水平 x1 x2 x3 x4 车辆最大 加速度 a 护栏最大 变形量 Z N1 748.5714 455 57.8571 4.00E+03 106410 929.81 N2 734.2857 465.7143 38.5714 3.86E+03 124930 870.26 N3 766.4286 459.2857 70.7143 3.29E+03 67107 905.66 N4 759.2857 442.1429 32.1429 3.71E+03 152440 866.15 N5 727.1429 463.5714 51.4286 2.0 E+03 139580 649.66 N6 745 444.2857 12.8571 2.14E+03 124120 721.81 N7 720 457.1429 25.7143 2.71E+03 93893 834.98 N8 762.8571 467.8571 19.2857 2.43E+03 90974 775.8 N9 730.7143 450.7143 0 3.14E+03 103550 810.04 N10 737.8571 440 64.2857 2.57E+03 98138 770.25 N11 770 448.5714 45 2.86E+03 95089 855.91 N12 723.5714 446.4286 77.1429 3.57E+03 117890 906.29 N13 752.1429 461.4286 6.4286 3.43E+03 85763 954.95 N14 741.4286 470 83.5714 3.00E+03 103970 844.63 N15 755.7143 452.8571 90 2.29E+03 112170 758.14 ⑥试验结果分析 运用 DPS 数据处理系统对上表数据进行二次多项式回归分析,得到车辆碰撞 加速度 a 与上护栏板安装高度 H、下护栏板安装高度 h、上下护栏板伸出量差值δ 和立柱跨度 L 的回归方程模型: 44 2 2 2 2 53248241.42 59805.3 134344.4 3504.54 39.81 66.41 218.2h 21.22 0.067 85.45 0.85 0.17 2.92 0.48 0.16 a H h L H L H h H H L h h L L 式(3.12) 回归模型的相关系数 R=0.99,决定系数 R2≈1,因此可以判定模型拟合十分理 想,当 H=747.96mm、h=457.19mm、δ=47.44mm、L=2949.25mm 时,车辆最大加 速度处的加速度最小,即为 29746.82mm/s2。 护栏板变形量与上护栏板安装高度 H、下护栏板安装高度 h、上下护栏板伸出 量差值δ和立柱跨度 L 的回归方程模型: 2 2 2 2 4 2 2 3 4 3 -266585.48 445.04 448.62 130.12 3.02 8.81 10 0.11 0.11 1.26 10 0.72 3.77 10 4.32 10 0.41 8.75 10 6.21 10 z H h L H h L H h H H L h h L L 式(3.13) 在对护栏变形量 Z 与上护栏板安装高度 H、下护栏板安装高度 h、上下护栏板 伸出量差值δ和立柱跨度 L 进行回归时,护栏变形量 Z 有负值出现,为避免此情况 的发生,先对 15 组数据中的 Z 值进行 ln 对数处理,得到的回归方程模型: 3 4 2 4 2 4 2 7 2 4 5 6 4 7 6 ln 352.65 0.63 0.55 0.16 3.07 10 1.3 10 2.4 10 1.4 10 1.7 10 9.9 10 7.4 10 4.98 10 5.56 10 3.4 10 8.49 10 z H h L H h L H h H H L h h L L 式(3.14) 回归模型的相关系数 R=0.99,决定系数 R2≈1,因此可以认为模型拟合十分理 想,当 H=720mm、h=440mm、δ=42.48mm、L=2005mm 时,护栏最大变形处的变 形量最小,lnz=6.011,即 z 为 407.84mm。 从式(3.12)和式(3.13)所得到的上护栏高度 H、下护栏高度 h、上下护栏 伸出量差值δ和立柱跨度 L 值可以看出,车辆加速度和护栏变形量不能同时达到最 佳效果值。因此,需要对各个变量加以优化,保证车辆加速度和护栏变形量在一 定范围内均能达到较好的效果。 3.7.3 数学建模 ①设计变量 通过前面章节的分析,新型护栏的变量确定为:上护栏板安装高度 x1、下护栏 板安装高度 x2、上下护栏板伸出量差值 x3 和立柱跨度 x4。 ②目标函数 车辆碰撞护栏安全评价中,评价指标有车辆最大加速度(无假人时)、护栏最 大变形量和车辆驶出角度等,本文着重对前面两个指标加以研究和分析,根据式 (3.12)和式(3.13),可知它们的目标函数如下所示: 45 1 1 2 3 4 2 2 2 2 1 2 3 4 1 2 1 3 1 4 2 3 2 4 3 4 min ( ) 53248241.42 59805.3 134344.4 3504.54 3 9.81 66.41 218.2x 21.22 0.067 85.45 0.85 0.17 2.92 0.48 0.16 f x x x x x x x x x x x x x x x x x x x x 2 2 2 1 2 3 4 1 2 2 4 2 2 2 3 4 1 2 1 3 3 4 3 1 4 2 3 2 4 3 4 min ( ) -266585.48 445.04 448.62 130.12 3.02 8.8 1 10 0.11 0.11 1.26 10 0.72 3.77 10 4.32 10 0.41 8.75 10 6.21 10 f x x x x x x x x x x x x x x x x x x x x x 不难看出,此优化目标属于多目标优化范畴,论文采用线性加权组合法确定 综合目标函数[44]。 1 ( ) ( ) q i i i f X w f X 式(3.15) 式中, iw ——加权因子( 1,2,...,i q ),是反映各个分目标重要性的一组系数,以 考虑各分目标函数在相对重要程度方面的差异。 ③约束函数 在前面一节中较为详细地分析了各设计变量的取值范围,即为: 1 2 3 4 720 770 440 470 0 90 2000 4000 x x x x ④数学模型 归纳起来,优化的目标函数以及约束函数构成如下数学模型: 2 1 1 2 3 4 1 2 2 2 2 3 4 1 2 1 3 1 4 2 2 3 2 4 3 4 min ( ) 53248241.42 59805.3 134344.4 3504.54 3 9.81 66.41 218.2x 21.22 0.067 85.45 0.85 0.17 2.92 0.48 0.16 m f x x x x x x x x x x x x x x x x x x x x x R 2 2 2 2 1 2 3 4 1 2 2 4 2 2 3 3 4 1 2 1 3 1 4 4 3 2 3 2 4 3 4 in ( ) 266585.48 445.04 448.62 130.12 3.02 8.81 1 0 0.11 0.11 1.26 10 0.72 3.77 10 4.32 10 0.41 8.75 10 6.21 10 f x x x x x x x x x x x x x x x x x x x x x 2 1 2 3 4 . . 720 770 440 470 0 90 2000 4000 x R S t x x x x 3.7.4 优化处理 非线性多变量约束最优化问题使用 MATLAB 函数 fmincon,用 MATLAB 求解 的程序如下: % myproject_suting 46 function myproject_suting clc; clear all; x0=[720,440,0,2000]; w(1,1)=0.6;w(1,2)=0.4; w(2,1)=0.4;w(2,2)=0.6; for i=1:2 i [x,f]=fmincon(@(x)fun_obj(x,w(i,:)),x0,[],[],[],[],[720,440,0,2000],[770,470,90,4000]) f1=53248241.4226343-59805.30437*x(1)-134344.39872*x(2)-3504.54219*x(3)-39.80 93901*x(4)+66.4096457*x(1)*x(1)+218.2033599*x(2)*x(2)+21.21699672*x(3)*x (3)+0.0670636727*x(4)*x(4)-85.4470222*x(1)*x(2)+0.856692142*x(1)*x(3)-0.17 38673893*x(1)*x(4)+2.919832438*x(2)*x(3)-0.476665375*x(2)*x(4)-0.16422891 92*x(3)*x(4) f2=-266585.48167+445.044048*x(1)+448.620336*x(2)+130.1193323*x(3)-3.0203890 85*x(4)-0.0881271931*x(1)*x(1)+0.1148248078*x(2)*x(2)+0.1096604622*x(3)* x(3)-0.0001255389554*x(4)*x(4)-0.718714255*x(1)*x(2)+0.0376567369*x(1)*x( 3)+0.00431996374*x(1)*x(4)-0.408408858*x(2)*x(3)+0.000875159845*x(2)*x(4) +0.00621505561*x(3)*x(4) end function f1f2=fun_obj(x,ww) f1f2=ww(1)*(53248241.4226343-59805.30437*x(1)-134344.39872*x(2)-3504.54219* x(3)-39.8093901*x(4)+66.4096457*x(1)*x(1)+218.2033599*x(2)*x(2)+21.216996 72*x(3)*x(3)+0.0670636727*x(4)*x(4)-85.4470222*x(1)*x(2)+0.856692142*x(1) *x(3)-0.1738673893*x(1)*x(4)+2.919832438*x(2)*x(3)-0.476665375*x(2)*x(4)-0. 1642289192*x(3)*x(4))-ww(2)*(-266585.48167+445.044048*x(1)+448.620336*x (2)+130.1193323*x(3)-3.020389085*x(4)-0.0881271931*x(1)*x(1)+0.1148248078 *x(2)*x(2)+0.1096604622*x(3)*x(3)-0.0001255389554*x(4)*x(4)-0.718714255*x (1)*x(2)+0.0376567369*x(1)*x(3)+0.00431996374*x(1)*x(4)-0.408408858*x(2)* x(3)+0.000875159845*x(2)*x(4)+0.00621505561*x(3)*x(4)); 输出结果为: 对第一组权系数,w1=0.6,w2=0.4,x=[748 457.2 47.5 2950.1]T,f1(x) =2.9747×104mm/s2,f2(x)=798.97mm; 对第二组权系数,w1=0.4,w2=0.6,x=[748 457.2 47.5 2951.1]T,f1(x) 47 =2.9747×104mm/s2,f2(x)=799.15mm。 这两组结果都为能满足约束条件的最终解。对比分析两组最终解,除立柱跨 度 x4 值略有微小差别外,其他三个设计变量值均保持一致,车辆最大加速度和护 栏最大变形量变化幅度很小。因此,综合考虑车辆碰撞加速度和护栏变形量能在 一定范围内取得最小值,对应的护栏结构参数初步可确定为:H=748mm, h=457mm,δ=47.5mm,L=2950mm。 3.8 本章小结 本章对车辆碰撞护栏事故中的骑跨、下钻事故进行了分析,依此提出了新型护 栏(双条半刚性护栏)的设计思想,分析了双条半刚性护栏结构中主要待求参数, 对决定护栏结构参数的车辆主要结构尺寸进行了统计,提取护栏尺寸参数取值范 围;运用 DPS 统计分析软件中的均匀设计得到护栏评价指标与护栏结构参数的数 量关系;利用 MATALB 软件 fmincon 模块进行非线性多变量约束优化,获取了护 栏结构参数的最佳值,即双条半刚性护栏中,上护栏安装高度 H=748mm,下护栏 安装高度 h=457mm,上、下护栏板伸出量差值δ=47.5mm,立柱跨度 L=2950mm。 48 第四章 汽车-护栏碰撞系统仿真模型的建立 4.1 有限元建模平台 有限元法是当今工程分析领域中实用性最强,应用最为广泛的数值计算方法。 它的基本思想是将一个表示结构或连续体的求解域离散为若干子域(单元),通过 它们边界上的节点相互联成组合体;每个单元内假设的近似函数来分片地表示全 求解域内待求的未知场变量,通过建立和原问题数学模型等效的变分原理,求解 原来待求场函数的无穷多自由度问题转化为求解场函数就结点值的有限自由度问 题[45]。 本文采用的有限元软件是 LS-DYNA 和 HyperMesh 前后处理软件。 4.1.1 仿真软件 LS-DYNA LS-DYNA 软件是世界上最著名的通用显示非线性动力分析程序,最初是 1976 年在美国劳伦斯利弗莫尔国家实验室(Lawrence Livermore National Lab.)由 J.O.Hallquist 主持开发完成的,是显示有限元程序的鼻祖和理论先导 [46][47] 。 LS-DYNA 以 Lagrange 算法为主,兼有 ALE 和 Euler 算法;以显示求解为主,兼 有隐式求解功能;以结构分析为主,兼有热分析、流体-结构耦合功能;以非线性 动力分析为主,兼有静力分析功能[48]。该软件能够模拟真实世界的各种复杂几何 非线性(大位移、大转动和大应变)、材料非线性和接触非线性问题,特别适合高 速碰撞、爆炸和金属成形等非线性动力冲击问题,广泛应用于汽车工业、航空航 天、制造业、国防工业等重要领域。 4.1.2 前处理软件 HyperMesh[49][50] HyperMesh 软件是美国 Altair 公司的产品,是世界领先的、功能强大的 CAE 应用软件包,也是一个创新、开放的企业级 CAE 平台,它集成了设计与分析所需 的各种工具,具有无与伦比的性能以及高度的开放性、灵活性和友好的用户界面。 HyperMesh 软件是一个功能强大的有限元前处理平台。首先,它是一个专用 的网格划分软件,在网格自动生成、单元质量检查以及不合格单元修改等方面独 具特色;其次,能够建立各种复杂的有限元模型,配有与不同的 CAD 软件接口, 例如 UG、Pro/E、CATIA、IGES、STEP 等 CAD 软件,读入 CAD 几何模型的速 度与效率较高,减少附加的冗余数据;再次,具有强大的几何处理能力,能够快 速读取那些结构非常复杂,模型数据,从而大大提高了 CAE 分析工程师的工 作效率;最后,配有各种有限元计算软件(求解器)接口,如 ABAQUS、ANSYS、 LS-DYNA、MADYMO、PAM-CRASH、VPG 等多种求解器接口,为各种有限元 求解器写出数据文件及读取不同求解器的结果文件,可实现不同有限元计算软件 49 之间的模型转换功能。 4.1.3 汽车与护栏碰撞仿真流程 图 4.1 汽车与护栏仿真流程图 Fig.4.1 Simulation scheme between vehicle and guardrail 50 一般地,一个完整的有限元模型需要经历前处理、求解和后处理三个过程。第 一阶段(即前处理)是在 HyperMesh 软件中实现的:首先选用某款有限元汽车, 进行局部的调整,对调整后的有限元轿车模型进行模型的验证;其次,在 CATIA 软件中建立护栏和土壤的几何模型,并导入至 HyperMesh 中进行网格的划分、材 料属性的定义、单元类型的选择、各组件的连接等前处理;最后,进行模型的耦 合,设置模型的初始条件、边界条件、接触类型和沙漏控制、质量缩放等操作。 第二阶段(即求解过程)基于 LS-DYNA 软件,在计算过程中,模型很难做到一次 调试成功,因此,通常需要根据错误提示返回到前处理阶段,进行相应的修改。 第三阶段在 LS-PrePost 软件中进行后处理,若是结果不满足要求,则仍需返回至 第一阶段进行调试,直至达到预期效果。其仿真流程如图 4.1 所示。 4.2 某轿车有限元模型 由于汽车整车一般包含了成百上千个零部件,其建模工作量十分巨大,目前公 认的一个整车建模工作量是 3 人/年,所以一般情况下,在建立汽车碰撞有限元模 型时,为了减小建模的工作量,都是利用现有的汽车设计 CAD 数据来建立最初的 几何实体模型,然后进行网格划分,再给计算所需的各种边界条件、载荷条件及 约束条件等[51]。当然,本文的研究受到了时间、经费等诸多因素的限制,根据汽 车与护栏实际的碰撞需要,只能重构已有的有限元模型,对重要的碰撞部位进行 局部的网格细化,而非重要碰撞部位则粗化网格,从而为后面仿真试验提供轿车 有限元模型。 按照我国高速公路护栏安全性能评价标准(JTG/T F83-01-2004)中的初始碰撞 条件,本文在美国国家碰撞分析中心 NCAC(The National Crash Analysis Center ) 平台上选用了某款符合要求的轿车模型。其相关技术参数如表 4.1,整车几何模型 如图 4.2 所示。 表 4.1 某轿车主要技术参数 Tab.4.1 Main technical parameters of a sedan 类别 单位 参数 车长×车宽×车高 mm 5025×1840×1470 轴距 mm 2760 前轮距 mm 1568 后轮距 mm 1591 整车质量 t 1.665 51 图 4.2 某轿车几何模型 Fig.4.2 Geometric model of a certain car ①碰撞区域的划分 一般情况下,汽车与护栏发生碰撞时,汽车的碰撞形态及变形部位基本相同。 为此,将汽车车身壳体按照碰撞等级区域划分为:严重碰撞区域 I、轻微碰撞区域 II 和非碰撞区域 III。其中严重碰撞区域 I 是碰撞和变形比较严重的区域,包括: 保险杠、保险杠蒙皮、前翼子板、发动机盖等;轻微碰撞区域 II 是与护栏发生碰 撞接触,变形和影响相对较小的区域,包括:侧门框、车门、后翼子板等;而其 他部位则归类于非碰撞区域 III,此区域的车身基本不变形。如图 4.3 所示。 图 4.3 碰撞区域划分图 Fig.4.3 Devision of crash area ②网格大小的调整 对于显示有限元而言,网格尺寸的设置是非常重要的,不同的网格大小会造成 不同的计算时间,以及影响单元是否出现坍塌行为。网格越小,计算时间越长; 网格越粗,则单元易出现锯齿形状的沙漏现象。因此,合理的网格密度须在保证 实用精度的前提下尽量地节省计算时间。在严重碰撞区域网格大小设置为 10~20mm,轻微碰撞区域网格的大小为 20~40mm 左右,而非碰撞区域可大于 50mm[52]。 52 调整后,该整车模型总共有 769035 个单元,663680 个节点。其中包括壳单元 570928 个、实体单元 40184 个和 4464 个焊点等。轿车的有限元模型如图 4.4 所示。 图 4.4 整车有限元模型 Fig.4.4 Finite element model of the whole car ③单元网格质量控制和模型单元检查 模型网格划分好之后,需要对网格质量加以控制,其控制标准如下[53]: 1)翘曲角度(warpage):≤15° 2)长宽比(Aspect Ratiao):≤5 3)倾斜角度(skew angle):≤10° 4)四边形内角(angle quad):40°~135° 5)三角形内角(angle tria):20°~120° 6)雅克比(jacobian):0.7 在实际调整中,所有单元并不都能满足上述要求,在保证模型整体良好的情况 下,对局部网格可进行适当调整。其中翘曲角度上限为 30°~40°、长宽比上限为 5~6、 倾斜角度上限为 60°~70°、雅克比下限为 0.5~0.6,保证失效单元占总单元数的 10% 之内即可。 ④模型的验证 通过对原来整车模型的局部修改,车辆的碰撞性能有可能发生变化,因此需要 对修改后的整车模型进行验证。验证初始条件设置:在轿车正前方 20mm 处增设 一刚性墙,赋予轿车 x 轴方向的初速度 50km/h,与刚性墙发生正面碰撞。 下面通过整车变形、碰撞能量、速度、加速度和刚性墙受力等几个方面与原模 型报告中的相关数据进行对比分析。 53 1)整车变形 图 4.5 为模型调整前后变形的对比图。通过比较,调整后的整车模型变形与调 整前碰撞变形基本相似。 (a)调整前整车模型变形图 (b)调整后整车模型变形图 图 4.5 整车模型变形对比图 Fig.4.5 Contrast of deformation (a)调整前整车模型能量曲线图 (b)调整后整车模型能量曲线图 图 4.6 整车模型能量对比图 Fig.4.6 Contrast of energy 2)碰撞能量 图 4.6 为碰撞能量对比图,图 4.6(a)为原整车模型的碰撞能量变化曲线图,图 4.6(b)为调整后整车模型的碰撞能量变化曲线图。由于调整后模型在碰撞过程中有 摩擦力做功,因此,存在能量消耗而导致总能量略有降低。从动能和内能变化趋 势来看,两者变化趋势基本保持了一致。 3)速度曲线 图 4.7 为座椅处的速度曲线对比图,对比可得,调整前后模型被测点的速度都 是先减小至零,然后发生反弹,两者变化趋势基本保持一致。 4)加速度曲线 图 4.8 为发动机顶部加速度曲线对比图。根据规定要求对发动机顶部加速度曲 线进行 SAE 滤波器 180Hz 过滤,得到的曲线如图 4.8(b)所示。对比分析可得,发 54 动机顶部的加速度调整前后变化趋势基本保持一致。 (a)调整前座椅处速度曲线图 (b)调整后座椅处速度曲线图 图 4.7 座椅处速度曲线对比图 Fig.4.7 Contrast of velocity at the seat (a)调整前发动机顶部加速度曲线图 (b)调整后发动机顶部加速度曲线图 图 4.8 发动机顶部加速度曲线对比图 Fig.4.8 Contrast of top engine acceleration (a)调整前刚性墙受力曲线图 (b)调整后刚性墙受力曲线图 图 4.9 刚性墙受力曲线对比图 Fig.4.9 Contrast of thrust against the rigid wall 55 5)刚性墙受力 图 4.9 为刚性墙受力曲线对比图,通过比较可以看出,调整前、后的刚性墙 受到车辆碰撞力随时间变化趋势基本一致。 综上所述,通过改变严重碰撞区域、轻微碰撞区域和非碰撞区域的网格大小, 对修改后的整车模型进行了 0.13s 的碰撞试验,从碰撞能量、变形情况和加速度三 个方面对比分析可知,修改后整车模型可以很好反映真实碰撞情况,可以作为与 护栏碰撞的轿车模型。 4.3 某货车有限元模型 按照我国高速公路护栏安全性能评价标准(JTG/T F83-01-2004)中的初始碰撞 条件,本文在美国国家碰撞分析中心 NCAC(The National Crash Analysis Center ) 平台上借用某款符合要求的货车模型。其相关技术参数如表 4.2,整车模型如图 4.10 所示。 表 4.2 某货车主要技术参数 Tab.4.2 Main technical parameters of a certain truck 类别 单位 参数 车长×车宽×车高 mm 8320×2486×2884 轴距 mm 4455 前轮距 mm 1965 后轮距 mm 1770 整车质量 t 10.156 图 4.10 某货车有限元模型 Fig.4.10 Finite element model of a certain truck 56 对整车模型进行验证,验证初始条件设置:在轿车正前方 20mm 处增设一刚性 墙,赋予轿车 x 轴方向的初速度 50km/h,与刚性墙发生正面碰撞。 (a)碰撞前 (b)碰撞中 图 4.11 某货车模型正面碰撞仿真试验 Fig.4.11 Front crash simulation test of a certain truck 图 4.12 能量曲线图 Fig.4.12 Energy curve 因实验设备条件有限,无法进行货车的实车碰撞,因此,只能凭借经验,通 过模型仿真结果来判别模型的有效性。图 4.11 为该货车正面碰撞仿真试验,应力 云图可以显示货车的变形基本符合事实;图 4.12 为货车碰撞能量变化曲线图,系 统的沙漏能小于总能量的 10%,因此,基本上可以判定该模型是有效的。 4.4 护栏有限元模型 本文研究的波形护栏是在目前高速公路上应用最为普遍的双波半刚性圆形立 57 柱式护栏基础上做了一定的改进,该模型包括上波形护栏板、下波形护栏板、立 柱、上防阻块和下防阻块等几个部分组成,下面对各个部件逐一进行建模。 4.4.1 波形护栏板模型 上波形护栏板采用公路交通安全设施设计细则(JTG/T D81-2006)中[2][10]的 Am 级结构中的波形护栏板型式,波形护栏板的截面形状如图 4.13 所示,几何尺 寸如表 4.3 所示。 图 4.13 上波形护栏截面形状 图 4.14 上护栏有限元模型 Fig.4.13 Section shape of upper waveform guardrail Fig.4.14 Finite element of the upper guardrail 表 4.3 上波形护栏截面尺寸 Tab.4.3 Section size of upper waveform guardrail 代号 B M H H1 H2 E R1 R2 R3 T 尺寸(mm) 310 96 85 83 39 14 24 24 10 4 上波形护栏板的有限元模型如图 4.14 所示,单元类型采用*SECTION_SHELL 四节点壳体单元,选用 Belytschko-Tsay 单元算法,壳体单元厚度方向上采用 2 个 高斯积分 点 , 以 在适 应 塑 性变 形 的 同 时提 高 模 型 的计 算 速 度 。模 型 采 用 *MAT_PIECEWISE_LINEAR_PLASTICITY(24 号)弹塑性材料类型,其具体的 材料属性见表 4.4。 表 4.4 波形护栏模型参数 Tab.4.4 Parameters of waveform guardrail model 名称 单位 数值 密度 Rho t/mm3 7.865E-9 弹性模量 E MPa 2.0E5 泊松比 NU - 0.27 屈服应力 SIGY MPa 310 剪切模量 ETAN MPa 763 C 1/s 40 P - 5 58 下护栏板的结构形式可以设计成各式各样的,如 M. Borovinšk 等人[54]设计的 形式如图 4.15(a),谢庆喜等[55]设计的结构形式(见图 4.15(b)),这些结构形式的护 栏在防止车辆发生阻绊事故上有一定的积极作用,但下护栏板过于细长,其强度 和刚度不能满足碰撞要求,在阻止车辆下钻事故方面还有待改进之处。为弥补上 述下护栏板的不足,下护栏板可在竖直方向增加栏板的宽度,而护栏板宽度的增 加势必加大了下护栏板与车辆在发生接触碰撞时的接触面积,从而增加了车辆在 纵向方向的受力,不利于车辆行驶方向的纠正。因此,为避免此情况的发生,同 时又满足碰撞的强度和刚度要求,并且不过多的增加与碰撞车辆的接触面积,依 照上护栏板结构形式,下护栏板结构可设计为图 4.15(c)的形式。 (a)形式一 (b)形式二 (c)形式三 图 4.15 下护栏结构形式图 Fig.4.15 Structure of lower guardrail 图 4.16 下波形护栏板截面形状 图 4.17 下护栏板有限元模型 Fig.4.16 Section shape of lower waveform guardrail Fig.4.17 Finite element of the lower guardrail 表 4.5 下波形护栏板截面尺寸 Tab.4.5 Section size of lower waveform guardrail 代号 M N H1 H2 E R1 R2 T 尺寸(mm) 96 20 83 39 14 24 24 4 59 下波形护栏板截面形状见图 4.16,截面尺寸见表 4.5,有限元模型见图 4.17。 该护栏板采用的单元类型、选取的单元算法、积分点、材料属性均与上波形护栏 板一致。 4.4.2 立柱模型 根据我国《高速公路交通安全设施设计及施工技术规范》(JTJ074-94)及《公 路交通安全设施设计细则》(JTG D81-2006)对 Am 波形护栏的修订,与原双波护栏 (护栏板安装高度 600mm)相匹配的立柱总高度是 1850mm,其中 1100mm 是埋设于 地底下。而双条半刚性护栏中的上护栏板安装高度为 748mm,比原来双波护栏安 装高度高出 148mm,对应的立柱则也应随之增长,即为 1998mm,为便于实际生 产,新型护栏匹配的立柱长度取为 2000mm,圆柱外径为 114mm,厚度为 4.5mm。 其几何尺寸如图 4.18 所示,有限元模型如图 4.19 所示。 图 4.18 立柱几何尺寸 Fig.4.18 Geometric size of the column 图 4.19 立柱有限元模型 Fig.4.19 Finite element model of the column 4.4.3 防阻块模型 防阻块是波形护栏结构中重要的传力构件之一,其作用主要体现在三个方面: 其一,自身吸收部分碰撞能量,缓冲车辆碰撞,降低车辆碰撞减速度的峰值,提 高乘员安全系数;其二,将护栏板从立柱上伸出,有效防止因车辆紧靠立柱而使 前轮在立柱处发生阻绊;其三,将护栏板上的碰撞力均匀的传递给其他立柱。在 我国的行业规范中推荐使用 A 型、B 型。A 型适用于圆柱型立柱,是一种六角形 的结构。B 型适用于槽型立柱或其他立柱。本文采用 A 型防阻块,防阻块几何尺 寸如图 4.20 所示,有限元模型见图 4.21 所示。 60 图 4.20 防阻块几何尺寸 图 4.21 防阻块有限元模型 Fig.4.20 Geometric size of loss control block Fig.4.21 Finite element model of loss control block 4.4.4 护栏各组件的连接[56][57] 护栏板与防阻块、防阻块与立柱之间的相互作用关系采用焊点(spotweld)单 元来模拟螺栓的连接效果。设定焊点单元的失效力,可以在受力达到该临界力时, 焊点发生失效,可使得护栏板、防阻块和立柱相互脱离。焊点单元的失效判别准 则为: 1 m n sn ss n s f f s s 式(4.1) 其中, snf ——点焊所能承受的轴向极限拉力; ssf ——点焊所能承受的轴向极限剪切力; ns ——点焊所能承受的拉力; ss ——点焊所能承受的剪切力; m ——法向点焊指数,取值 2; n ——剪切点焊指数,取值 2。 4.5 地面模型 为较为有效的模拟实际汽车与护栏碰撞情况,也需要建立地面模型,模拟碰撞 过程中地面对立柱的约束作用。土壤材料采用(14 号材料)*MAT_SOIL_AND _FOAM_FAILU RE,该材料模型假定土体在竖直方向逐级变化,不形成分层[58][59]。 路基压实土体密度ρ=1.874×103kg/m3,泊松比 v=0.35,剪切模量 G=49.5MPa,拉伸 终止应力 pc=-0.55MPa,体积模量 K=134.55MPa[60]。土基的模型用直径为 750mm, 高度为 110mm 的圆柱体模拟,有限元模型如图 4.22 所示。 61 图 4.22 路基有限元模型 Fig.4.22 Finite element model of the roadbed 4.6 “车辆-护栏-地面”碰撞体系的耦合 4.6.1 碰撞假设与简化处理 本文研究的碰撞模型做如下假设和简化处理: ①不考虑驾驶员对车辆的紧急操控,如转向操作; ②采用五个跨度的护栏长度近似代表实际护栏的防御能力; ③护栏跨中位置作为初始碰撞点; ④上、下护栏板采用整体式,忽略实际护栏板间的螺栓连接; ⑤护栏板、防阻块和立柱的联接采用 spotweld 焊点模拟螺栓的联接; ⑥不考虑车轮的转动作用。 4.6.2 参数确定及计算控制 将前面建立好的轿车有限元模型、护栏有限元模型和地面有限元模型导入至 一个文件中,并需要对模型进行初始条件、边界条件的参数确定和接触类型、质 量缩放、沙漏控制、输出文件设置等计算控制。耦合模型如图 4.23 所示。 图 4.23 汽车与护栏碰撞耦合模型 Fig.4.23 Simulation coupled model of vehicle crash against guardrail ①初始条件 1)车辆碰撞速度 车辆与护栏发生接触瞬间的碰撞速度与正常驾驶车速是不同的。在车辆即将与 62 护栏发生碰撞时,驾驶员往往会采取一定的应急处理,比如松油门,紧急制动, 转向等措施。因此,车辆碰撞速度一般视为行驶车速的 60%~80%[22]。根据我国《高 速公路护栏安全性能评价标准》(JTG/T F83-01-2004)的要求,当某一种车型的平均 车速高于高速公路最高限速时,以高速公路最高限速的 0.8 倍考虑,本文小轿车的 碰撞速度确定为:100km/h,货车的碰撞速度为 60km/h。 2)车辆碰撞角度 车辆碰撞角度是指失控车辆冲击方向与防撞护栏纵轴所成的夹角,它与道路等 级、车辆种类、行驶速度和车辆在车道上的位置有关[22]。据交通事故统计数据显 示,汽车与中央分隔带碰撞的平均角度在 80%的情况下为 18°[61],并结合我国《高 速公路护栏安全性能评价标准》(JTG/T F83-01-2004)的碰撞初始条件,本文车辆 碰撞角度选取为 20°。 ②边界条件 实际中,土壤是连续的,因离立柱远处的土壤对模型计算结果影响不大,为节 省计算工作量,只建立以立柱为中心,r=2700mm 范围的土壤,在土壤外缘设置 6 自由度的约束;与此同时,五跨度以外的护栏受到车辆碰撞影响较小,为模拟五 跨度以外护栏构件对五跨度以内护栏构件的影响作用,对上、下护栏板两端进行 6 自由度的全约束。即: ( , , , , , , ) 0x y zg x y z t 式(4.2) 耦合模型中因考虑重力作用,采用*LOAD_BODY_Z 对系统进行了重力加速度 的加载。为防止碰撞系统出现下落现象,建立以 Z 轴为矢量的刚性墙,模拟实际 地面的约束效果。 ③接触类型 LS-DYNA 提供了许多种类的接触算法,参照有关碰撞仿真经验[19],车辆与护 栏碰撞过程中的接触定义如表 4.6 所示。 表 4.6 轿车与护栏碰撞系统中的接触类型 Tab.4.6 Contract types in the crash system of vehicle and guardrail 序列 名 称 接触类型 1 护栏板 防阻块 立柱的接触 *CONTACT_AUTOMATIC_SINGLE_SURFACE 2 车辆与护栏间的接触 *CONTACT_AUTOMATIC_NODES_TO_SURFACE 3 车轮与路面的接触 *CONTACT_AUTOMATIC_SURFACE_TO_SURFACE 4 车辆自身接触 *CONTACT_AUTOMATIC_SINGLE_SURFACE 5 立柱与土壤的接触 *CONTACT_AUTOMATIC_SURFACE_TO_SURFACE 63 ④质量缩放 对于 LS-DYNA 的显示时间积分,模型的计算时间步长是由时间步长最小的单 元决定的,其关系如下所示[46]: min min min 2/ (1 ) l lt c E 式(4.3) 式中, minl ——最小单元; ——泊松比; ——特定质量密度; E ——弹性模量。 如果模型中有少量小单元存在,其计算时间会大幅增加。一般地,可以采用 质量缩放的方法来解决这个问题。由于单元的尺寸 minl 、弹性模量 E 和泊松 对仿 真精度有至关重要的影响,不能随意更改。所以,只能通过调整材料的密度 来 适当增加时间步长。密度调整原理如式(4.4)所示[48]: 2 2 21 specifed i i t E l v 式(4.4) LS-DYNA 中提供两种质量缩放实施方案: 1)所有单元采用相同的时间步长,质量缩放加到全部单元上,DT2MS 为正; 2)只对计算时间步长小于指定时间步长的单元有效,质量缩放仅加到小于设 定值的单元上,DT2MS 为负。 本模型采用第二种方案。在进行质量缩放后,必然会导致模型质量的增加、 惯性效应的增大以及质心的改变。为保证模型计算的有效性兼顾缩短计算时间, 其增加的质量控制在总质量的 5%以内。 在 HyperMesh 中质量缩放的实现: 1)在*CONTROL_TIMESTEP 卡片中,激活时间步长缩放因子 TSSFAC,该值 取值范围一般为 0.67~0.9,为避免负体积和提高计算的稳定性,可适当缩小该值, 本文模型中采用系统默认值 0.9; 2)查看 TSSFAC=0.9 情况下整个模型不同单元类型的最小时间步长 minimume values; 3)在 failure criteria 中输入适当的时间步长,检查失效单元数量,保证失效单 元数不超过总单元数的 5%; 4)根据 TSSFAC*|DTAMS|=时间步长,计算得出 DT2MS,通过计算,本文 DT2MS 取 1.32E-6,如图 4.24 所示。 64 图 4.24 质量缩放 Fig.4.24 Mass scaling ⑤沙漏控制 沙漏现象(Hourglass modes)是一种比结构全局相应高得多的频率震荡的零能 变形模式(Zero-energy Modes)。因缩短模型计算时间,对实体单元、四边形壳体 单元和 2D 单元采用缩减积分而导致计算结果可信度的下降。沙漏是数值计算造成 的结果而不是结构本身的固有特征[62][19]。沙漏表现的特征为:系统刚度不够和单 元网格出现锯齿状形态。为保证模型具有较高的准确性和有效性,沙漏引起的能 量一般不得超过总能量的 10%,常用的沙漏控制方法有[4]: 1)调整模型的体积粘度,由于过度地改变结构的体积粘度,将对结构的整体 变形模式产生严重的负面影响,因此,通常不推荐使用此方法; 2)采用全积分。优点是不会产生沙漏现象,缺点是计算成本过高; 3)增加系统的弹性刚度。只要增加沙漏系数(Hourglassing Coefficient),就 可以达到增加系统弹性刚度的目的。然而,当沙漏系数超过 0.15 时,会导致计算 失稳。本文采用第三种方法,设置沙漏系数为 0.10。 4.7 本章小结 本章简单介绍了有限元仿真软件 LS-DYNA 和有限元前处理软件 HyperMesh。 首先对某款有限元轿车根据护栏碰撞位置划分区域,进行了局部网格的二次划分, 以正面碰撞仿真试验与原模型报告进行了该模型有效性的验证,并对某货车进行 了模型的有效验证;其次根据前一章护栏结构优化结果,建立了护栏有限元模型; 第三,构建“车辆-护栏-地面”耦合模型,以及对耦合模型进行了参数控制。 65 第五章 汽车-护栏碰撞仿真结果分析 5.1 试验方案的确定 根据第二章中各国护栏碰撞试验条件,并依据我国《高速公路护栏安全性能评 价标准》(JTG/T F83-01-2004)碰撞试验方法,拟定试验方案如下: 表 5.1 试验方案 Tab.5.1 Test scheme 试验组数 试验车型 车辆质量 (kg) 碰撞速度 (km/h) 碰撞角度 (°) 护栏形式 属 性 试验 1 小轿车 1500 100 20 双条半刚性护栏 试验组 试验 2 小轿车 1500 100 20 现有波形护栏 对比组 试验 3 大货车 10000 60 20 双条半刚性护栏 试验组 试验 4 大货车 10000 60 20 现有波形护栏 对比组 本文按照第二章中提出的三个方面的评价指标来进行,即乘员安全性能、车 辆安全性能和护栏防撞性能。 5.2 某轿车与双条半刚性护栏碰撞仿真结果分析 5.2.1 碰撞过程及能量变化 在某轿车与双条半刚性护栏碰撞仿真过程中,车辆未发生下钻事故,双条半刚 性护栏结构基本完整,导向性能好,碰撞情况如图 5.1 所示。 (a)t=0.025s 时 (b)t=0.3s 时 图 5.1 某轿车与双条半刚性护栏碰撞仿真图 Fig.5.1 Crash simulation between vehicle and double semi-rigid guardrail 66 图 5.2 碰撞能量曲线 Fig.5.2 Crash energy curve 图 5.3 某轿车重心附近节点 2000901 的加速度曲线 Fig.5.3 Acceleration curve of node 2000901 close to the center of mass 图 5.2 为碰撞能量曲线,从图中可以看出,随着碰撞过程的延续,系统动能在 缓慢的下降,内能在逐步上升,两者变化趋势平滑;系统的总能量略有下降,可 能是由于碰撞过程中车辆与护栏间的摩擦力做负功而吸收了部分能量以及碰撞热 量的散失造成的。 5.2.2 乘员安全性能 由于实验条件和时间受限,暂未将假人放入汽车与护栏碰撞系统进行仿真, 因此采用车体重心加速度来作为评判乘员安全性能的一个手段。图 5.3 为某轿车重 心附近的节点 2000901 处三个方向经过 SAE(10Hz)过滤后的加速度曲线图,可 67 以看出:X 方向的加速度波动幅度较 Y 方向小,护栏在车辆纵向产生的影响小于 横向,护栏的导向性能较好;Y 方向加速度分别在 0.06s、0.17s 和 0.21s 出均出现 峰值,车体与护栏发生了三次碰撞,即前翼子板与护栏发生碰撞、车身与护栏发 生碰撞以及车尾与护栏发生的碰撞;Z 方向加速度呈现震荡趋势,主要是由于在 Z 方向能量无法被其他部件吸收产生的一种现象。 按照每 0.1 秒以 100 次进行采样,根据式(2.4),可计算得 x、y 和 z 方向任 意 50ms 时段的平均值分别为:19.3551g 、6.9559g 和 0.4578g,根据式(2.3)得 到车辆重心附近节点处转换的乘员加速度伤害指标 ASI=1.2393。根据式(2.8)换 算成 HIC 值为:242.2609 因此,乘员安全性能基本达到要求。 5.2.3 车辆安全性能 图 5.4 为轿车行驶中心线与护栏纵向方向夹角随时间的变化曲线图。可以清晰 的看到,当 t=0s 时,车辆的碰撞角度(即驶入角度)为 20°,随护栏的变形和导向, 车辆的行驶方向在逐步恢复正常状态,最后,当 t=0.3s 时,车辆驶离护栏,驶出 角度约为 10°,小于评价标准中规定的 60%驶入角。因此,车辆安全性能较好。 0 0.05 0.1 0.15 0.2 0.25 0.30 5 10 15 20 25 (s) ( ° ) 图 5.4 某轿车行驶角度曲线图 Fig.5.4 Driving angle curve of a certain car 5.2.4 护栏防撞性能 护栏变形情况如图 5.5 所示。从图中可以看到,第三、四和五立柱处变形较为 严重,上、下护栏板变形较大,其中护栏变形量最大的节点为 42592,该点的变形 量随时间变形关系如图 5.6 所示。在快接近 0.3s 时护栏得到最大值 800mm,但仍 68 然小于标准中规定的 1000mm。因此,护栏的防撞性能满足要求。 (a)t=0.05s 时 (b)t=0.3s 时 图 5.5 双条半刚性护栏变形情况 Fig.5.5 Deformation of the double semi-rigid guardrail 图 5.6 护栏最大位移量 Fig.5.6 Max displacement of the guardrail 5.3 某轿车与现有波形护栏仿真结果分析 5.3.1 碰撞过程 图 5.7 为某轿车与现有波形护栏碰撞仿真事故,可以发现当 t=0.61s 时,轿车 前发动机盖被掀开,车体前部钻入护栏下方。由于在 t=0.65s 时,车辆与护栏发生 严重的碰撞接触,仿真出现负体积而被迫计算中断,不过可以明确地发现车辆发 生了下钻事故。通常这类事故会导致护栏侵入驾驶室,极大地削弱乘员的生存空 间,甚至造成车毁人亡的惨痛代价! 69 (a)t=0.0s 时 (b)t=0.06s 时 图 5.7 某轿车与现有波形护栏发生下钻护栏事故 Fig.5.7 Vehicle runs into the present waveform guardrail 图 5.8 某轿车重心附近节点 2000901 的加速度曲线 Fig.5.8 Acceleration curve of node 2000901 close to the center of mass 5.3.2 乘员安全性能 图 5.8 为某轿车重心附近的节点 2000901 处三个方向经过 SAE(10Hz)过滤后 的加速度曲线图。与图 5.3 相比,该图各方向的加速度均远大于图 5.4 中的加速度。 按照每 0.1 秒以 100 次进行采样,根据式(2.4),可计算得 x、y 和 z 方向任 意 50ms 时段的平均值分别为:41.8207g 、16.8484g 和 8.7005g,根据式(2.3)得 到车辆重心附近节点处转换的乘员加速度伤害指标 ASI=2.9384。根据式(2.8)换 算成 HIC 值为:2.5717e+008,远超过 1000,可见,乘员的安全无法保证。 由于乘员的安全无法保证,因此剩下的车辆安全性能和护栏防撞性能评价也 就失去意义,故不做讨论。 70 5.4 某货车与双条半刚性护栏碰撞仿真结果分析 5.4.1 碰撞过程及能量变化 在某货车与双条半刚性护栏碰撞仿真过程中,车辆未发生骑跨和翻车等事故, 双条半刚性护栏结构基本完整,导向性能好,其碰撞情况如图 5.9 所示。 (a)t=0.1s 时 (b)t=0.6s 时 图 5.9 某货车与双条半刚性护栏碰撞仿真图 Fig.5.9 Crash simulation between truck and double semi-rigid guardrail 图 5.10 碰撞能量曲线 Fig.5.10 Crash energy curve 图 5.10 为碰撞能量曲线,图中显示,随着碰撞过程的延续,系统动能在缓慢 的下降,内能在逐步上升,两者变化趋势平滑;在 0.7s 附近处,动能和内能变化 较为突然,主要是因货车即将驶离护栏时,货车尾部发生甩尾,并与护栏发生碰 撞产生的。 5.4.2 乘员安全性能 图 5.11 为某货车重心附近节点 23221 处三个方向经过 SAE(10Hz)过滤后的 加速度曲线图,可以发现:三个方向在 0.25s 附近均达到波峰,说明该时刻为货车 71 与护栏的碰撞最为激烈,而在之前的 0.6s 和之后的 0.36sX 方向也出现了波峰,是 货车前车轮与两个立柱发生了部分擦挂造成的,若没有下护栏板的防护,车轮就 会与立柱因产生阻绊效应而引发侧翻等事故。 按照每 0.1 秒以 50 次进行采样,根据式(2.4),可计算得 x、y 和 z 方向任意 50ms 时段的平均值分别为:19.64433g、5.56533g 和 3.47307g,根据式(2.3)得到 车辆重心附近节点处转换的乘员加速度伤害指标 ASI=1.2115。根据式(2.8)换算 成 HIC 值为:234.0844。可以判定,乘员安全性能基本满足要求。 图 5.11 某货车重心附近节点 23221 处加速度曲线 Fig.5.11 Acceleration curve of node 23221 close to the center of mass 0 0.1 0.2 0.3 0.4 0.5 0.6 0.7 0.80 5 10 15 20 25 (s) ( ° ) 图 5.12 某货车行驶角度曲线图 Fig.5.12 Driving angle curve of a truck 72 5.4.3 车辆安全性能 图 5.12 为货车行驶中心线与护栏纵向方向夹角随时间的变化曲线图。当 t=0s 时,车辆的碰撞角度(即驶入角度)为 20°,随护栏的变形和导向,车辆的行驶方 向在逐步恢复正常状态,最后,当 t=0.8s 时,车辆驶离护栏,驶出角度约为 11°, 小于评价标准中规定的 60%驶入角。因此,车辆安全性能较好。 5.4.4 护栏防撞性能 图 5.13 双条半刚性护栏最大位移量 Fig.5.13 Max displacement of the double semi-rigid guardrail 某货车与护栏碰撞时,护栏的变形量和之前轿车碰撞时护栏变形大为不同。 如图 5.13 所示,货车碰撞时,t=0.3s 及 t=0.65s 附近时护栏变形出现两个峰值,因 货车车身较长,先后与护栏发生两次大的碰撞,护栏才出现两次变形。最大值为 600mm,小于标准中规定的 1000mm。因此,护栏的防撞性能满足要求。 5.5 某货车与现有波形护栏仿真结果分析 5.5.1 碰撞过程 图 5.14 为某货车与现有波形护栏碰撞仿真事故。由于现有护栏高度相对货车 略有偏低,货车与其碰撞后,很容易骑跨在护栏上,乃至冲出护栏,并极有可能 与来方车辆发生二次碰撞事故,造成严重的多车事故。 5.5.2 乘员安全性能 图 5.15 为某货车重心附近节点 23221 处三个方向经过 SAE(10Hz)过滤后的 加速度曲线图。与图 5.11 比较,现有护栏给货车造成的加速度要小。原因在于货 车骑跨并冲出护栏,加速度自然叫前者小。 73 按照每 0.1 秒以 50 次进行采样,根据式(2.4),可计算得 x、y 和 z 方向任意 50ms 时段的平均值分别为 16.3928g、9.5172g 和 3.7485g,根据式(2.3)得到车辆 重心附近节点处转换的乘员加速度伤害指标 ASI=1.3894,根据式(2.8)换算成 HIC 值为:291.6036。 可以判定,乘员安全性能满足要求。 然而,该货车已骑跨并即将冲出护栏,因此,尽管乘员安全性能满足要求,但 可以认定护栏的防护基本无效。 (a)t=0.0s 时 (b)t=0.4s 时 图 5.14 某货车与现有护栏发生骑跨护栏事故 Fig.5.14 Truck runs into the present waveform guardrail 图 5.15 某货车重心附近节点 23221 处加速度曲线 Fig.5.15 Acceleration curve of node 23221 close to the center of mass 74 5.6 双条半刚性护栏与现有护栏对比分析 通过上述两组仿真对比试验,可以得到新设计的双条半刚性护栏在基本满足我 国高速公路护栏安全性能评价标准各项指标的同时,还非常有效地防止了轿车的 下钻事故、大型车的骑跨和冲出护栏事故,而现有波形护栏的弱点正在于此。由 此可见,双条半刚性护栏相对现有波形护栏还是具有一定的优势的。 当然,在仿真试验过程中,也发现了双条半刚性护栏仍需逐步完善的地方。首 先,从图 5.3 中 X 方向加速度的 10ms 平均值 19.3551g 看出,该值极为接近标准中 的临界值 20g,所以可在双条半刚性护栏“软硬”方面进行一些探讨;其次,从图 5.11 中 X 方向加速度的三个峰值可知,双条半刚性护栏立柱与车轮发生了擦挂,因此, 还需对下防阻块的“软硬”做深入的研究。 5.7 本章小结 本章主要内容是进行了两组对比试验,第一组是某轿车先后与双条半刚性护栏 碰撞仿真试验和现有波形护栏的碰撞仿真试验,第二组是某货车与双条半刚性护 栏碰撞仿真试验以及现有波形护栏的碰撞仿真试验,从三个护栏安全评价指标对 双条半刚性护栏进行了安全评价,得出该护栏在基本满足评价指标的前提下,十 分有效地防止了轿车的下钻事故和大型车骑跨、冲出护栏事故的发生。 75 第六章 结论与展望 6.1 结论 本文主要通过汽车与护栏碰撞仿真试验,研究了一种新型防撞护栏(即双条半 刚性护栏)以适应高速公路车辆微型化和重型化不同的防撞要求。本文主要结论 如下: ①对比和总结了国内外护栏防撞试验方法和安全评价标准,并分析了我国高速 公路护栏安全评价标准中,乘员安全评价指标的头部性能指标 HIC 采用《实车正 面碰撞乘员保护设计规则》中规定值 1000 存在一定偏差,研究表明,护栏碰撞中 乘员头部性能指标 HIC 取 557.45 为宜。 ②研究了车辆与护栏发生碰撞产生的骑跨和下钻事故机理,建立了车辆骑跨事 故的数学模型,为新型护栏的设计提供理论基础。 ③提出了新型防撞护栏结构,采用上、下双条半刚性护栏基本结构形式,并在 理论上分析了该护栏可有效防止车辆发生下钻事故和骑跨事故。 ④运用均匀设计试验方法和 MATLAB 软件 fmincon 非线性多变量约束优化, 确定双条半刚性护栏的基本参数,即上护栏板中心安装高度 H=748mm,下护栏中 心安装高度 h=457mm , 上、 下护 栏板 伸出 量差 值δ=47.5mm 以 及立 柱跨 度 L=2950mm。 ⑤构建了“汽车-护栏-地面”有限元模型,进行了碰撞仿真试验,与现有护栏进 行对比分析,验证了双条半刚性护栏基本达到了车辆微型化、大型化和重型化的 防护要求。 6.2 展望 由于时间及作者知识水平有限,尚有待进一步完善的地方: ①本文采用的汽车模型较少,无法进一步验证双条双波护栏的防撞性能,希望 今后完成其他车辆与双条半刚性护栏碰撞仿真试验和实车碰撞试验,以验证和修 正新型护栏的局部结构参数。 ②因新型护栏的设计影响因素众多,而且工作量十分巨大,本文只考虑了其中 比较重要的四个因素,这显然是不够全面的,比如:没有考虑该护栏立柱掩埋深 度,护栏板厚度及上、下护栏板硬度比等对防撞功能的影响等。 ③本文未把假人和乘员约束系统纳入碰撞仿真模型。现目前使用的假人只是针 对正面碰撞和侧面碰撞的,暂未出现兼顾正碰和侧碰的假人。因此,适用于非完 全正碰和非完全侧碰的假人有待开发和研究。 76 致 谢 本文是在导师刘建勋副教授的精心指导下完成的。刘老师渊博的学识、严谨、 求实的治学态度,孜孜不倦、勤于探索的精神,忘我、踏实的工作作风,以及豁 达开朗的人生态度都给作者留下了深刻的印象,使作者受益匪浅。在生活上,刘 老师更给予了无私的关怀和帮助,使作者深受感动,在此向刘老师表示衷心的感 谢和崇高的敬意! 感谢各位专家、教授在百忙之中来评阅论文、参加答辩! 感谢闫宏涛、郭庆祥、闫利勇、朱超、张翼峰、吴卓键、周莎、张艳、周宗 丽等同学在研究生期间给予作者的帮助和支持! 向所有关心和帮助过作者的老师和同学表示衷心的感谢! 最后感谢最亲爱的家人,感谢他们多年来在物质和精神上不遗余力的支持、 关心和鼓励!正是他们无微不至的关心,理解和支持,激励着作者不断前行,直 至顺利完成学业,并将永远激励着作者在新的征途中不断前进! 77 参考文献 [1] 雷正保. 大力开展半刚性护栏防撞新机理的研究[J]. 振动与冲击. 2002. 21(1):1-6 [2] JTJ074-94. 高速公路交通安全设施设计及施工技术规范[S].北京:交通出版社,1994. [3] 2000-2007 年全国道路交通事故统计数据[J]. 道路交通与安全. 2008. 8(4). [4] 雷正保,谢玉洪,李海侠. 大变形结构的耐撞性[M].长沙:国防科技大学出版社,2005.5:2-40. [5] 刘东,马社强,牛学军. 我国高速公路交通事故特点分析[J]. 中国人民公安大学学报(自然科 学版). 2008. (4):65-68. [6] 唐铮铮,贡锁白. 路侧护栏设计[J].公路交通科技,2001, 18 (3):75-78. [7] 谢玉洪,雷正保,李海侠,宁英. 高速公路防撞护栏的研究现状与发展趋势[J]. 工程建设与设 计. 2003. (12):40-43. [8] 周延朝. 波形梁护栏碰撞仿真实验研究[D].重庆:重庆交通大学,2009,6. [9] 谢玉洪. 高度自适应半刚性护栏的研究[D].长沙:长沙理工大学,2004.4:3-20. [10] JTG/T D81-2006.公路交通安全设施设计细则[S].北京:人民交通出版社,2006:8-9 [11] Bank L.C., T.R. Gentry. Development of a pultruded composite material highway guardrail [J] Gentry/Composities:Part A 32 ,2001:1329-1338. [12] Engstrand.K.E., Improvements to the Weak-Post W-Beam Guardrail[D]. Worcester: Worcester Polytechnic Institute, 2000. [13] Vesenjak M., Z. Ren. Improving the roadside safety with computational simulations.[C] // DYNA more GmhH, 4th European LS-DYNA Users Conference,Germany,.2003, 21-32. [14] Borovinšk M.,M.Vesenjak,M.Ulbin,Z.Ren,Simulation of crash tests for high containment levels of road safety barriers[J]. Engineering Failure Analysis,2007(14):1711–1718. [15] Reid J.D., D.L.Sicking, R.K.Faller, B.G.Pfeifer. Development of a New Guardrail System[J]. Transportation Research Record 1599, Transportation Research Board, 1997. [16] Faller, R.K., K.A. Polivka, B.D. Kuipers, B.W. Bielenberg, J.D. Reid, J.R. Rohde, and D.L. Sicking, “Midwest Guardrail System for Standard and Special Applications”[J] Transportation Research Record No. 1890, Transportation Research Board, 2004:19-33. [17] Sicking, D.L., J.D. Reid, J.R. Rohde. Development of the Midwest Guardrail System[J] Transportation Research Record, Paper No.02-3157,2002:44-52. [18] Marzougui, D., P. Mohan, S. Kan, and K. Opiela, Evaluation of Rail Height Effects on the safety Performance of W-Beam Barriers[C] Gothenburg, Sweden : In Proceedings of the 6th European LSDYNA User’s Conference, 2007:1-20. [19] 毛娟娟. 客车与半刚性护栏碰撞的有限元分析与模拟[D].大连:大连理工大学,2008,12. 78 [20] 贾翠平. 汽车与高速公路混凝土护栏碰撞事故分析及仿真研究[D].武汉:武汉理工大学, 2007,11. [21] 黄红武.轿车与高速公路护栏碰撞事故分析及仿真研究[D].长沙:湖南大学,2003,3. [22] 赖跃.重型车辆与半刚性护栏碰撞的有限元分析[D].上海:同济大学,2006,2. [23] Bronstad. M.E., J.D.Michie, “Recommended Procedures for Vehicle Crash Testing of Highway Appurtenances.” NCHRP Report 153 [R]. Washington, D.C.:Transportation Research Board, 1974. [24] Michie J.D., “Recommended Procedures for the Safety Performance Evaluation of Highway Appurtenances.” NCHRP Report 230 [R]. Washington, D.C.:Transportation Research Board, 1981. [25] Ross, Jr., H. E., D. L. Sicking, R. A. Zimmer, and J. D. Michie, “Recommended Procedures for the Safety Performance Evaluation of Highway Features.” NCHRP Report 350[R]. Washington, D.C. Transportation Research Board, 1993. [26] 于树平,乔希永. 国内外高速公路安全护栏试验方法及评价标准的分析研究.[C] 大连:中 国汽车工程学会第七届汽车安全技术会议. 2002. 131-139. [27] Transportation Research Board National Research Council,NCHRP Report 350[S].Washington, D.C.:National Academy Press,1993.:15-16. [28] EUROPEAN STANDARD BS EN1317-2:1998 “Road Restraint Systems. Part2:Performance Classes, Impact Test Acceptance Criteria and Test Methods for Safety Berries ” CEN 1998. [29] JTG D81-2006. 公路交通安全设施设计规范[S].北京:人民交通出版社,2006. [30] 于数平,乔希永,王维,杨瑞峰. 护栏碰撞试验乘员加速度伤害指标 ASI 与头部损伤指标 HIC 相关性研究[C]. 2004 汽车安全技术国际会议. 2004:99-104. [31] 贾宁,白书锋,张颖,闫书明. 车辆碰撞护栏时的乘员风险评价[OL].[2011-4-3]. http://www. docin.com/p-27618178.html [32] JTG/TF83-01-2004. 高速公路护栏安全性能评价标准[S].北京:人民交通出版社,2004: 8-10. [33] 张金换,杜汇良,马春生.汽车碰撞安全性设计[M].北京:清华大学出版社,2010.2:32-36. [34] Shojaati,M., Correlation between injury risk and impact severity index ASI[C]. Monte Verità / Ascona:3rd Swiss Transport Research Conference,2003. Bmst. Passenger Safety on Modern Vehicle Restraint Systems[C]. lisbon :16th IRF World Road Meeting.2010,5 [35] 黄红武, 莫劲翔, 杨济匡, 钟志华. 影响护栏防护性能的相关因素研究[J]. 湖南大学学报 (自然科学版). 2004. 31(2):45-47. [36] 何勇. 我国的护栏设计条件及波形梁护栏结构机理[J].公路交通科技. 1994. 11(2). 30-35. [37] 丁桦,贾日学. 汽车与护拦碰撞特性的研究:车与波形梁护拦碰撞过程的力学模型[J]. 中国 79 公路学报. 1996. 9(3):85-90. [38] 马力. 中国汽车市场最近十年发展态势分析[J]. 世界汽车,2003,(1):13-14. [49] 廖林清.现代设计方法[M].重庆:重庆大学出版社,2000,9. [40] 卢险峰. 优化设计导引[M].北京:化学工业出版社,2010.2. [41] 均匀设计方法[OL].(2011-4-7)http://baike.baidu.com/view/1330522?fromTaglist. [42] 均匀设计[OL].(2011-4-7)http://www.boraid.com/baike/doc.asp?id=18419. [43] 刘华,万建平. 均匀试验设计的方法与应用[J]. 阜阳师范学院学报(自然科学版). 2003. 20(1):12-16. [44] 李元科.工程最优设计[M].北京:清华大学出版社,2006.8:155-157. [45] 王勖成. 有限元法[M]. 北京:清华大学出版社,2003. 1-2. [46] 何涛,杨竞,金鑫. ANSYS 10.0/LS-DYNA 非线性有限元分析实例指导教程[M].北京:机械 工业出版社, 2007:5-12. [47] 徐文岷. 汽车碰撞过程的有限元数值模拟[D] 哈尔滨:哈尔滨工程大学,2007:31-33. [48] 赵海鸥. LS-DYNA 动力学分析指南[M].北京:兵器工业出版社,2003:1-25. [49] HyperMesh 百度百科[OL].(2011-4-7)http://baike.baidu.com/view/1988251.htm. [50] 于开平,周传月,谭惠丰. HyperMesh 从入门到精通[M].北京:科学出版社,2005:7-12. [51] 钟志华,张维钢,何文. 汽车碰撞安全技术[M].北京:机械工业出版社,2003:77-78. [52] 陈晓东,尹同耀,朱西产,冯琦,程勇. 汽车侧面碰撞计算机仿真方法[J].汽车工程. 2004. 26(1): 65-69. [53] 王祥. 汽车侧面碰撞安全性设计与优化[D].长沙:湖南大学,2009. [54] Borovinšk M., M.Vesenjak, M.Ulbin, Z.Ren,Simulation of crash tests for high containment levels of road safety barriers[J]. Engineering Failure Analysis,2007(14):1711–1718. [55] 谢庆喜, 张维刚, 钟志华. 波形梁半刚性护栏与汽车碰撞的仿真分析及其结构优化[J]. 客 车技术与研究. 2006. 28(1):10-12. [56] 胡高贤. 土基对波形梁护栏安全性能影响的传真研究[D].长沙:湖南大学,2007.3. [57] C A Plaxico , F Mozzarelli and M H Ray. Tests and simulation of a w-beam rail-to-post connection [J]. Worcester Polytechnic Institute,Worcester,2003,8(6):543-550. [58] 胡高贤,张维刚. 汽车与波形梁护栏碰撞的仿真研究[J].北京汽车.2007,(2):22-25. [59] 张维刚,胡高贤. 土基中波形梁护栏立柱的有限元模型研究[J]. 公路交通科技. 2007, 24(7):143-146. [60] SCHAUER D, F. TOKARZ, G, KAY. Preliminary vehicle in pact simulation technology advancement[M] Publication ,NO.FHWA-RD-96-059,Federal Highway Administration,1997. [61] 姚启明,孙利. 汽车冲击防撞护栏的运动响应分析[J]. 沈阳建筑工程学院学报(自然科学 版),2002,18(4):250-253. 80 [62] 尚晓江,苏建宇. ANSYS/LS-DYNA 动力分析方法与工程实践[M].北京:中国水利水电出 版社,2006. 81 在学期间发表的论著及取得的科研成果 一、在校期间发表的论文 [1] 刘建勋,唐辉,苏云. 大客车火灾智能预警及灭火系统研究[J].重庆科技学院学报(自然科学 版),2011,13(1):151-154. 二、在校期间参与的科研项目 [1] 参与《重庆市出租汽车驾驶员从业人员资格培训试题库构建》工作; [2] 参与《重庆市出租汽车驾驶员从业资格培训教材》编写; [3] 参与导师的重庆市自然科学基金项目“基于交通安全预警下的汽车驾驶员醉酒状态操作行 为规律研究” 申报工作; [4] 参与导师的重庆市交通科学技术项目“重庆市公交天然气大客车传动系节能降耗实用技术 研究”申报工作。 82 附录 汽车与护栏碰撞试验仿真图 一、试验 1: 某轿车与双条半刚性护栏碰撞仿真试验 83 附图 1 某轿车与双条半刚性护栏碰撞视图一 84 t=0.25s t=0.05s t=0.075s t=0.1s t=0.125s t=0.15s t=0.175s t=0.2s t=0.225s t=0.25s t=0.275s t=0.3s 附图 2 某轿车与双条半刚性护栏碰撞视图二 85 t=0.025s t=0.05s t=0.075s t=0.1s t=0.125s t=0.15s t=0.175s t=0.2s t=0.225s t=0.25s t=0.275s t=0.3s 附图 3 双条半刚性护栏变形图 二、试验 2: 某轿车与现有波形护栏碰撞仿真试验 附图 4 某轿车与现有波形护栏发生下钻事故视图一 86 t=0.1s t=0.2s t=0.3s t=0.4s t=0.5s t=0.6s 附图 5 某轿车与现有波形护栏发生下钻事故视图二 三、试验 3 某货车与双条半刚性护栏碰撞仿真试验 t=0s t=0.1s t=0.2s t=0.3s t=0.4s t=0.5s t=0.6s t=0.7s t=0.8s 附图 6 某货车与双条半刚性护栏碰撞视图一 t=0s t=0.1s t=0.2s t=0.3s t=0.4s t=0.5s 87 t=0.6s t=0.7s t=0.8s 附图 7 某货车与双条半刚性护栏碰撞视图二 t=0s t=0.1s t=0.2s t=0.3s t=0.4s t=0.5s t=0.6s t=0.7s t=0.8s 附图 8 双条半刚性护栏变形图 四、试验 4 某货车与现有波形护栏碰撞仿真试验 附图 9 某货车与现有波形护栏发生骑跨事故视图一 88 t=0s t=0.05s t=0.1s t=0.15s t=0.2s t=0.25s t=0.3s t=0.35s t=0.4s 附图 10 某货车与现有波形护栏发生骑跨事故视图二 t=0s t=0.05s t=0.1s t=0.15s t=0.2s t=0.25s t=0.3s t=0.35s t=0.4s 附图 11 现有波形护栏变形图查看更多